00000070392020FYFalseus-gaap:LongTermDebtNoncurrentus-gaap:LongTermDebtNoncurrentus-gaap:LongTermDebtCurrentus-gaap:LongTermDebtCurrentP2Y00000070392020-01-012020-12-31iso4217:USD00000070392020-06-30xbrli:shares00000070392021-02-2600000070392020-12-3100000070392019-12-31iso4217:USDxbrli:shares0000007039us-gaap:ProductMember2020-01-012020-12-310000007039us-gaap:ProductMember2019-01-012019-12-310000007039us-gaap:ProductMember2018-01-012018-12-310000007039us-gaap:ServiceMember2020-01-012020-12-310000007039us-gaap:ServiceMember2019-01-012019-12-310000007039us-gaap:ServiceMember2018-01-012018-12-3100000070392019-01-012019-12-3100000070392018-01-012018-12-310000007039us-gaap:CommonStockMember2017-12-310000007039us-gaap:AdditionalPaidInCapitalMember2017-12-310000007039us-gaap:TreasuryStockMember2017-12-310000007039us-gaap:RetainedEarningsMember2017-12-310000007039us-gaap:ParentMember2017-12-310000007039us-gaap:NoncontrollingInterestMember2017-12-3100000070392017-12-310000007039us-gaap:AdditionalPaidInCapitalMember2018-01-012018-12-310000007039us-gaap:ParentMember2018-01-012018-12-310000007039us-gaap:CommonStockMember2018-01-012018-12-310000007039us-gaap:TreasuryStockMember2018-01-012018-12-310000007039us-gaap:RetainedEarningsMember2018-01-012018-12-310000007039us-gaap:CommonStockMember2018-12-310000007039us-gaap:AdditionalPaidInCapitalMember2018-12-310000007039us-gaap:TreasuryStockMember2018-12-310000007039us-gaap:RetainedEarningsMember2018-12-310000007039us-gaap:ParentMember2018-12-310000007039us-gaap:NoncontrollingInterestMember2018-12-3100000070392018-12-310000007039us-gaap:AdditionalPaidInCapitalMember2019-01-012019-12-310000007039us-gaap:ParentMember2019-01-012019-12-310000007039us-gaap:CommonStockMember2019-01-012019-12-310000007039us-gaap:TreasuryStockMember2019-01-012019-12-310000007039us-gaap:RetainedEarningsMember2019-01-012019-12-310000007039us-gaap:CommonStockMember2019-12-310000007039us-gaap:AdditionalPaidInCapitalMember2019-12-310000007039us-gaap:TreasuryStockMember2019-12-310000007039us-gaap:RetainedEarningsMember2019-12-310000007039us-gaap:ParentMember2019-12-310000007039us-gaap:NoncontrollingInterestMember2019-12-310000007039us-gaap:AdditionalPaidInCapitalMember2020-01-012020-12-310000007039us-gaap:ParentMember2020-01-012020-12-310000007039us-gaap:CommonStockMember2020-01-012020-12-310000007039us-gaap:RetainedEarningsMember2020-01-012020-12-310000007039us-gaap:CommonStockMember2020-12-310000007039us-gaap:AdditionalPaidInCapitalMember2020-12-310000007039us-gaap:TreasuryStockMember2020-12-310000007039us-gaap:RetainedEarningsMember2020-12-310000007039us-gaap:ParentMember2020-12-310000007039us-gaap:NoncontrollingInterestMember2020-12-31xbrli:pure0000007039trec:AmakMember2020-12-310000007039trec:PiocheElyValleyMinesIncMember2020-12-31iso4217:SARiso4217:USD0000007039us-gaap:CustomerConcentrationRiskMemberus-gaap:SalesRevenueNetMember2020-01-012020-12-310000007039us-gaap:CustomerConcentrationRiskMemberus-gaap:SalesRevenueNetMember2019-01-012019-12-310000007039us-gaap:CustomerConcentrationRiskMemberus-gaap:SalesRevenueNetMember2018-01-012018-12-310000007039us-gaap:AccountsReceivableMember2020-12-310000007039us-gaap:AccountsReceivableMember2019-12-310000007039us-gaap:GeographicConcentrationRiskMemberus-gaap:SalesRevenueNetMember2020-01-012020-12-310000007039us-gaap:GeographicConcentrationRiskMemberus-gaap:SalesRevenueNetMember2019-01-012019-12-310000007039us-gaap:GeographicConcentrationRiskMemberus-gaap:SalesRevenueNetMember2018-01-012018-12-31iso4217:SAR0000007039trec:AmakMember2019-09-222019-09-220000007039trec:AmakMember2019-12-310000007039trec:AmakMember2020-07-012020-09-300000007039trec:AmakMember2020-09-300000007039trec:AmakMember2020-09-280000007039trec:AmakMember2020-03-260000007039trec:AmakMember2020-03-262020-03-2600000070392020-03-262020-03-260000007039us-gaap:ForeignCountryMember2020-03-2600000070392020-09-300000007039us-gaap:ForeignCountryMembertrec:AmakMember2020-01-012020-12-310000007039trec:AmakMemberus-gaap:SubsequentEventMember2021-01-010000007039trec:SaudiIndustrialDevelopmentFundLimitedGuaranteeMember2020-12-310000007039us-gaap:DiscontinuedOperationsDisposedOfBySaleMembertrec:InvestmentInAlMasaneAlKobraMiningCompanyAMAKMember2020-01-012020-12-310000007039us-gaap:DiscontinuedOperationsDisposedOfBySaleMembertrec:InvestmentInAlMasaneAlKobraMiningCompanyAMAKMember2019-01-012019-12-310000007039us-gaap:DiscontinuedOperationsDisposedOfBySaleMembertrec:InvestmentInAlMasaneAlKobraMiningCompanyAMAKMember2018-01-012018-12-310000007039trec:AmakMember2020-12-310000007039trec:AmakMember2020-01-012020-09-300000007039trec:AmakMember2019-01-012019-12-310000007039trec:AmakMember2018-01-012018-12-310000007039trec:AmakMember2020-09-300000007039trec:AmakMember2019-12-310000007039trec:AmakMember2020-01-012020-09-300000007039trec:AmakMember2019-01-012019-12-310000007039trec:AmakMember2018-01-012018-12-310000007039trec:PlatinumCatalystMember2020-12-310000007039trec:PlatinumCatalystMember2019-12-310000007039trec:CatalystMember2020-12-310000007039trec:CatalystMember2019-12-310000007039us-gaap:LandMember2020-12-310000007039us-gaap:LandMember2019-12-310000007039us-gaap:MachineryAndEquipmentMember2020-12-310000007039us-gaap:MachineryAndEquipmentMember2019-12-310000007039us-gaap:ConstructionInProgressMember2020-12-310000007039us-gaap:ConstructionInProgressMember2019-12-310000007039us-gaap:CostOfSalesMember2020-01-012020-12-310000007039us-gaap:CostOfSalesMember2019-01-012019-12-310000007039us-gaap:CostOfSalesMember2018-01-012018-12-310000007039us-gaap:SellingGeneralAndAdministrativeExpensesMember2020-01-012020-12-310000007039us-gaap:SellingGeneralAndAdministrativeExpensesMember2019-01-012019-12-310000007039us-gaap:SellingGeneralAndAdministrativeExpensesMember2018-01-012018-12-310000007039trec:SpecialtyWaxSegmentMember2019-01-012019-12-310000007039us-gaap:CustomerRelationshipsMember2020-12-310000007039us-gaap:NoncompeteAgreementsMember2020-12-310000007039us-gaap:LicensingAgreementsMember2020-12-310000007039us-gaap:DevelopedTechnologyRightsMember2020-12-310000007039us-gaap:CustomerRelationshipsMember2019-12-310000007039us-gaap:NoncompeteAgreementsMember2019-12-310000007039us-gaap:LicensingAgreementsMember2019-12-310000007039us-gaap:DevelopedTechnologyRightsMember2019-12-31trec:patentutr:acre00000070392020-09-012020-09-300000007039trec:AmendedAndRestatedCreditAgreementFourthAmendmentMemberus-gaap:RevolvingCreditFacilityMember2020-12-310000007039trec:AmendedAndRestatedCreditAgreementFourthAmendmentMembertrec:TermLoanMember2020-12-310000007039trec:ARCAgreementMemberus-gaap:RevolvingCreditFacilityMember2020-12-310000007039srt:MinimumMembertrec:AmendedAndRestatedCreditAgreementFourthAmendmentMemberus-gaap:LondonInterbankOfferedRateLIBORMemberus-gaap:RevolvingCreditFacilityMember2020-12-310000007039trec:AmendedAndRestatedCreditAgreementFourthAmendmentMembersrt:MaximumMemberus-gaap:LondonInterbankOfferedRateLIBORMemberus-gaap:RevolvingCreditFacilityMember2020-12-310000007039srt:MinimumMembertrec:AmendedAndRestatedCreditAgreementFourthAmendmentMemberus-gaap:RevolvingCreditFacilityMemberus-gaap:BaseRateMember2020-12-310000007039trec:AmendedAndRestatedCreditAgreementFourthAmendmentMembersrt:MaximumMemberus-gaap:RevolvingCreditFacilityMemberus-gaap:BaseRateMember2020-12-310000007039srt:MinimumMembertrec:AmendedAndRestatedCreditAgreementFourthAmendmentMemberus-gaap:RevolvingCreditFacilityMember2020-01-012020-12-310000007039trec:AmendedAndRestatedCreditAgreementFourthAmendmentMembersrt:MaximumMemberus-gaap:RevolvingCreditFacilityMember2020-01-012020-12-310000007039trec:AmendedAndRestatedCreditAgreementFourthAmendmentMemberus-gaap:RevolvingCreditFacilityMember2020-01-012020-12-310000007039trec:TOCCOMembertrec:AmendedAndRestatedCreditAgreementFourthAmendmentMember2020-12-310000007039trec:TOCCOMembertrec:AmendedAndRestatedCreditAgreementFourthAmendmentMember2019-12-310000007039srt:MinimumMembertrec:TOCCOMembertrec:AmendedAndRestatedCreditAgreementFourthAmendmentMember2020-01-012020-12-310000007039srt:MinimumMembertrec:TOCCOMembertrec:AmendedAndRestatedCreditAgreementFourthAmendmentMember2019-01-012019-12-310000007039trec:TermLoanMembertrec:AcquisitionTermLoanMember2020-01-012020-09-300000007039trec:TermLoanMembertrec:AcquisitionTermLoanMember2020-09-300000007039trec:AmendedAndRestatedCreditAgreementFourthAmendmentMember2018-12-310000007039trec:ARCAgreementMember2018-12-310000007039trec:AmendedAndRestatedCreditAgreementFourthAmendmentMemberus-gaap:RevolvingCreditFacilityMember2019-12-310000007039trec:AmendedAndRestatedCreditAgreementFourthAmendmentMembertrec:TermLoanMember2019-12-310000007039trec:PPPLoansMembertrec:CARESActMember2020-05-062020-05-060000007039trec:PPPLoansMembertrec:CARESActMember2020-05-060000007039trec:StockOptionPlanForKeyEmployeesMember2008-07-310000007039trec:TrecoraResourcesStockAndIncentivePlanMember2012-06-300000007039trec:StockOptionPlanForKeyEmployeesMemberus-gaap:EmployeeStockOptionMember2020-01-012020-12-310000007039srt:MinimumMembertrec:StockOptionPlanForKeyEmployeesMemberus-gaap:EmployeeStockOptionMember2020-01-012020-12-310000007039srt:MaximumMembertrec:StockOptionPlanForKeyEmployeesMemberus-gaap:EmployeeStockOptionMember2020-01-012020-12-310000007039trec:EmployeeStockOptionAndWarrantMembertrec:StockOptionPlanForKeyEmployeesMember2020-01-012020-12-310000007039trec:EmployeeStockOptionAndWarrantMembertrec:StockOptionPlanForKeyEmployeesMember2019-01-012019-12-310000007039trec:EmployeeStockOptionAndWarrantMembertrec:StockOptionPlanForKeyEmployeesMember2018-01-012018-12-310000007039trec:EmployeeStockOptionAndWarrantMembertrec:StockOptionPlanForKeyEmployeesMember2019-12-310000007039trec:EmployeeStockOptionAndWarrantMembertrec:StockOptionPlanForKeyEmployeesMember2020-12-310000007039us-gaap:CommonStockMembertrec:StockOptionPlanForKeyEmployeesMemberus-gaap:EmployeeStockOptionMember2020-12-310000007039trec:StockOptionPlanForKeyEmployeesMemberus-gaap:EmployeeStockOptionMember2018-01-012018-12-310000007039trec:StockOptionPlanForKeyEmployeesMemberus-gaap:EmployeeStockOptionMember2019-01-012019-12-310000007039trec:StockOptionPlanForKeyEmployeesMember2020-12-310000007039trec:StockOptionPlanForKeyEmployeesMembersrt:ChiefExecutiveOfficerMemberus-gaap:EmployeeStockOptionMember2018-01-012018-12-310000007039srt:MinimumMemberus-gaap:RestrictedStockUnitsRSUMembertrec:TrecoraResourcesStockAndIncentivePlanMember2020-01-012020-12-310000007039srt:MaximumMemberus-gaap:RestrictedStockUnitsRSUMembertrec:TrecoraResourcesStockAndIncentivePlanMember2020-01-012020-12-310000007039us-gaap:RestrictedStockUnitsRSUMembertrec:TrecoraResourcesStockAndIncentivePlanMember2019-12-310000007039us-gaap:RestrictedStockUnitsRSUMembertrec:TrecoraResourcesStockAndIncentivePlanMember2020-01-012020-12-310000007039us-gaap:RestrictedStockUnitsRSUMembertrec:TrecoraResourcesStockAndIncentivePlanMember2020-12-310000007039trec:CARESActMember2020-03-270000007039trec:CARESActMember2020-12-310000007039trec:CARESActMember2020-03-272020-03-27trec:Segment0000007039us-gaap:OperatingSegmentsMembertrec:PetrochemicalSegmentMember2020-01-012020-12-310000007039us-gaap:OperatingSegmentsMembertrec:SpecialtyWaxSegmentMember2020-01-012020-12-310000007039us-gaap:CorporateNonSegmentMember2020-01-012020-12-310000007039us-gaap:OperatingSegmentsMembertrec:PetrochemicalSegmentMember2020-12-310000007039us-gaap:OperatingSegmentsMembertrec:SpecialtyWaxSegmentMember2020-12-310000007039us-gaap:CorporateNonSegmentMember2020-12-310000007039srt:ConsolidationEliminationsMember2020-12-310000007039us-gaap:OperatingSegmentsMembertrec:PetrochemicalSegmentMember2019-01-012019-12-310000007039us-gaap:OperatingSegmentsMembertrec:SpecialtyWaxSegmentMember2019-01-012019-12-310000007039us-gaap:CorporateNonSegmentMember2019-01-012019-12-310000007039us-gaap:OperatingSegmentsMembertrec:PetrochemicalSegmentMember2019-12-310000007039us-gaap:OperatingSegmentsMembertrec:SpecialtyWaxSegmentMember2019-12-310000007039us-gaap:CorporateNonSegmentMember2019-12-310000007039srt:ConsolidationEliminationsMember2019-12-310000007039us-gaap:EmployeeStockOptionMember2020-01-012020-12-3100000070392020-01-012020-03-3100000070392020-04-012020-06-3000000070392020-07-012020-09-3000000070392020-10-012020-12-3100000070392019-01-012019-03-3100000070392019-04-012019-06-3000000070392019-07-012019-09-3000000070392019-10-012019-12-310000007039srt:BoardOfDirectorsChairmanMember2020-01-012020-12-310000007039srt:BoardOfDirectorsChairmanMember2019-01-012019-12-310000007039srt:BoardOfDirectorsChairmanMember2018-01-012018-12-310000007039us-gaap:AccountsPayableAndAccruedLiabilitiesMember2019-12-310000007039us-gaap:OtherPostretirementBenefitPlansDefinedBenefitMember2020-12-310000007039us-gaap:OtherPostretirementBenefitPlansDefinedBenefitMember2019-12-310000007039us-gaap:OtherPostretirementBenefitPlansDefinedBenefitMember2020-01-012020-12-310000007039us-gaap:OtherPostretirementBenefitPlansDefinedBenefitMember2019-01-012019-12-310000007039us-gaap:ValuationAllowanceOfDeferredTaxAssetsMember2017-12-310000007039us-gaap:ValuationAllowanceOfDeferredTaxAssetsMember2018-01-012018-12-310000007039us-gaap:ValuationAllowanceOfDeferredTaxAssetsMember2018-12-310000007039us-gaap:ValuationAllowanceOfDeferredTaxAssetsMember2019-01-012019-12-310000007039us-gaap:ValuationAllowanceOfDeferredTaxAssetsMember2019-12-310000007039us-gaap:ValuationAllowanceOfDeferredTaxAssetsMember2020-01-012020-12-310000007039us-gaap:ValuationAllowanceOfDeferredTaxAssetsMember2020-12-310000007039us-gaap:AllowanceForCreditLossMember2017-12-310000007039us-gaap:AllowanceForCreditLossMember2018-01-012018-12-310000007039us-gaap:AllowanceForCreditLossMember2018-12-310000007039us-gaap:AllowanceForCreditLossMember2019-01-012019-12-310000007039us-gaap:AllowanceForCreditLossMember2019-12-310000007039us-gaap:AllowanceForCreditLossMember2020-01-012020-12-310000007039us-gaap:AllowanceForCreditLossMember2020-12-310000007039trec:AmakMember2020-01-012020-12-310000007039trec:AmakMember2020-12-310000007039trec:AmakMember2019-12-310000007039trec:AmakMember2019-01-012019-12-310000007039trec:AmakMember2018-01-012018-12-310000007039trec:AmakMemberus-gaap:CommonStockMember2017-12-310000007039us-gaap:AdditionalPaidInCapitalMembertrec:AmakMember2017-12-310000007039trec:AmakMemberus-gaap:TreasuryStockMember2017-12-310000007039trec:AmakMemberus-gaap:RetainedEarningsMember2017-12-310000007039trec:AmakMember2017-12-310000007039us-gaap:AdditionalPaidInCapitalMembertrec:AmakMember2018-01-012018-12-310000007039trec:AmakMemberus-gaap:CommonStockMember2018-01-012018-12-310000007039trec:AmakMemberus-gaap:RetainedEarningsMember2018-01-012018-12-310000007039trec:AmakMemberus-gaap:CommonStockMember2018-12-310000007039us-gaap:AdditionalPaidInCapitalMembertrec:AmakMember2018-12-310000007039trec:AmakMemberus-gaap:TreasuryStockMember2018-12-310000007039trec:AmakMemberus-gaap:RetainedEarningsMember2018-12-310000007039trec:AmakMember2018-12-310000007039trec:AmakMemberus-gaap:TreasuryStockMember2019-01-012019-12-310000007039trec:AmakMemberus-gaap:RetainedEarningsMember2019-01-012019-12-310000007039trec:AmakMemberus-gaap:CommonStockMember2019-12-310000007039us-gaap:AdditionalPaidInCapitalMembertrec:AmakMember2019-12-310000007039trec:AmakMemberus-gaap:TreasuryStockMember2019-12-310000007039trec:AmakMemberus-gaap:RetainedEarningsMember2019-12-310000007039trec:AmakMemberus-gaap:TreasuryStockMember2020-01-012020-12-310000007039trec:AmakMemberus-gaap:RetainedEarningsMember2020-01-012020-12-310000007039trec:AmakMemberus-gaap:CommonStockMember2020-12-310000007039us-gaap:AdditionalPaidInCapitalMembertrec:AmakMember2020-12-310000007039trec:AmakMemberus-gaap:TreasuryStockMember2020-12-310000007039trec:AmakMemberus-gaap:RetainedEarningsMember2020-12-310000007039trec:AmakMember2009-12-31trec:share_bundle0000007039trec:TrecoraUSCompanyMemberus-gaap:LoansPayableMembertrec:LoanDueToTheMinistryOfFinanceAndNationalEconomyMember2009-12-310000007039trec:TrecoraUSCompanyMembertrec:AlMasaneMineMember1993-05-221993-05-22utr:sqkm0000007039trec:TrecoraUSCompanyMembertrec:AlMasaneMineMember1993-05-220000007039trec:AmakMember2011-01-012011-12-310000007039trec:AmakMember2011-12-31iso4217:SARxbrli:shares0000007039trec:AmakMember2013-01-012013-12-310000007039trec:AmakMember2013-12-310000007039trec:AmakMember2015-01-012015-12-310000007039trec:AmakMember2015-12-310000007039trec:AmakMember2016-01-012016-12-310000007039trec:AmakMember2016-12-310000007039trec:AmakMember2018-10-310000007039trec:AmakMember2019-01-012019-03-310000007039trec:AmakMember2019-10-022019-10-020000007039trec:AmakMembertrec:AmakMember2019-10-022019-10-020000007039trec:AmakMember2020-04-012020-09-280000007039trec:AmakMember2020-04-012020-04-010000007039trec:AmakMember2020-08-102020-08-100000007039trec:AmakMembertrec:SaudiShareholdersMember2020-09-300000007039trec:AmakMembertrec:ArmicoMember2020-09-300000007039trec:AmakMembertrec:OtherShareholdersMember2020-09-300000007039trec:SaudiShareholdersTrecoraAndARMICOMembertrec:AmakMember2020-09-300000007039us-gaap:PropertyPlantAndEquipmentOtherTypesMembersrt:MinimumMembertrec:AmakMember2020-01-012020-12-310000007039us-gaap:PropertyPlantAndEquipmentOtherTypesMembertrec:AmakMembersrt:MaximumMember2020-01-012020-12-310000007039trec:AmakMembercurrency:SAR1986-06-300000007039trec:AmakMember2020-01-012020-09-30trec:year0000007039srt:MinimumMemberus-gaap:MiningPropertiesAndMineralRightsMembertrec:AmakMember2020-01-012020-12-310000007039us-gaap:MiningPropertiesAndMineralRightsMembertrec:AmakMembersrt:MaximumMember2020-01-012020-12-310000007039trec:AmakMembertrec:StockpileOreMember2020-09-300000007039trec:AmakMembertrec:StockpileOreMember2019-12-310000007039trec:OreConcentratesMembertrec:AmakMember2020-09-300000007039trec:OreConcentratesMembertrec:AmakMember2019-12-310000007039trec:AmakMembertrec:PreciousMetalDoreMember2020-09-300000007039trec:AmakMembertrec:PreciousMetalDoreMember2019-12-310000007039trec:AmakMembertrec:ExplosivesMember2020-09-300000007039trec:AmakMembertrec:ExplosivesMember2019-12-310000007039trec:AmakMembertrec:ChemicalsAndOtherMember2020-09-300000007039trec:AmakMembertrec:ChemicalsAndOtherMember2019-12-310000007039trec:AmakMember2020-09-300000007039trec:AmakMemberus-gaap:BuildingMember2020-09-300000007039trec:AmakMemberus-gaap:BuildingMember2019-12-310000007039us-gaap:LeaseholdImprovementsMembertrec:AmakMember2020-09-300000007039us-gaap:LeaseholdImprovementsMembertrec:AmakMember2019-12-310000007039us-gaap:EquipmentMembertrec:AmakMember2020-09-300000007039us-gaap:EquipmentMembertrec:AmakMember2019-12-310000007039trec:AmakMemberus-gaap:VehiclesMember2020-09-300000007039trec:AmakMemberus-gaap:VehiclesMember2019-12-310000007039trec:AmakMembertrec:CivilWorksMember2020-09-300000007039trec:AmakMembertrec:CivilWorksMember2019-12-310000007039trec:AmakMembertrec:TailingsDamMember2020-09-300000007039trec:AmakMembertrec:TailingsDamMember2019-12-310000007039trec:AmakMembertrec:PlantAndMachineryMember2020-09-300000007039trec:AmakMembertrec:PlantAndMachineryMember2019-12-310000007039us-gaap:MiningPropertiesAndMineralRightsMembertrec:AmakMember2020-09-300000007039us-gaap:MiningPropertiesAndMineralRightsMembertrec:AmakMember2019-12-310000007039trec:AmakMemberus-gaap:MineDevelopmentMember2020-09-300000007039trec:AmakMemberus-gaap:MineDevelopmentMember2019-12-310000007039us-gaap:ConstructionInProgressMembertrec:AmakMember2020-09-300000007039us-gaap:ConstructionInProgressMembertrec:AmakMember2019-12-310000007039us-gaap:SecuredDebtMembertrec:AmakMembertrec:LoanAgreementWithSaudiIndustrialDevelopmentFundSIDFMember2010-12-310000007039trec:AmakMembertrec:BanqueSaudiFransiBSFCreditFacilityMember2019-12-310000007039us-gaap:LineOfCreditMembertrec:SaudiArabianInterbankOfferedRateSAIBORMembertrec:BanqueSaudiFransiBSFCreditFacilityMember2019-01-012019-12-310000007039trec:AmakMembertrec:BanqueSaudiFransiBSFCreditFacilityMember2019-12-012019-12-310000007039trec:AmakMembertrec:LoanAgreementWithSaudiIndustrialDevelopmentFundSIDFMember2019-12-012019-12-310000007039us-gaap:SecuredDebtMembertrec:AmakMembertrec:LoanAgreementWithSaudiIndustrialDevelopmentFundSIDFMember2020-09-300000007039us-gaap:SecuredDebtMembertrec:AmakMembertrec:LoanAgreementWithSaudiIndustrialDevelopmentFundSIDFMember2019-12-310000007039us-gaap:SecuredDebtMembertrec:AmakMembertrec:LoanAgreementWithSaudiIndustrialDevelopmentFundSIDFMember2019-01-012019-09-300000007039us-gaap:SecuredDebtMembertrec:AmakMembertrec:LoanAgreementWithSaudiIndustrialDevelopmentFundSIDFMember2019-01-012019-12-310000007039trec:AmakMember2012-01-012012-12-310000007039us-gaap:MiningPropertiesAndMineralRightsMember2020-12-310000007039us-gaap:MiningPropertiesAndMineralRightsMembertrec:GuyanMember2020-12-31
UNITED STATES SECURITIES AND EXCHANGE COMMISSION
Washington, D.C. 20549
___________________
FORM 10-K
(MARK ONE)
| | | | | |
☒ | ANNUAL REPORT PURSUANT TO SECTION 13 OR 15(d) OF THE SECURITIES EXCHANGE ACT OF 1934 For The Fiscal Year Ended December 31, 2020 OR |
☐ | TRANSITION REPORT PURSUANT TO SECTION 13 OR 15(d) OF THE SECURITIES EXCHANGE ACT OF 1934 For The Transition Period from ___________ to ________ |
Commission File Number 1-33926
TRECORA RESOURCES
(Exact name of registrant as specified in its charter)
| | | | | |
Delaware (State or other jurisdiction of incorporation or organization) | 75-1256622 (I.R.S. Employer Identification No.) |
1650 Hwy 6 S, Suite 190 Sugar Land, TX (Address of principal executive offices) | 77478 (Zip code) |
Registrant’s telephone number, including area code: (281) 980-5522
Securities registered pursuant to Section 12(b) of the Act:
| | | | | | | | |
Title of each class | Trading Symbol(s) | Name of each exchange on which registered |
Common Stock, par value $0.10 per share | TREC | New York Stock Exchange |
Securities registered pursuant to Section 12(g) of the Act:
None
Indicate by check mark if the registrant is a well-known seasoned issuer, as defined in Rule 405 of the Securities Act. Yes ☐ No ý
Indicate by check mark if the registrant is not required to file reports pursuant to Section 13 or Section 15(d) of the Act. Yes ☐ No ý
Indicate by check mark whether the registrant (l) has filed all reports required to be filed by Section 13 or 15(d) of the Securities Exchange Act of 1934 during the preceding 12 months (or for such shorter period that the registrant was required to file such reports), and (2) has been subject to such filing requirements for the past 90 days. Yes ý No ☐
Indicate by check mark whether the registrant has submitted electronically every Interactive Data File required to be submitted pursuant to Rule 405 of Regulation S-T (§232.405 of this chapter) during the preceding 12 months (or for such shorter period that the registrant was required to submit such files). Yes ý No ☐
Indicate by check mark whether the registrant is a large accelerated filer, an accelerated filer, a non-accelerated filer, a smaller reporting company, or an emerging growth company. See the definitions of “large accelerated filer", “accelerated filer", “smaller reporting company", and “emerging growth company" in Rule 12b-2 of the Exchange Act.
| | | | | |
Large accelerated filer ☐ | Accelerated filer ý |
Non-accelerated filer ☐ | Smaller reporting company ☒ |
Emerging growth company ☐ | |
If an emerging growth company, indicate by check mark if the registrant has elected not to use the extended transition period for complying with any new or revised financial accounting standards provided pursuant to Section 13(a) of the Exchange Act ☐
Indicate by check mark whether the registrant has filed a report on and attestation to its management’s assessment of the effectiveness of its internal control over financial reporting under Section 404(b) of the Sarbanes-Oxley Act (15 U.S.C. 7262(b)) by the registered public accounting firm that prepared or issued its audit report. Yes ☒ No ☐
Indicate by check mark whether the registrant is a shell company (as defined in Rule 12b-2 of the Act.) Yes ☐ No ý
The aggregate market value on June 30, 2020, of the registrant’s voting securities held by non-affiliates was approximately $119 million.
Number of shares of registrant’s Common Stock, par value $0.10 per share, outstanding as of February 26, 2021: 24,834,693.
DOCUMENTS INCORPORATED BY REFERENCE
Certain information required to be furnished pursuant to Part III of this Form 10–K will be set forth in, and will be incorporated by reference from, the registrant’s definitive proxy statement for the 2021 Annual Meeting of Stockholders anticipated to be held on May 14, 2021 to be filed by the registrant with the Securities and Exchange Commission pursuant to Regulation 14A within 120 days after the registrant’s fiscal year ended December 31, 2020.
TABLE OF CONTENTS
Item Number and Description
PART I
ITEM 1. Business.
General
Trecora Resources (the “Company" or “TREC”) was incorporated in the State of Delaware in 1967. The Company's principal business activities are the manufacturing of various specialty petrochemicals products and specialty waxes and the provision of custom processing services. Unless the context requires otherwise, references to “we,” “us,” “our,” “TREC,” and the “Company" are intended to mean Trecora Resources and its subsidiaries.
This document includes the following abbreviations:
a.TOCCO – Texas Oil & Chemical Co. II, Inc. – Wholly owned subsidiary of TREC and parent of SHR and TC
b.SHR – South Hampton Resources, Inc. – Specialty Petrochemicals segment and parent of GSPL
c.GSPL – Gulf State Pipe Line Co, Inc. – Pipeline support for the Specialty Petrochemicals segment
d.TC – Trecora Chemical, Inc. – Specialty Waxes segment
e.PEVM – Pioche Ely Valley Mines, Inc. – Inactive mine - 55% ownership
f.AMAK – Al Masane Al Kobra Mining Company – Held-for-sale mining equity investment and discontinued operations (sale of ownership interest completed in September 2020)
Business Segments
We operate in two business segments; the manufacturing of various specialty petrochemicals products and the manufacturing of specialty waxes.
Our Specialty Petrochemicals segment is conducted through SHR, a Texas corporation. SHR owns and operates a specialty petrochemicals facility in Silsbee, Texas which produces high purity hydrocarbons and other petroleum based products including isopentane, normal pentane, isohexane and hexane. These products are used in the production of polyethylene, packaging, polypropylene, expandable polystyrene, poly-iso/urethane foams, crude oil from the Canadian tar sands, and in the catalyst support industry. Our Specialty Petrochemicals products are typically transported to customers by rail car, tank truck, iso-container, and by ship. SHR owns all of the capital stock of GSPL, a Texas corporation, which owns and operates pipelines that connect the SHR facility to a natural gas line, to SHR’s truck and rail loading terminal and to a major petroleum products pipeline owned by an unaffiliated third party. SHR also provides custom processing services at its Silsbee facility.
Our Specialty Waxes segment is conducted through TC, a Texas corporation, located in Pasadena, Texas which produces specialty polyethylene and poly alpha olefin waxes and provides custom processing services. The specialty polyethylene waxes are used in markets from paints and inks to adhesives, coatings, and PVC lubricants. The highly specialized synthetic poly alpha olefin waxes are used in applications such as toner in printers and as additives for candles. These waxes are sold in solid form as pastilles or, for large adhesive companies, in bulk liquid form.
See Note 17 to the Consolidated Financial Statements for more information.
In addition, on September 28, 2020, we completed the final closing of the sale of our ownership interest in AMAK, a Saudi Arabian closed joint stock company, which owns, operates and is developing mining assets in Saudi Arabia. Our investment was classified as held-for-sale and the equity in earnings (losses) were recorded in discontinued operations. See Note 6 to the Consolidated Financial Statements for more information.
Specialty Petrochemicals Operations
SHR’s specialty petrochemicals facility is located in Silsbee, Texas approximately 30 miles north of Beaumont and 90 miles east of Houston. The base SHR facility consists of five operating units which, while interconnected, make distinct products through differing processes: (i) a Penhex Unit; (ii) a Reformer Unit; (iii) a Cyclo-pentane Unit; (iv) an Advanced Reformer unit; and (v) an Isomerization Unit. In addition to the base plant, SHR operates three proprietary chemical production facilities for toll processing customers. The Penhex Unit currently has the permitted capacity to process approximately 11,000 barrels per day of fresh feed. The Reformer Unit, the Advanced Reformer unit, and the Cyclo-Pentane Unit further process streams produced by the Penhex Unit.
The facility generally consists of equipment commonly found in most petrochemical facilities such as fractionation towers and hydrogen treaters, except the facility is adapted to produce specialized products that are high purity and very consistent with precise specifications that are utilized in the petrochemical industry as solvents, additives, blowing agents and cooling agents.
Our present total capacity at our Silsbee facility is 13,000 barrels per day of fresh feed; however, our air permits limit us to a maximum processing rate of 11,000 barrels per day. During 2018, we constructed a 4,000 barrels per day Advanced Reformer unit to increase our capability to upgrade by-products produced from the Penhex Unit and to provide security of hydrogen supply to the plant. We believe we have sufficient pentane capacity to maintain our share of market growth for the foreseeable future.
The Advanced Reformer, Reformer and Isomerization units are operated as needed to support the Penhex and Cyclo-pentane Units. Consequently, utilization rates of these units are driven by production from the Penhex Unit.
Operating utilization rates are affected by product demand, raw material composition, mechanical integrity, and unforeseen natural occurrences, such as weather events. The nature of the petrochemical process demands periodic shut-downs for decoking and other mechanical repairs.
In support of the specialty petrochemicals operation, we own approximately 100 storage tanks with total capacity approaching 294,000 barrels, and 127 acres of land at the plant site, 107 acres of which are developed. We also own a truck and railroad loading terminal consisting of storage tanks, nine rail spurs, and truck and tank car loading facilities on approximately 63 acres of which 33 acres are developed.
We obtain substantially all our feedstock from a sole supplier. The agreement is primarily a logistics arrangement whereby the supplier buys or contracts for feedstock material and utilizes their tank and pipeline connections to transport into our pipeline. We renewed our contract with this supplier in May 2020 for a period extending through the end of July 2026 with subsequent one year renewals unless canceled by either party with 180 days' notice.
GSPL owns and operates two 8-inch diameter pipelines and five 4-inch diameter pipelines, aggregating approximately 70 miles in length connecting SHR’s facility to (1) a natural gas line, (2) SHR’s truck and rail loading terminal and (3) a major petroleum products pipeline system owned by an unaffiliated third party. All pipelines are operated within Texas Railroad Commission and DOT regulations for maintenance and integrity.
We sell our products predominantly to large domestic and international companies. Products are marketed through continued long term relationships. Our commercial team has historically prided itself on regular visits at customer facilities as well as attendance at various petrochemical conferences throughout the world. Due to the COVID-19 pandemic, we pivoted this year to remote contact with customers. We also provide information about our products and services through our website. We utilize both formula and non-formula based pricing depending upon a customer’s requirements and competitive situations. Under formula pricing, the price charged to the customer is primarily based on a formula which includes as a component the average cost of feedstock over the prior month. With this pricing mechanism, product prices move in conjunction with feedstock prices. However, the formulas use an average feedstock price from the prior month. Current formula product sales prices trail current market feedstock prices by approximately 30 days. See additional discussion of concentration of revenue and corresponding receivables as disclosed in Note 3 to the Consolidated Financial Statements.
Specialty Waxes Operations
TC is a leading manufacturer of specialty waxes and also provides custom processing services from its 27.5 acre plant located in Pasadena, Texas. TC provides custom manufacturing, hydrogenation, distillation, blending, forming and packaging of finished and intermediate products and wax products for coatings, hot melt adhesives and lubricants. Situated near the Houston Ship Channel, the facility allows for easy access to international shipping and direct loading to rail or truck. The location is within reach of major chemical pipelines and on-site access to a steam pipeline and dedicated hydrogen line create a platform for expansion of both wax production capacity and custom processing capabilities. We manufacture a variety of hard, high melting point, low to medium viscosity polyethylene wax products along with a wide range of other waxes and lubricants. These products are used in a variety of applications including: performance additives for hot melt adhesives; penetration and melting point modifiers for paraffin and microcrystalline waxes; lubrication and processing aides for plastics, PVC, rubber, and dry stir-in additives for inks. In oxidized forms, applications also include use in textile emulsions.
TC also provides turnkey custom manufacturing services including quality assurance, transportation and process optimization. The plant has high vacuum distillation capability for the separation of temperature sensitive materials. We have a fully equipped laboratory and pilot plant facility and a highly trained, technically proficient team of engineers and chemists suited to handle the rapid deployment of new custom processes and development of new wax products. TC’s custom manufacturing services provide a range of specialized capabilities to chemical and industrial customers including synthesis, hydrogenation, distillation, forming and propoxylation in addition to a number of other chemical processes.
Mineral Interests
We also have a 55% ownership interest in an inactive mining corporation, PEVM. PEVM’s properties include 48 patented and 5 unpatented claims totaling approximately 1,500 acres. All of the claims are located in Lincoln County, NV.
In November 2019, PEVM entered into a sales contract which, upon completion of due diligence, may lead to liquidation of substantially all of its remaining assets. Upon closing of the sale, PEVM will be dissolved. Any proceeds from the sale will primarily be used to repay outstanding indebtedness of PEVM owed to the Company.
Environmental, Health and Safety Matters
Our operations are subject to a wide range of environmental laws and regulations at the national, state, and local levels. Our facilities and operations are subject to numerous federal, state and local environmental laws and to other laws regarding health and safety matters (the “Environmental and Health Laws”), many of which provide for certain performance obligations, substantial fines and criminal sanctions for violations. Certain Environmental and Health Laws impose strict liability as well as joint and several liability for costs required to remediate and restore sites where hazardous substances, hydrocarbons or solid wastes have been stored or released. We may be required to remediate contaminated properties currently or formerly owned or operated by us or facilities of third parties that received waste generated by our operations regardless of whether such contamination resulted from the conduct of others or from consequences of our own actions that were in compliance with all applicable laws at the time those actions were taken.
There can be no assurance that we will not incur material costs or liabilities in complying with such laws or in paying fines or penalties for violation of such laws. Our insurance may not cover all environmental risks and costs or may not provide sufficient coverage if an environmental claim is made against us. The Environmental and Health Laws and enforcement policies thereunder have in the past resulted, and could in the future result, in significant compliance expenses, cleanup costs (for our sites or third-party sites where our wastes were disposed of), penalties or other liabilities relating to the handling, manufacture, use, emission, discharge or disposal of hazardous or toxic materials at or from our facilities or the use or disposal of certain of its chemical products. Historically, our subsidiaries have incurred significant expenditures in order to comply with the Environmental and Health Laws and are reasonably expected to do so in the future. We will also be obligated to manage certain discharge water outlets and monitor groundwater contaminants at our chemical facilities should we discontinue the operations of a facility. Matters pertaining to the environment are discussed in Part I, Item 1A. Risk Factors, Part II, Item 7. Management’s Discussion and Analysis of Financial Condition and Results of Operations and Notes 2 and 14 to the Consolidated Financial Statements.
In 1993, during remediation of a small spill area, the Texas Commission on Environmental Quality (“TCEQ”) required SHR to drill a well to check for groundwater contamination under the spill area. Two pools of hydrocarbons were discovered to be floating on the groundwater at a depth of approximately 25 feet. One pool is under the site of a former gas processing plant owned and operated by Sinclair, Arco and others before its purchase by SHR in 1981. Analysis of the material indicates it entered the ground prior to SHR’s acquisition of the property. The other pool is under the original SHR facility and analysis indicates the material was deposited decades ago. Tests conducted have determined that the hydrocarbons are contained on the property and not migrating in any direction. The recovery is proceeding as planned and is expected to continue for many years until the pools are reduced to acceptable levels. Expenses of recovery and periodic migration testing are being recorded as normal operating expenses. Expenses for future recovery are expected to stabilize and be less per annum than the initial set up cost, although there is no assurance of this. The light hydrocarbon recovered from the former gas plant site is compatible with
our normal Penhex feedstock and is accumulated and transferred into the Penhex feedstock tank. The material recovered from under the original SHR site is accumulated and sold as a by-product. We have drilled additional wells periodically to further delineate the boundaries of the pools and to ensure that migration has not taken place. These tests confirmed that no migration of the hydrocarbon pools has occurred. The TCEQ has deemed the current action plan acceptable and reviews the plan on a semi-annual basis.
Human Capital Management
Trecora Resources and its subsidiaries hire and retain employees by offering competitive pay and benefits while motivating our workforce through a number of recognition and bonus programs. We are proud to provide our employees the opportunity to grow and advance as we invest in their training, education and career development.
As of December 31, 2020, we had 263 employees, 10 of whom were corporate management and staff and 253 worked at our plant facilities. We employ regular employees defined as active executive, management, professional, technical and wage employees who work full time or part time for the Company and are covered by our benefit plans and programs. We have not experienced any significant work stoppages, either as a result of the COVID-19 pandemic or otherwise.
We are committed to providing market-competitive pay and benefits. All regular employees are eligible for performance-based cash incentive programs. The incentive plan reinforces and rewards individuals for achievement of specific business goals, including safety, quality and productivity.
We offer comprehensive benefit programs to our employees that provide flexibility of choice through our total rewards framework of pay and recognition, health and wellness, work/life balance, learning and development, and culture and community. We recognize and support the growth and development of our employees and encourage employees to participate in external learning programs.
COVID-19 Response
We took early action regarding employee well-being in response to the COVID-19 pandemic, implementing comprehensive protocols to protect the health and safety of our employees and contractors. Many of our employees were transitioned to a remote work environment for the duration of the pandemic. We had no reductions in scheduled hours or reductions in force for any of our employees. We also enhanced our benefits programs to offer expanded supplemental paid leave during quarantine periods and waived employee cost-sharing for COVID-19 testing.
Competition
The specialty petrochemicals and specialty waxes industries are highly competitive. There is competition within the industries and also with other industries in supplying the needs of both industrial and individual consumers. We compete with other firms in the sale or purchase of needed goods and services and employ all methods of competition which are lawful and appropriate for such purposes. See further discussion in Part I, Item 1A. Risk Factors.
Available Information
We will provide paper copies of this Annual Report on Form 10-K, our quarterly reports on Form 10-Q, our current reports on Form 8-K and amendments to those reports, all as filed or furnished pursuant to Section 13(a) or 15(d) of the Securities Exchange Act of 1934, as amended (the “Exchange Act”), free of charge upon written or oral request to Trecora Resources, 1650 Hwy 6 S, Suite 190, Sugar Land, TX 77478, (281) 980-5522. These reports are also available free of charge on our website, www.trecora.com, as soon as reasonably practicable after they are filed electronically with the U.S. Securities and Exchange Commission (“SEC”) and can also be accessed by visiting the SEC website at www.sec.gov. SHR also has a website at www.southhamptonr.com, and TC has a website at www.trecchem.com. Any of the aforementioned websites and the information contained on or connected to them are not incorporated by reference herein to the SEC filings.
ITEM 1A. Risk Factors.
We are subject to a variety of risks inherent in the global specialty petrochemicals and specialty waxes businesses. Many of these risk factors are not within our control and could adversely affect our business, results of operations or our financial condition.
Risks Related to our Industry and Operations
We rely on a limited number of customers, including one customer that represented more than 10% of our consolidated revenue in 2020. A significant change in customer relationships or in customer demand for our products could materially adversely affect our results of operations, financial condition and cash flows.
We rely on a limited number of customers. Our largest customer, ExxonMobil and its affiliates, represented approximately 15.4% of our consolidated revenues in 2020. A significant reduction in sales to any of our key customers could materially adversely affect our results of operations, financial condition and cash flows, and could result from our key customers further
diversifying their product sourcing, experiencing financial difficulty or undergoing consolidation.
Our industry is highly competitive, and we may lose market share to other producers of specialty petrochemicals, specialty waxes or other products that can be substituted for our products, which may adversely affect our results of operations, financial condition and cash flows.
Our industry is highly competitive, and we face significant competition from both large international producers and from smaller regional competitors. Our competitors may improve their competitive position in our core markets by successfully introducing new products, improving their manufacturing processes or expanding their capacity or manufacturing facilities. Further, some of our competitors benefit from advantageous cost positions that could make it increasingly difficult for us to compete in certain markets. If we are unable to keep pace with our competitors’ product and manufacturing process innovations, cost position or alternative value proposition, it could have a material adverse effect on our results of operations, financial condition and cash flows.
In addition, we face increased competition from companies that may have greater financial resources and different cost structures, alternative values or strategic goals than us. We have a portfolio of businesses across which we must allocate our available resources, while competing companies may specialize in only certain of our product lines. As a result, we may invest less in certain areas of our business than our competitors, and such competitors may have greater financial, technical and marketing resources available to them. Industry consolidation may also affect competition by creating larger, more homogeneous and stronger competitors in the markets in which we compete, and competitors also may affect our business by entering into exclusive arrangements with existing or potential customers or suppliers. We may have to lower the prices of many of our products and services to stay competitive, while at the same time, trying to maintain or improve revenue and gross margin.
Loss of key employees, our inability to attract and retain new qualified employees or our inability to keep our employees focused on our strategies and goals could have an adverse impact on our operations.
In order to be successful, we must attract, retain and motivate executives and other key employees including those in managerial, technical, safety, operations, sales and marketing positions. We must also keep employees focused on our strategies and goals. The failure to hire, or loss of, key employees in a competitive industry could have a significant adverse impact on our operations. In addition, an important component of our competitive performance is our ability to operate safely and efficiently, including our ability to manage expenses and minimize the production of low margin products on an on-going basis. This requires continuous management focus, including technological improvements, safe operations, cost control and productivity enhancements. The extent to which we manage these factors will impact our performance relative to competition.
If the availability of our raw materials is limited, we may be unable to produce some of our products in quantities sufficient to meet customer demand or on favorable economic terms, which could have an adverse effect on our results of operations, financial condition and cash flows.
We use natural gasoline as a raw material in the production our products in the Specialty Petrochemicals segment. We use polyethylene waxes in our Specialty Waxes segment. Suppliers may not be able to meet our raw material requirements and we may not be able to obtain substitute supplies from alternative suppliers in sufficient quantities, on economic terms, or in a timely manner. A lack of timely availability of our raw materials in the quantities we require to produce our products (including as a result of supply chain issues due to the COVID-19 pandemic or other global economic issues) could result in our inability to meet customer demand and could have a material adverse effect on our results of operations, financial condition and cash flows.
Increases in the costs of our raw materials could have an adverse effect on our financial condition and results of operations if those costs cannot be passed onto our customers.
Our results of operations are directly affected by the cost of raw materials. Since the cost of these primary raw materials comprise a significant amount of our total cost of goods sold, the selling prices for our products and therefore our total revenue is impacted by movements in these raw material costs, as well as the cost of other inputs. In the past we have experienced erratic and significant changes in the costs of these raw materials, the cost of which has generally correlated with changes in energy prices, supply and demand factors, and prices for natural gas and crude oil. Moreover, the price of raw materials may also be impacted by other external factors, including uncertainties associated with war, terrorist attacks, weather and natural disasters, health epidemics or pandemics (such as the COVID-19 pandemic), civil unrest, the effects of climate change or political instability, plant or production disruptions, strikes or other labor unrest, breakdown or degradation of transportation infrastructure used in the delivery of raw materials or changes in laws or regulations in any of the countries in which we have significant suppliers. In addition, product mix can have an impact on our overall unit selling prices, since we provide an extensive product offering and therefore experience a wide range of unit selling prices. Because of the significant portion of our cost of goods sold represented by these raw materials, our gross profit margins could be adversely affected by changes in the cost of these raw materials if we are unable to pass the increases on to our customers.
In addition, we utilize both formula and non-formula based pricing, depending on customer requirements and competitive situations. Under formula pricing the price charged to the customer is primarily based on a formula which includes, as a component, the average cost of feedstock over the prior month. With this pricing mechanism, product prices generally move in conjunction with feedstock prices. However, because the formulas use an average feedstock price from the prior month, the movement of prices will trail the movement of costs, and formula prices may or may not reflect our actual feedstock cost for the month during which the product is actually sold. In addition, while formula pricing can reduce product margins during periods of increasing feedstock costs, during periods of decreasing feedstock costs, formula pricing will follow feedstock costs down but will retain higher margins during the period by trailing the movement of costs by approximately 30 days. These timing differences have had and may, in the future, have a negative effect on our cash flow. Any raw materials cost increase that we are not able to pass on to our customers could have a material adverse effect on our business, results of operations, financial condition and liquidity.
Due to volatile raw material prices, there can be no assurance that we can continue to recover raw material costs or retain customers in the future. For example, our logistics costs have increased substantially within the past three years, narrowing our profit margins. This may force us to increase our pricing, which could cause customers to consider competitors’ products, some of which may be available at a lower cost. Significant loss of customers could result in a material adverse effect on our results of operations, financial condition and cash flows.
If we are unable to access third-party transportation for our raw materials and finished products, we may not be able to fulfill our obligations to our customers in a timely manner, which could have a material adverse effect on our results of operations, financial condition and cash flows.
We rely upon transportation provided by third parties (including common carriers, rail companies and trans-ocean cargo companies) to receive raw materials used in the production of our products and to deliver finished products to our customers. While we attempt to offset the risks associated with third-party transportation issues, including by owning and operating a truck fleet to meet certain customer demand as well as managing our supplies of raw materials, such mitigation efforts may not be successful. If we are unable to access third-party transportation at economically attractive rates, or at all, or if there is any other significant disruption in the availability of third-party transportation, we may not be able to obtain sufficient quantities of raw materials (on favorable terms, or at all) to match the pace of production and/or we may not be able to fulfill our obligations to our customers in a timely manner, which could have a material adverse effect on our results of operations, financial condition and cash flows.
Failure to successfully consummate extraordinary transactions, including the integration of other businesses, assets, products or technologies, or realize the financial and strategic goals that were contemplated at the time of any such transaction may adversely affect our future business, results of operations and financial condition.
As part of our business strategy, we from time to time explore possible investments, acquisitions, strategic alliances, joint ventures, divestitures and outsourcing transactions (collectively, “extraordinary transactions”) in order to further our business objectives. To pursue this strategy successfully, we must identify suitable candidates for, and successfully complete, extraordinary transactions, some of which may be large and complex, and manage post-closing issues such as the integration of acquired businesses or employees. The expense and effort incurred in exploring and consummating extraordinary transactions, the time it takes to integrate an acquisition or our failure to integrate businesses successfully, could result in additional and/or unexpected expenses and losses. We also may not be successful in negotiating the terms of any potential extraordinary transactions, conducting thorough due diligence, financing an extraordinary transaction or effectively integrating the acquired business, product or technology into our existing business and operations. Our due diligence may fail to identify all of the problems, liabilities or other shortcomings or challenges of an acquired business, product or technology. Moreover, we may incur significant expenses whether or not a contemplated extraordinary transaction is ultimately consummated.
Additionally, in connection with any extraordinary transaction we consummate, we many not fully realize all of the anticipated synergies and other benefits we expect to achieve (on our expected timeframe, or at all), and we may incur unanticipated expenses, write-downs, impairment charges or unforeseen liabilities that could negatively affect our business, financial condition and results of operations, disrupt relationships with current and new employees, customers and vendors, incur significant debt or have to delay or not proceed with announced transactions. Further, managing extraordinary transactions requires varying levels of management and employee resources, which may divert our attention from other business operations. We may also face additional challenges and costs after the consummation of the transaction, including those related to integrating or restructuring our operations, information management and other technology systems, while carrying on our ongoing business.
Maintenance, expansion and refurbishment of our facilities and the development and implementation of new manufacturing processes involve significant risks which may adversely affect our business, results of operations, financial condition and cash flows.
Our facilities require periodic maintenance, upgrading, expansion, refurbishment or improvement. Any unexpected operational or mechanical failure, including failure associated with breakdowns and forced outages, could reduce our facilities’ production capacity below expected levels which would reduce our revenues and profitability. Unanticipated expenditures associated with maintaining, upgrading, expanding, refurbishing or improving our facilities may also reduce profitability.
If we make any major modifications to our facilities, such modifications likely would result in substantial additional capital expenditures and may prolong the time necessary to bring the facility online. We may also choose to refurbish or upgrade our facilities based on our assessment that such activity will provide adequate financial returns. However, such activities require time for development before commencement of commercial operations, and key assumptions underpinning a decision to make such an investment may prove incorrect, including assumptions regarding construction costs, demand growth and timing which could have a material adverse effect on our business, results of operations, financial condition and cash flows.
Finally, we may not be successful or efficient in developing or implementing new production processes. Innovation in production processes involves significant expense and carries inherent risks, including difficulties in designing and developing new process technologies, development and production timing delays, lower than anticipated manufacturing yields, and product defects. Disruptions in the production process can also result from errors, defects in materials, delays in obtaining or revising operating permits and licenses, returns of product from customers, interruption in our supply of materials or resources and disruptions at our facilities due to accidents, maintenance issues, or unsafe working conditions, all of which could affect the timing of production ramps and yields. Production issues can lead to increased costs and may affect our ability to meet product demand, which could adversely impact our business, results of operations, financial condition and cash flows.
There are certain hazards and risks inherent in our operations that could adversely affect those operations and results of operations and financial condition.
As a manufacturer and distributor of diversified chemical products, our business is subject to operating risks inherent in chemical manufacturing, storage, handling and transportation. These risks include, but are not limited to, fires, explosions, severe weather and natural disasters, mechanical failure, unscheduled downtime, loss of raw materials or our products, transportation interruptions, remediation, chemical spills, terrorist acts or war, discharges or releases of toxic or hazardous substances or gases. These hazards can cause personal injury and loss of life, severe damage to, or destruction of, property and equipment and environmental contamination. In addition, our suppliers are also subject to similar risks that may adversely impact our production capabilities. A significant limitation on our ability to manufacture products due to disruption of manufacturing operations or related infrastructure could have a material adverse effect on our results of operations and financial condition.
While we adapt our manufacturing and distribution processes and controls to minimize the inherent risk of our operations, to promote workplace safety and to minimize the potential for human error, we cannot completely eliminate the risk of accidental contamination or injury from hazardous or regulated materials, including injury of our employees, individuals who handle our products or goods treated with our products, or others who claim to have been exposed to our products, nor can we completely eliminate the unanticipated interruption or suspension of operations at our facilities due to such events. We may be held liable for significant damages or fines in the event of contamination or injury, and such assessed damages or fines could have a material adverse effect on our results of operations and financial conditions. Our property, business interruption and casualty insurance may not fully insure us against all potential hazards incidental to our business.
Conditions in the global economy may adversely affect our results of operations, financial condition and cash flows.
The demand for our products have historically correlated closely with general economic growth rates. The occurrence of recessions or other periods of low or negative growth will typically have a direct adverse impact on our results of operations, financial condition and cash flows. Other factors that affect general economic conditions in the world or in a major region, such as changes in population growth rates or periods of civil unrest, weather and national disasters or health epidemics and pandemics also impact the demand for our products. Economic conditions that impair the functioning of financial markets and financial institutions also pose risks to us, including risks to the safety of our financial assets and to the ability of our partners and customers to fulfill their commitments to us.
In addition, the revenue and profitability of our operations have historically been subject to fluctuation, which makes future financial results less predictable. Our revenue, gross margin and profit vary among our products, customer groups and geographic markets. Overall gross margins and profitability in any given period are dependent partially on the product, customer and geographic mix reflected in that period’s net revenue. In addition, newer geographic markets may be relatively less profitable due to investments associated with entering those markets and local pricing pressures. Market trends, competitive pressures, increased raw material or shipping costs, regulatory impacts and other factors may result in reductions in revenue or
pressure on gross margins of certain segments in a given period which may necessitate adjustments to our operations.
The global outbreak of COVID-19 has had, and may continue to have, an adverse impact on the business, results of operations, financial position, and liquidity of the Company and/or its customers, suppliers, and other counterparties.
The COVID-19 pandemic has caused, and may continue to cause, a global slowdown of economic activity, particularly, reduced demand in durable goods markets such as automotive and construction, disruptions in global supply chains, significant economic uncertainty and volatility and disruption of financial markets. The COVID-19 pandemic is having an impact on the Company’s operations and financial performance, as well as on the operations and financial performance of many of the Company’s customers and suppliers. Across all of our businesses, we are facing increased operational challenges from the continued need to protect employee health and safety by requiring restrictions on the movement of people, which can cause workplace disruptions, reduced productivity, operational disruptions or shutdowns, and the incurrence of additional costs. Due to the economic slowdown caused by the COVID-19 pandemic, we are also experiencing, and may continue experiencing, lower demand and volume for products and services from our customers, as well as potential restrictions or delays on deliveries of key raw materials from our suppliers. See Part II, Item 7. Management’s Discussion and Analysis of Financial Condition and Results of Operations, for additional information on how we have been impacted and the steps we have taken in response.
Because the severity, magnitude and duration of the COVID-19 pandemic and its economic consequences are uncertain, rapidly changing and difficult to predict, the pandemic’s impact on the Company’s operations and financial performance, as well as its impact on our ability to successfully execute our business strategies and initiatives, remains uncertain and difficult to predict. Additionally, the ultimate impact of the COVID-19 pandemic on our operations and financial performance depends on many factors that are not within our control, including, but not limited, to: governmental, business and individuals’ actions that have been and continue to be taken in response to the pandemic (including restrictions on travel and transport and human capital constraints); the impact of the pandemic and actions taken in response on global and regional economies, travel, and economic activity; the availability of federal, state, local or non-U.S. funding programs; general economic uncertainty in key global markets and financial market volatility; the weakening of demand in certain end markets; prolonged disruption in global logistics channels; global economic conditions and levels of economic growth; and the pace of recovery as the COVID-19 pandemic subsides. We expect that the longer the period of economic and global supply chain and disruption continues, the more material the impact could be on our business operations, financial performance and results of operations, and this could include potential charges, impairments and other adverse financial impacts in future periods.
As the COVID-19 pandemic continues to adversely affect our operating and financial results, it may also have the effect of heightening many of the other risks described in the risk factors herein, the COVID-19 pandemic may also affect our operating and financial results in a manner that is not presently known to us.
Domestic or international natural disasters or other severe weather events, health epidemics or pandemics or terrorist attacks may disrupt our operations or those of our customers or suppliers, decrease demand for our products or otherwise have an adverse impact on our business.
Chemical related assets, and U.S. corporations such as ours, may be at a greater risk of future terrorist attacks (including both physical attacks and cyber–attacks) than other possible targets in the U.S. Moreover, extraordinary events such as natural disasters, other severe weather events or global or local health epidemics (such as the COVID-19 pandemic) could result in significant damage to our facilities, the pipeline systems and other infrastructure we rely on and/or disruption of our operations and may negatively affect local economies, including those of our customers or suppliers. The occurrence of such events cannot be predicted, although their occurrence can be expected to continue to adversely impact the economy in general and our specific markets.
The resulting damage from a natural disaster, other severe weather events or terrorist attack could include loss of life, property damage or site closure. Several of our facilities are located in regions where natural disasters and other severe weather events have previously disrupted, and may in the future disrupt, our ability to manufacture and deliver products from certain facilities. Any damage resulting in stoppage or reduction of our facilities’ production capacity could reduce our revenues and any unanticipated capital expenditures to repair such damage (to the extent not covered by our insurance policies) may reduce profitability. Any, or a combination, of these factors could also adversely impact our results of operations, financial condition and cash flows.
We are exposed to local business risks in different countries, which could have a material adverse effect on our financial condition and results of operations.
Although we do not have production operations and assets outside of the U.S., we do have a global portfolio of customers and thus we are subject to a variety of international market risks including, but not limited to: ongoing instability or changes in a country’s or region’s economic or political conditions, including inflation, recession, interest rate fluctuations, civil unrest and actual or anticipated military or political conflicts; longer accounts receivable cycles and financial instability or credit risk among customers and distributors; trade regulations and procedures and actions affecting production, pricing and marketing of
products, including domestic and foreign customs and tariffs or other trade barriers; regulations favoring local contractors or requiring foreign contractors to employ citizens of, or purchase supplies from, a local jurisdiction; local labor conditions and regulations and the geographical dispersion of the workforce; changes in the regulatory or legal environment; differing technology standards or customer requirements; import, export or other business licensing requirements or requirements relating to making foreign direct investments, which could affect our ability to obtain favorable terms for labor and raw materials or lead to penalties or restrictions; data privacy regulations; risk of non-compliance with the sanction laws or U.S. Foreign Corrupt Practices Act or similar anti-bribery legislation in other countries by agents or other third-party representatives; risk of nationalization of private enterprises by foreign governments; foreign currency exchange restrictions and fluctuations; the outbreak of global or regional health epidemics or pandemics (such as the COVID-19 pandemic); difficulties associated with repatriating cash generated or held abroad in a tax-efficient manner and changes in tax laws; and fluctuations in freight costs and disruptions in the transportation and shipping infrastructure at important geographic points of exit and entry for our products and shipments.
Such economic and political uncertainties may materially and adversely affect our business, financial condition or results of operations in ways that cannot be predicted at this time. Although it is impossible to predict the occurrences or consequences of any such events, they could result in a decrease in demand for our products, make it difficult or impossible to deliver products to our customers or to receive raw materials from our suppliers and create delays and inefficiencies in our supply chain. We are also predominantly uninsured for losses and interruptions caused by terrorist acts, conflicts and wars.
Certain activist stockholders actions could cause us to incur expense and hinder execution of our strategy.
While we seek to actively engage with our stockholders and consider their views on business and strategy, we could be subject to actions or proposals from our stockholders that do not align with our business strategies or the interests of our other stockholders. Responding to these stockholders could be costly and time-consuming, disrupt our business and operations and divert the attention of our management. Furthermore, uncertainties associated with such activities could negatively impact our ability to execute our strategic plan, retain customers and skilled employees and affect long-term growth. In addition, such activities may cause our stock price to fluctuate based on temporary or speculative market perceptions that do not necessarily reflect our business operations.
Delaware law and certain provisions of our organizational documents may make a takeover of our company more difficult.
Provisions of our charter and bylaws may have the effect of delaying, deferring or preventing a change in control of our company. A change of control could be proposed in the form of a tender offer or takeover proposal that might result in a premium over the market price for our common stock. In addition, these provisions could make it more difficult to bring about a change in the composition of our board of directors, which could result in the entrenchment of current management. For example, our charter and bylaws: require that the number of directors be determined, and provide that any vacancy or new board seat may be filled only by the board; do not permit stockholders to call a special meeting; and establish advance notice requirements for nominations for elections to our board of directors or for proposing matters that can be acted upon by stockholders at stockholder meetings.
Our employment agreements and equity arrangements with our executive officers also contain change in control provisions. Under the terms of these arrangements, the executive officers may be entitled to receive significant cash payments, immediate vesting of equity awards and continued medical benefits in the event their employment is terminated under certain circumstances in connection with or in certain circumstances following, a “corporate change”. We disclose in proxy statements filed with the SEC potential payments to our named executive officers in connection with such “corporate change.” Certain change of control transactions may also constitute an event of default under our agreements with our creditors and other third parties.
These arrangements and provisions of our organizational documents and Delaware law may have the effect of delaying, deferring or preventing changes of control or changes in management of our company, even if such transactions or changes would have significant benefits for our stockholders. As a result, these provisions could limit the price some investors might be willing to pay in the future for shares of our common stock.
Risks Related to Legal and Regulatory Matters
We are subject to numerous regulations that could require us to modify our current business practices and incur increased costs.
We are subject to numerous regulations, including customs and international trade laws, export control, data privacy, antitrust laws and zoning and occupancy laws that regulate manufacturers generally and/or govern the importation, promotion and sale of our products, the operation of our facilities and our relationship with our customers, suppliers and competitors. In addition, we face risk associated with trade protection laws, policies and measures and other regulatory requirements affecting trade and investment, including loss or modification of exemptions for taxes and tariffs, imposition of new tariffs and duties and import and export licensing requirements. If these laws or regulations were to change (including as a result of policies that may be adopted by the new Biden administration) or were violated by our management, employees, suppliers, buying agents or trading companies, the costs of certain goods could increase, or we could experience delays in shipments of our goods, be subject to fines or penalties, or suffer reputational harm, which could reduce demand for our products and hurt our business and negatively impact our results of operations. In addition, changes in federal and state minimum wage laws and other laws relating to employee benefits could cause us to incur additional wage and benefits costs, which could negatively impact our profitability.
Legal requirements are frequently changed and subject to interpretation, and we are unable to predict the ultimate cost of compliance with these requirements or their effects on our operations. We may be required to make significant expenditures or modify our business practices to comply with existing or future laws and regulations, which may increase our costs and materially limit our ability to operate our business.
Adverse results of legal proceedings could materially adversely affect us.
We are subject to and may in the future be subject to a variety of legal proceedings and claims that arise out of the ordinary conduct of our business, including legal proceedings brought in non-U.S. jurisdictions. Results of legal proceedings cannot be predicted with certainty. Irrespective of its merits, litigation may be both lengthy and disruptive to our operations and may cause significant expenditure and diversion of management attention. We may be faced with significant monetary damages or injunctive relief against us that could have an adverse impact on our business and results of operations should we fail to prevail in certain matters.
We expect to continue to incur capital expenditures and operating costs as a result of our compliance with existing and future environmental laws and regulations.
Our industry is subject to extensive laws and evolving regulations related to the protection of the environment. These laws and regulations have tended to become more stringent over time, continue to increase in both number and complexity and affect our operations with respect to, among other things: the discharge of pollutants into the environment; emissions into the atmosphere (including greenhouse gas emissions); and restrictions, liabilities and obligations in connection with storage, transportation, treatment and disposal of hazardous substances and waste. We are also subject to laws and regulations that require us to operate and maintain our facilities to the satisfaction of applicable regulatory authorities.
In addition, failure to comply with these laws or regulations, or failure to obtain required permits from applicable regulatory authorities, may expose us to fines, penalties or interruptions in operations. To the extent these capital expenditures or operating costs are not ultimately reflected in the prices of our products and services, or that we are subject to fines, penalties or other interruptions in our operations, our business, results of operations, financial condition and cash flows may be adversely affected.
The adoption of climate change legislation or regulation could result in increased operating costs and reduced demand for our products.
The nature of our operations could make us subject to legislation or regulations affecting the emission of greenhouse gases. The U.S. Environmental Protection Agency has promulgated (and may in the future promulgate) regulations applicable to projects involving greenhouse gas emissions above a certain threshold, and the U.S. and certain states within the U.S. have enacted, or are considering, limitations on greenhouse gas emissions. Jurisdictions outside the U.S. are also addressing greenhouse gases by legislation or regulation. In addition, efforts have been made and continue to be made at the international level toward the adoption of international treaties or protocols that would address global greenhouse gas emissions. These limitations may include the adoption of cap and trade regimes, carbon taxes, restrictive permitting, increased efficiency standards and incentives or mandates for renewable energy. For example, in January 2021, President Biden signed executive orders that represent his administrations first actions to fight climate change, which included an executive order to reenter the Paris Agreement international treaty on climate change that requires member countries to review and progress their intended contributions and set greenhouse gas reduction goals every five years beginning in 2020. The implementation of this treaty and other efforts to reduce greenhouse gas emissions could make our products more expensive, lengthen project implementation times and reduce
demand for hydrocarbons, as well as shift hydrocarbon demand toward relatively lower-carbon sources. Such legislation, regulation, treaties or protocols may also increase our compliance costs, such as for monitoring or sequestering emissions.
Risks Related to Technology
Increased information systems security threats and more sophisticated and targeted computer crime could pose a risk to our systems, networks, products and services.
Increased information systems security threats and more sophisticated, targeted computer crime pose a risk to the security of our systems and networks and the confidentiality, availability, and integrity of our data, operations, and communications. While we attempt to mitigate these risks by employing a number of measures, including security measures, employee training, comprehensive monitoring of our networks and systems, upgrading our equipment and software and maintenance of backup and protective systems, if these measures prove inadequate, we could be adversely affected by, among other things, loss or damage of intellectual property, proprietary and confidential information, and communications or customer data, having our business operations interrupted, our supply chain interrupted and increased costs to prevent, respond to, or mitigate these cyber security threats. Any significant disruption or slowdown of our systems could cause customers to cancel orders, result in us being unable to manufacture or deliver products (or cause delays), harm our reputation or cause standard business processes to become inefficient or ineffective, which could adversely affect our results of operations, financial condition and cash flows.
If we are not able to continue the technological innovation and successful commercial introduction of new products, our customers may turn to other producers to meet their requirements, which may adversely affect our results of operations, financial condition and cash flows.
Our industry and the markets into which we sell our products experience periodic technological change and ongoing product improvements. In addition, our customers may introduce new generations of their own products, adopt new or different risk profiles, or require new technological and increased performance specifications that would require us to develop customized products. Our future growth and profitability will depend on our ability to maintain or enhance technological capabilities, develop and market products and applications that meet changing customer requirements and successfully anticipate or respond to technological changes in a cost effective and timely manner. Our inability to maintain a technological edge, innovate and improve our products could cause a decline in the demand and sales of our products and adversely affect our results of operations, financial condition and cash flows.
Ineffectiveness of our enterprise resource planning (“ERP”) system may adversely affect our business and results of operations or the effectiveness of internal controls over financial reporting.
During the last five years, we implemented a new ERP system at our specialty petrochemicals facility in order to better manage our business, and we continue to implement additional improvements to the system. ERP implementations are complex and time-consuming projects that involve substantial expenditures on system software and implementation activities over a significant period of time. If the ERP system does not operate as intended, it could adversely affect our financial reporting systems and our ability to produce financial reports, the effectiveness of internal controls over financial reporting (including our disclosure controls and procedures), and our business and results of operations.
Risks Related to Financing and Tax
Changes in tax laws or exposure to additional income tax liabilities could affect our future profitability.
Factors that could materially affect our future effective tax rates include but are not limited to: changes in tax laws or the regulatory environment; changes in accounting and tax standards or practices; changes in the composition of operating income by tax jurisdiction; and our operating results before taxes.
We are subject to federal and state income taxes in the United States. Significant judgment is required in determining our provision for income taxes. We believe our tax estimates are reasonable, the final determination of tax audits and any related litigation could be materially different to that which is reflected in our Consolidated Financial Statements. Should any tax authority take issue with our estimates, our results of operations, financial condition and cash flows could be adversely affected.
We are subject to examination by federal and state tax authorities. While we regularly assess the likelihood of favorable or unfavorable outcomes resulting from examinations by the IRS and other tax authorities to determine the adequacy of our provision for income taxes, there can be no assurance that the actual outcome resulting from these examinations will not materially adversely affect our financial condition and operating results.
The covenants in the instruments that govern our outstanding indebtedness may limit our operating and financial flexibility.
The covenants in the instruments that govern our outstanding indebtedness limit our ability to, among other things: incur indebtedness and liens; make loans and investments; prepay, redeem or repurchase debt; engage in acquisitions, consolidations,
asset dispositions, sale-leaseback transactions and affiliate transactions; change our business; amend some of our debt agreements; and grant negative pledges to other creditors.
In addition, the ARC Agreement (as defined herein) also has financial covenants that require TOCCO to maintain a maximum Consolidated Leverage Ratio and minimum Consolidated Fixed Charge Coverage Ratio (each as defined in the ARC Agreement). See Part II, Item 7. Management’s Discussion and Analysis of Financial Condition and Results of Operations under the heading “Liquidity and Capital Resources.”
A failure by us or our subsidiaries to comply with the covenants and restrictions contained in the agreements governing our indebtedness could result in an event of default under such indebtedness, which could adversely affect our ability to respond to changes in our business and manage our operations. Upon the occurrence of an event of default under any of the agreements governing our indebtedness, the lenders could elect to declare all amounts outstanding to be due and payable and exercise other remedies as set forth in the agreements. Further, an event of default or acceleration of indebtedness under one instrument may constitute an event of default under another instrument. If any of our indebtedness were to be accelerated, there can be no assurance that our assets would be sufficient to repay this indebtedness in full, which could have a material adverse effect on our ability to continue to operate as a going concern.
Our indebtedness could limit cash flow available for our operations and could adversely affect our ability to service debt or obtain additional financing if necessary.
As of December 31, 2020, we had nil in borrowings outstanding under our revolving credit facility (the “Revolving Facility”) and $46.6 million in borrowings outstanding under our term loan facility (the “Term Loan Facility" and, together with the Revolving Facility, the “Credit Facilities”). Pursuant to the terms of the amended and restated credit agreement (as amended, the “ARC Agreement”) governing the Credit Facilities, we also have the option, at any time, to request an increase to the commitment under the Revolving Facility and/or the Term Loan Facility by an additional amount of up to $50.0 million in the aggregate, subject to lenders acceptance of the increased commitment and other conditions.
Although the agreements governing our existing indebtedness contain restrictions on the incurrence of additional indebtedness, these restrictions are subject to a number of important exceptions, and additional indebtedness that we may incur from time to time to finance projects or for other reasons in compliance with these restrictions could be substantial. If we incur significant additional indebtedness, the related risks that we face could increase.
For example, in May 2020, SHR and TC received loan proceeds in an aggregate principal amount of approximately $6.1 million under the new Payment Protection Program (“PPP Loans”), which may be partially or fully forgiven if we comply with the provisions of the Coronavirus Aid, Relief, and Economic Security Act of 2020 (“CARES Act”). However, since the enactment of the CARES Act, the Small Business Administration and the Treasury Department issued numerous rules and additional guidance to implement the PPP Loans under the CARES Act, application of which remains to be seen. As a result of this unclear regulatory environment, it is difficult to determine and predict with certainty eligibility and available benefits under the PPP Loans. We expect that our use of the proceeds of the PPP Loans is consistent with the intended purpose for the PPP Loans, such as maintaining the continuity of our workforce, including compensation and benefits. However, no assurance can be provided whether we will obtain forgiveness of the PPP Loans in whole or in part. If we are not successful in obtaining forgiveness of all or a portion of the PPP Loans, the unforgiven portion of such indebtedness could remain outstanding until the maturity which could reduce our liquidity. Additionally, if the SBA conducts an audit of our PPP Loans, there is no guarantee the result will be favorable in determining whether full or partial forgiveness is obtained.
Our current, or any future, indebtedness (including any unforgiven portion of the PPP Loans) could: limit our flexibility in planning for, or reacting to, changes in the markets in which we compete; place us at a competitive disadvantage relative to our competitors with less indebtedness; limit our ability to reinvest in our business; render us more vulnerable to general adverse economic, regulatory and industry conditions; and require us to dedicate a substantial portion of our cash flow to service our indebtedness.
Our ability to meet our cash requirements, including our debt service obligations, is dependent upon our ability to maintain our operating performance, which will be subject to general economic and competitive conditions and to financial, business and other factors, many of which are beyond our control. We cannot provide assurance that our business will generate sufficient cash flow from operations to fund our cash requirements and debt service obligations.
To service our current, and any future, indebtedness, we will require a significant amount of cash, which may adversely affect our future results.
Our ability to generate cash depends on many factors beyond our control, and any failure to meet our debt service obligations could harm our business, results of operations and financial condition. Our ability to make payments on and to refinance our indebtedness, and to fund working capital needs and planned capital expenditures, will depend on our ability to generate cash in the future. This, to a certain extent, is subject to general economic, financial, competitive, business, legislative, regulatory and other factors that are beyond our control.
If our business does not generate sufficient cash flow from operations or if future borrowings are not available to us in an amount sufficient to enable us to pay our indebtedness, or to fund our other liquidity needs, we may need to refinance all or a portion of our indebtedness (or otherwise seek amendment or relief from the terms of our indebtedness), on or before the maturity thereof, sell assets, reduce or delay capital investments or seek to raise additional capital, any of which could have a material adverse effect on our operations. We might not generate sufficient cash flow to repay indebtedness as currently anticipated. In addition, we may not be able to effect any of these actions, if necessary, on commercially reasonable terms or at all. Our ability to restructure or refinance our indebtedness, will depend on the condition of the capital markets and our financial condition at such time. Any refinancing of our indebtedness could be at higher interest rates and may require us to comply with more onerous covenants, which could further restrict our business operations. The terms of existing or future debt instruments may limit or prevent us from taking any of these actions. Our inability to generate sufficient cash flow to satisfy our debt service obligations, or to refinance or restructure our obligations on commercially reasonable terms or at all, would have a material adverse effect on our business, results of operations and financial conditions.
Our variable rate indebtedness subjects us to interest rate risk, which could cause our debt service obligations to increase significantly.
Borrowings under the Credit Facilities are, and additional borrowings in the future may be, at variable rates of interest that expose us to interest rate risk. If interest rates increase, our debt service obligations on the variable rate indebtedness will increase even though the amount borrowed will remain the same, and our net income and cash flows, including cash available for servicing our indebtedness, will correspondingly decrease. We may in the future enter into, interest rate swaps for our variable rate debt whereby we exchange floating for fixed rate interest payments in order to reduce exposure to interest rate volatility. However, any interest rate swaps into which we enter may not fully mitigate our interest rate risk.
ITEM 1B. Unresolved Staff Comments.
None.
ITEM 2. Properties.
Specialty Petrochemicals Facility
SHR owns and operates a specialty petrochemicals facility located in Silsbee, Texas approximately 30 miles north of Beaumont and 90 miles east of Houston. The base SHR facility consists of five operating units which, while interconnected, make distinct products through differing processes: (i) a Penhex Unit; (ii) a Reformer Unit; (iii) a Cyclo-pentane Unit; (iv) an Advanced Reformer unit; and (v) an Isomerization Unit. In addition to the base plant, SHR operates three proprietary chemical production facilities for toll processing customers. The Reformer Unit, the Advanced Reformer unit, and the Cyclo-Pentane Unit further process streams produced by the Penhex Unit.
Our present total capacity at our Silsbee facility is 13,000 barrels per day of fresh feed; however, our air permits limit us to a maximum processing rate of 11,000 barrels per day. During 2018, we constructed a 4,000 barrels per day Advanced Reformer unit to increase our capability to upgrade by-products produced from the Penhex Unit and to provide security of hydrogen supply to the plant.
In support of the Specialty Petrochemicals segment, we own approximately 100 storage tanks with total capacity of approximately 294,000 barrels, and 127 acres of land at the plant site, 107 acres of which are developed. We also own a truck and railroad loading terminal consisting of storage tanks, nine rail spurs, and truck and tank car loading facilities on approximately 63 acres of which 33 acres are developed.
GSPL owns and operates two 8-inch diameter pipelines and five 4-inch diameter pipelines, aggregating approximately 70 miles in length connecting SHR’s facility to (1) a natural gas line, (2) SHR’s truck and rail loading terminal and (3) a major petroleum products pipeline system owned by an unaffiliated third party. All pipelines are operated within Texas Railroad Commission and DOT regulations for maintenance and integrity.
Specialty Waxes Facility
TC owns and operates a specialty waxes facility from its 27.5 acre plant site located in Pasadena, Texas. The plant contains several stainless steel reactors ranging in size from 3,300 to 16,000 gallons with overhead condensing systems, two 4,000 gallon glass line reactors, five Sandvik forming belts with pastillating capabilities, five high vacuum wiped film evaporators varying in size from 12 to 20 m2 steel batch column with 10,000 gallon still pot and 20 theoretical stages of structured packing. This plant has the ability to crystallize and recover solids from the crystallization process. There are also three fully equipped, on-site laboratories. With a base product offering of polyethylene waxes, TC is well suited to manage high molecular weight materials that must be managed in the molten state. TC offers pastillating for waxes, polymers and resins, flaking capabilities, as well as solids packaging services.
In 2017, TC expanded its processing capabilities with the start-up of the hydrogenation/distillation unit. This approximately $29 million investment provides TC with state-of-the-art distillation and high-pressure hydrogenation capabilities. During 2019, TC continued to experience issues with the reliable operation of this unit in accordance with its design specifications. Toward the end of 2019 we completed a number of design corrections and other modifications including changes to operating procedures and operator training in order to improve the unit’s operational reliability. While operational reliability of the unit has improved, its performance did not fully meet design specifications.
Mineral Interest
Our only mineral interest is our ownership interest in PEVM. See Item 1 – Business – Mineral Interests.
Offices
Outside of the facilities that we own, SHR has a leased corporate and sales office in Sugar Land, Texas.
ITEM 3. Legal Proceedings.
The Company is periodically named in legal actions arising from normal business activities. We evaluate the merits of these actions and, if we determine that an unfavorable outcome is probable and can be reasonably estimated, we will establish the necessary reserves. We are not currently involved in legal proceedings that could reasonably be expected to have a material adverse effect on our business, prospects, financial condition or results of operations. We may become involved in material legal proceedings in the future.
ITEM 4. Mine Safety Disclosures.
Not applicable.
PART II
ITEM 5. Market for Registrant’s Common Equity, Related Stockholder Matters, and Issuer Purchases of Equity Securities.
Our common stock traded on the New York Stock Exchange (“NYSE”) under the symbol “TREC."
As of February 26, 2021, there were approximately 427 recorded holders (including brokers' accounts) of the Company’s common stock. We have not paid any dividends since our inception and have instead deployed earnings to fund the development of our business. Any future determination to pay dividends will be at the discretion of our board of directors and will depend on our financial condition, results of operations, capital expenditure requirements, restrictions contained in current and future financing instruments, and other factors that our board of directors deems relevant. In addition, our ability to pay dividends depends in part on our receipt of cash dividends and distributions from our subsidiaries. The terms of certain of our current debt instruments restrict the ability of our subsidiaries to pay dividends, as may the terms of any of our future debt or preferred securities.
Total Stockholder Return
The following graph compares the cumulative total stockholder return on our common stock against the NYSE Composite Index and the S&P Specialty Chemical Index, for the five years ending December 31, 2020. The graph was constructed on the assumption that $100 was invested in our common stock and each comparative on December 31, 2015, and that any dividends were fully reinvested.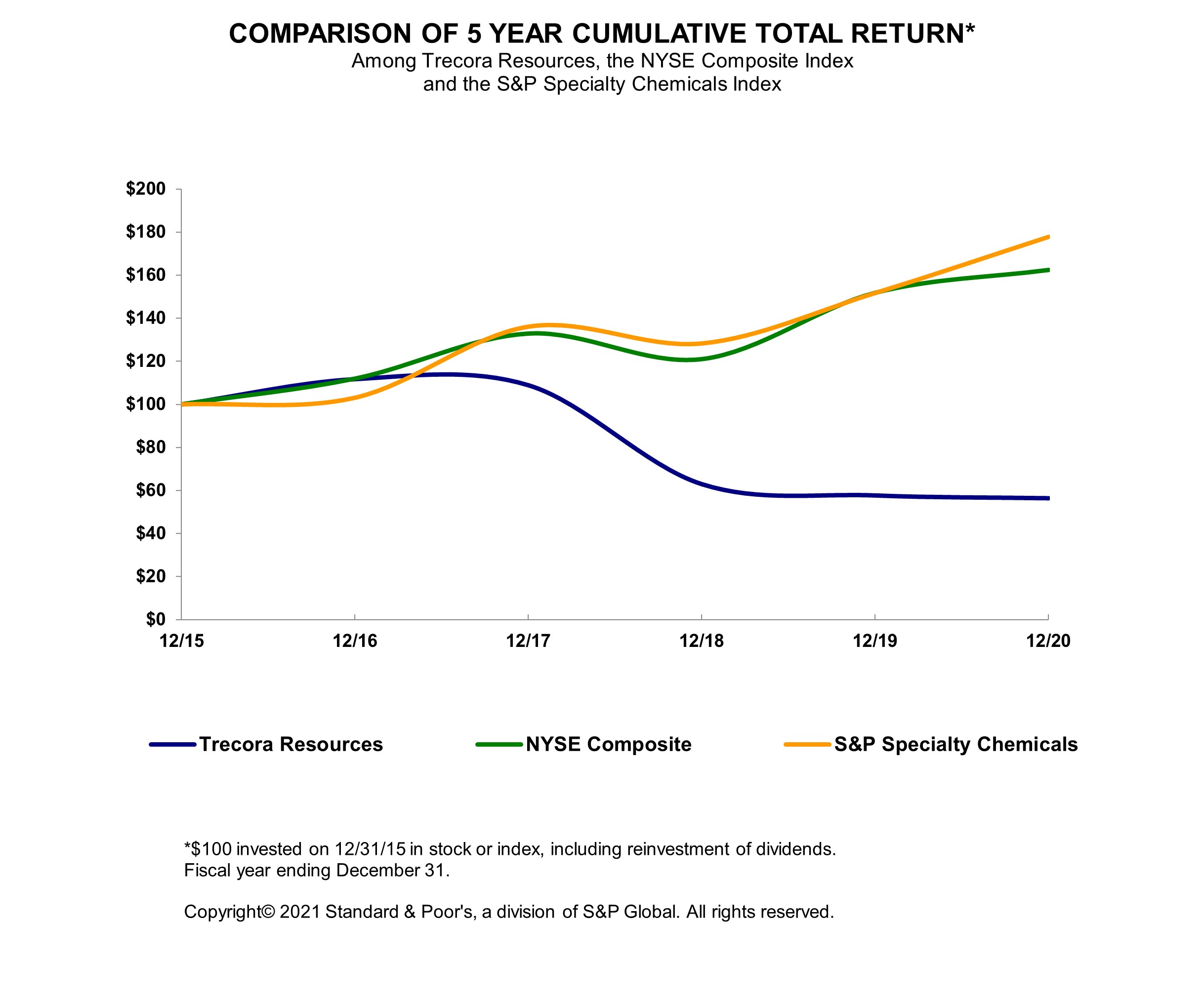
ITEM 6. Selected Financial Data.
The following is a five-year summary of selected financial data for years ended December 31 (in thousands, except per share amounts) and should be read in conjunction with the information set forth in Part II, Item 7. Management’s Discussion and Analysis of Financial Condition and Results of Operations and Part II, Item 8. Financial Statements and Supplementary Data. As a result of the sale of our ownership interest in AMAK, which was completed in September 2020, AMAK’s historical financial results are reflected in our Consolidated Financial Statements as discontinued operations for all periods presented below. See additional information related to the sale of the Company’s investment in AMAK in Note 6 to the Consolidated Financial Statements.
| | | | | | | | | | | | | | | | | | | | | | | | | | | | | |
| 2020 | | 2019 | | 2018 | | 2017 | | 2016 |
| (thousands of dollars, except per share information) |
Revenues | $ | 208,626 | | | $ | 258,959 | | | $ | 287,932 | | | $ | 245,143 | | | $ | 212,399 | |
| | | | | | | | | |
Income (loss) from continuing operations | 4,966 | | | (12,884) | | | (1,728) | | | 21,512 | | | 17,559 | |
Income (loss) from discontinued operations, net of tax | 26,209 | | | (2,090) | | | (604) | | | (3,503) | | | 1,869 | |
Net income (loss) | 31,175 | | | (14,974) | | | (2,332) | | | 18,009 | | | 19,428 | |
| | | | | | | | | |
Basic income (loss) per common share: | | | | | | | | | |
Income (loss) from continuing operations (dollars) | 0.20 | | | (0.52) | | | (0.07) | | | 0.89 | | | 0.72 | |
Income (loss) from discontinued operations, net of tax (dollars) | 1.06 | | | (0.08) | | | (0.02) | | | (0.14) | | | 0.08 | |
Net income (loss) (dollars) | 1.26 | | | (0.61) | | | (0.10) | | | 0.74 | | | 0.80 | |
| | | | | | | | | |
Diluted income (loss) per common share: | | | | | | | | | |
Income (loss) from continuing operations (dollars) | 0.20 | | | (0.52) | | | (0.07) | | | 0.86 | | | 0.70 | |
Income (loss) from discontinued operations, net of tax (dollars) | 1.03 | | | (0.08) | | | (0.02) | | | (0.14) | | | 0.07 | |
Net income (loss) (dollars) | 1.23 | | | (0.61) | | | (0.10) | | | (0.72) | | | 0.78 | |
| | | | | | | | | |
EBITDA from continuing operations (1) | 19,642 | | | 4,890 | | | 16,084 | | | 29,176 | | | 40,310 | |
Adjusted EBITDA from continuing operations (1) | 21,593 | | | 31,041 | | | 20,168 | | | 31,880 | | | 31,313 | |
Total Assets | 316,833 | | | 301,819 | | | 329,968 | | | 327,326 | | | 290,484 | |
Current portion of long-term debt | 4,194 | | | 4,194 | | | 4,194 | | | 8,061 | | | 10,145 | |
Total long-term debt obligations | 41,901 | | | 79,095 | | | 98,288 | | | 91,021 | | | 73,107 | |
(1)Non-GAAP financial measure. See the information under the heading “Non-GAAP Financial Measures" below for additional information about this measures and a reconciliation to the most directly comparable financial measure under United States generally accepted accounting principles (“GAAP”).
Non-GAAP Financial Measures
We include in this Annual Report on Form 10-K the non-GAAP financial measures of EBITDA from continuing operations and Adjusted EBITDA from continuing operations and provide reconciliations from our most directly comparable GAAP financial measure to those measures.
We believe these financial measures provide users of our financial statements with supplemental information that may be useful in evaluating our operating performance. We also believe that such non-GAAP measures, when read in conjunction with our operating results presented under GAAP, can be used to better assess our performance from period to period and relative to performance of other companies in our industry, without regard to financing methods, historical cost basis or capital structure. These measures are not measures of financial performance or liquidity under GAAP and should be considered in addition to, and not as a substitute for, analysis of our results under GAAP.
We define EBITDA from continuing operations as net income (loss) from continuing operations plus interest expense, income tax expense (benefit), depreciation and amortization. We define Adjusted EBITDA from continuing operations as EBITDA from continuing operations plus share–based compensation, plus restructuring and severance expenses, plus impairment losses and plus or minus gains or losses on disposal of assets.
The following table presents a reconciliation of net income (loss), our most directly comparable GAAP financial performance measure for each of the periods presented, to EBITDA from continuing operations and Adjusted EBITDA from continuing operations.
| | | | | | | | | | | | | | | | | | | | | | | | | | | | | |
| 2020 | | 2019 | | 2018 | | 2017 | | 2016 |
Net income (loss) | $ | 31,175 | | | $ | (14,974) | | | $ | (2,332) | | | $ | 18,009 | | | $ | 19,428 | |
Income (loss) from discontinued operations, net of tax | 26,209 | | | (2,090) | | | (604) | | | (3,503) | | | 1,869 | |
Income (loss) from continuing operations | 4,966 | | | (12,884) | | | (1,728) | | | 21,512 | | | 17,559 | |
| | | | | | | | | |
Interest expense | 2,491 | | | 5,139 | | | 4,100 | | | 2,931 | | | 1,981 | |
Derivative (gains) losses on interest rate swap | — | | | — | | | — | | | (3) | | | 4 | |
Depreciation and amortization | 16,148 | | | 16,201 | | | 14,358 | | | 10,961 | | | 9,777 | |
Income tax (benefit) expense* | (3,963) | | | (3,566) | | | (646) | | | (6,228) | | | 10,989 | |
EBITDA from continuing operations | 19,642 | | | 4,890 | | | 16,084 | | | 29,173 | | | 40,310 | |
| | | | | | | | | |
Share-based compensation** | 1,912 | | | 1,319 | | | 1,422 | | | 2,707 | | | 2,552 | |
Loss on disposal of assets | 39 | | | 680 | | | — | | | — | | | — | |
Impairment of goodwill and certain intangibles | — | | | 24,152 | | | — | | | — | | | — | |
Bargain purchase gain | — | | | — | | | — | | | — | | | (11,549) | |
Loss on extinguishment of debt | — | | | — | | | 315 | | | — | | | — | |
Restructuring and severance expenses | — | | | — | | | 2,347 | | | — | | | — | |
Adjusted EBITDA from continuing operations | $ | 21,593 | | | $ | 31,041 | | | $ | 20,168 | | | $ | 31,880 | | | $ | 31,313 | |
* The Company used a statutory rate of 35% for 2016. For 2017 through 2020 the Company estimated current taxable income to be zero and calculated deferred taxes using a statutory rate of 21% based on the enacted tax rate. (See Notes 2 and 16 to the Consolidated Financial Statements).
** Reduced to reflect amount included in Restructuring and severance expenses.
ITEM 7. Management’s Discussion and Analysis of Financial Condition and Results of Operations.
Management’s Discussion and Analysis of Financial Condition and Results of Operations should be read in conjunction with Item 8. Financial Statements and Supplementary Data.
Forward Looking Statements
Some of the statements and information contained in this Annual Report on Form 10-K may constitute forward-looking statements within the meaning of the Private Securities Litigation Reform Act of 1995. Statements regarding the Company’s financial position, business strategy and plans and objectives of the Company’s management for future operations and other statements that are not historical facts, are forward-looking statements. Forward-looking statements are often characterized by the use of words such as “outlook,” “may,” “will,” “can,” “shall,” “should,” “could,” “expects,” “plans,” “anticipates,” “contemplates,” “proposes,” “believes,” “estimates,” “predicts,” “projects,” “potential,” “continue,” “intend,” or the negative of such terms and other comparable terminology, or by discussions of strategy, plans or intentions.
Forward-looking statements involve known and unknown risks, uncertainties, assumptions, and other important factors that could cause the actual results, performance or our achievements, or industry results, to differ materially from historical results, any future results, or performance or achievements expressed or implied by such forward-looking statements. Such risks, uncertainties and factors include, but are not limited to the impacts of the COVID-19 pandemic on our business, financial results and financial condition and that of our customers, suppliers, and other counterparties; general economic and financial conditions domestically and internationally; insufficient cash flows from operating activities; our ability to attract and retain key employees; feedstock, and product prices; feedstock availability and our ability to access third party transportation; competition; industry cycles; natural disasters or other severe weather events, health epidemics and pandemics (including the COVID-19 pandemic) and terrorist attacks; our ability to consummate extraordinary transactions, including acquisitions and dispositions, and realize the financial and strategic goals of such transactions; technological developments and our ability to maintain, expand and upgrade our facilities; regulatory changes; environmental matters; lawsuits; outstanding debt and other financial and legal obligations (including having to return the amounts borrowed under the PPP Loans or failing to qualify for forgiveness of such loans, in whole or in part); difficulties in obtaining additional financing on favorable conditions, or at all; local business risks in foreign countries, including civil unrest and military or political conflict, local regulatory and legal
environments and foreign currency fluctuations; and other risks detailed in Part I, Item 1A. Risk Factors and Part II, Item 7. Management’s Discussion and Analysis of Financial Condition and Results of Operations therein, and in our other filings with the SEC. Many of these risks and uncertainties are currently amplified by and will continue to be amplified by, or in the future may be amplified by, the COVID-19 pandemic and other natural disasters such as severe weather events.
There may be other factors of which we are currently unaware or deem immaterial that may cause our actual results to differ materially from the forward-looking statements. In addition, to the extent any inconsistency or conflict exists between the information included in this report and the information included in our prior releases, reports and other filings with the SEC, the information contained in this report updates and supersedes such information.
Forward-looking statements are based on current plans, estimates, assumptions and projections, and, therefore, you should not place undue reliance on them. Forward-looking statements speak only as of the date they are made, and we undertake no obligation to update them in light of new information or future events.
Overview
The following discussion and analysis of our financial results, as well as the accompanying Consolidated Financial Statements and related notes to Consolidated Financial Statements to which they refer, are the responsibility of our management. Our accounting and financial reporting fairly reflect our business model which is based on the manufacturing and marketing of specialty petrochemicals products and waxes and providing custom manufacturing services.
Our preferred supplier position into the specialty petrochemicals market is derived from the combination of our reputation as a reliable supplier established over many years, the very high purity of our products, and a focused approach to customer service. In specialty waxes, we are able to deliver to our customers a product performance and price point that we believe is unique to our market; while the diversity of our custom processing assets and capabilities offers solutions to our customers that we believe are uncommon along the U.S. Gulf Coast.
Enabling our success in these businesses is a commitment to operational excellence which establishes a culture that prioritizes the safety of our employees and communities in which we operate, the integrity of our assets and regulatory compliance. This commitment drives a change to an emphasis on forward-looking, leading-indicators of our results and proactive steps to continuously improve our performance. We bring the same commitment to excellence to our commercial activities where we focus on the value proposition to our customers while understanding opportunities to maximize our value capture through service and product differentiation, supply chain and operating cost efficiencies and diversified supply options. We believe our focus on execution, meeting the needs of our customers, and growing our business while maintaining prudent control of our costs, will significantly contribute to enhanced shareholder value.
Business Environment and Risk Assessment
We believe we are well-positioned to participate in the US chemical industry growth driven by new investments and overall economic growth. While petrochemical prices are volatile on a short-term basis and depend on the demand of our customers' products, our investment decisions are based on our long-term business outlook using a disciplined approach in selecting and pursuing the most attractive investment opportunities.
The global impact of COVID-19 has resulted in various emergency measures to curb the spread of the virus. We continue to monitor the progression of the COVID-19 pandemic on a daily basis. Our guiding principle is, and has always been, the protection of our people and the communities in which we work, as well as maintaining the overall integrity of our assets. While our essential plant personnel remain on-site, many of our other employees are working remotely. We are continuing to follow the orders and guidance of federal, state, and local governmental agencies, as we maintain our own stringent protocols in an effort to mitigate the spread of the virus and protect the health of our employees, customers, and suppliers as well as the communities in which we work. As an organization, we adopted social distancing behaviors early, executed the necessary changes to enable all possible job duties to be performed remotely and rapidly identified and executed the necessary adjustments to support optimal productivity for all remote workers.
To date, our plants have continued to operate as normal, and our supply chain has generally remained intact, with adequate availability of raw materials. Importantly, under the U.S. Department of Homeland Security guidance issued on April 17, 2020 as updated through August 18, 2020, as well as many related state and local governmental orders, chemical manufacturing sites are considered essential critical infrastructure, and as such, are not currently subject to closure in the locations where we operate. Although there has been some disruption in global logistics channels, we have not experienced significant delays in fulfillment of customer orders.
The COVID-19 pandemic has had an impact on our business, results of operations, financial position and liquidity for the year ended December 31, 2020. In comparison to 2019, we saw reduced demand for our products and services in certain end markets, including durable goods such as automotive and construction, which we attribute to the economic slowdown caused by
the COVID-19 pandemic. This weakened demand in certain end markets is likely to continue into 2021, and could spread more broadly to our other end markets.
Our management will continue to actively monitor the impact of the global pandemic on our business, results of operations, financial condition, liquidity, suppliers, industry, investments, and workforce. We do not currently anticipate any material impairments, with respect to intangible assets, long–lived assets, or right of use assets, increases in allowances for credit losses from our customers, restructuring charges, other expenses, or changes in accounting judgments to have a material impact on our Consolidated Financial Statements.
Specialty Petrochemicals Segment
SHR’s specialty petrochemicals sales decreased in 2020 compared to 2019. Product sales revenue decreased 23.6% driven by volume decline of 11.4%, primarily due to the impact of COVID-19 on our customers and end markets. Product prices were lower in 2020 compared to 2019 primarily due to lower feedstock costs. During 2020, SHR continued to emphasize our competitive advantages achieved through our high quality products and outstanding customer service and responsiveness. We also continued to make strides in improving safety and plant reliability.
During 2020, natural gasoline feedstock costs were approximately 27% lower than 2019, reflecting lower crude oil prices. Approximately 65% of our prime products are sold under formula pricing whereby feedstock price is passed along to the customer typically with a one month lag. Falling feedstock costs during the first half of 2020 assisted prime products margins while we saw a narrowing of margins in the second half of 2020 due to rising feedstock costs. Our by-product margins were materially lower compared to 2019 due to lower by-product component prices.
Specialty Waxes Segment
Sales revenues for our specialty waxes business increased approximately 4.7% in 2020 from 2019 as we had higher wax product revenues and higher custom processing revenues. The increase in revenues was due to an increase in wax feed supply as compared to 2019, where wax feed supply disruptions were impacted due to operating issues at our wax feed suppliers.
Our Specialty Waxes products are used in a variety of applications including: performance additives for hot melt adhesives; penetration and melting point modifiers for paraffin and microcrystalline waxes; lubrication and processing aides for plastics, PVC, rubber, and dry stir-in additives for inks. In oxidized forms, applications also include use in textile emulsions.
Restructuring and Severance Impact
During 2018, the Company incurred restructuring and severance expenses of $2.3 million which were included in General and Administrative Expenses. These expenses were primarily attributable to the termination of certain executives during 2018 as part of the restructuring of executive management and the reduction in the workforce at our Silsbee, Texas facility in December 2018. These expenses related to severance, stock compensation for continued vesting of time-vested shares issued under the Company’s long-term incentive plan, and certain employee benefits including medical insurance and vacation. As of December 31, 2019, there was less than $0.1 million remaining for accrued restructuring related liabilities. As of December 31, 2020, there were no remaining liabilities related to restructuring and severance.
Liquidity and Capital Resources
Working Capital
Our approximate working capital days are summarized as follows:
| | | | | | | | | | | | | | | | | |
| December 31, 2020 | | December 31, 2019 | | December 31, 2018 |
Days sales outstanding in accounts receivable | 40.0 | | | 37.1 | | | 34.4 | |
Days sales outstanding in inventory | 20.5 | | | 19.2 | | | 21.0 | |
Days sales outstanding in accounts payable | 22.9 | | | 20.6 | | | 24.2 | |
Days of working capital | 37.7 | | | 35.7 | | | 31.1 | |
Our days sales outstanding in accounts receivable increased from 2019 to 2020 due to a recovery in sales late in the fourth quarter of 2020 and the associated timing of related receivables.
Our days sales outstanding in inventory increased from 2019 to 2020 due to lower daily sales primarily in our Specialty Petrochemicals segment.
Our days sales outstanding in accounts payable increased from 2019 to 2020 due primarily to higher accrued payables in our Specialty Petrochemicals segment.
Sources and Uses of Cash
Cash and cash equivalents increased $49.5 million during the year ended December 31, 2020. The change in cash and cash equivalents is summarized as follows:
| | | | | | | | | | | | | | | | | |
| 2020 | | 2019 | | 2018 |
Net cash provided by (used in) | (in thousands) |
Operating activities | $ | 25,565 | | | $ | 25,121 | | | $ | 19,895 | |
Investing activities | 55,329 | | | (6,031) | | | (19,871) | |
Financing activities | (31,375) | | | (19,680) | | | 3,683 | |
Increase (decrease) in cash and equivalents | $ | 49,519 | | | $ | (590) | | | $ | 3,707 | |
Cash and cash equivalents | 55,664 | | | 6,145 | | | 6,735 | |
Operating Activities
Operating activities generated cash of $25.6 million during fiscal 2020 as compared with $25.1 million of cash provided during fiscal 2019. Net income increased by $46.1 million while cash provided by operations increased by $0.4 million from 2019 to 2020. Net income for 2020 included net income from discontinued operations related to the sale of AMAK of $26.2 million while net loss for 2019 included a non-cash impairment charge for goodwill and certain intangible assets of $24.2 million.
Operating activities generated cash of $25.1 million during fiscal 2019 as compared with $19.9 million of cash provided during fiscal 2018. Net loss increased by $12.6 million while cash provided by operations increased by $5.2 million from 2018 to 2019 due primarily to the following factors:
•Net loss for 2019 included a non-cash impairment charge for goodwill and certain intangible assets of $24.2 million; and
•Trade receivables decreased $0.8 million in 2019 as compared to an increase of $1.5 million in 2018.
These significant sources of cash were partially offset by the following decreases in cash provided by operations:
•Accounts payable and accrued liabilities decreased $4.9 million in 2019 (primarily due to payoff of catalyst purchased at the end of 2018) as compared to an increase of $2.2 million in 2018 (also primarily due to catalyst purchases);
•Income taxes receivable were flat in 2019, as compared to a decrease of $5.4 million in 2018 (primarily due to collection of federal and state research and development credits, carryback claims, and refunds of tax payments on deposit); and
•Net loss for 2019 included non-cash deferred income tax liability of $3.0 million as compared to non-cash deferred income tax liability of $1.4 million in 2018.
Investing Activities
Cash provided by investing activities during fiscal 2020 was approximately $55.3 million, representing an increase of approximately $61.4 million compared to fiscal 2019. The primary source of the funds provided by investing activities was $68.5 million of proceeds, net of the deposit previously paid, received in connection with the sale of our ownership interest in AMAK, discussed in Note 6 to the Consolidated Financial Statements, offset by additions of plant, pipeline and equipment of approximately $13.4 million.
Cash used in investing activities during fiscal 2019 was approximately $6.0 million, representing a decrease of approximately $13.8 million compared to fiscal 2018. The majority of the decrease was due to the completion of construction projects for the Advanced Reformer unit. During 2019, major capital expenditures included improvements to plant safety and maintenance projects at SHR and TC and feedstock pipeline maintenance and upgrade work at SHR.
Financing Activities
Cash used in financing activities during fiscal 2020 was approximately $31.4 million as compared to $19.7 million during fiscal 2019. In the first quarter of 2020, we drew $20.0 million under our Revolving Facility as a precaution in light of the uncertainty caused by the COVID-19 pandemic. We also received PPP Loans of $6.1 million to maintain the continuity of our workforce, including maintaining compensation and benefits. Utilizing a portion of the net proceeds from the sale of our investment in AMAK, together with cash on hand, we repaid our outstanding balance on our Revolving Facility of $23 million at the end of the second quarter and further reduced our debt with a $30 million prepayment toward our Term Loan Facility. We also made scheduled payments of $4.4 million on our Term Loan Facility.
Cash used in financing activities during fiscal 2019 was approximately $19.7 million versus cash provided of $3.7 million during fiscal 2018. During 2019, we made principal payments on our outstanding Credit Facilities of $21.4 million. We drew $2.0 million on Revolving Facility for working capital purposes. See Note 13 to the Consolidated Financial Statements for additional discussion on long-term debt.
Anticipated Cash Needs
The COVID-19 pandemic has resulted in significant economic uncertainty and market volatility. In response, we have taken steps to address our liquidity needs during this uncertain period. As of December 31, 2020, we have approximately $55.7 million in cash, combined with borrowing availability on our Revolving Facility of approximately $52.4 million. We also benefited from certain provisions of the CARES Act, including certain changes to U.S. tax law and borrowings under the PPP Loans that we believed were essential to support the continuity of our workforce. As a result, we believe the Company is able to support its operating requirements and capital expenditures through internally generated funds supplemented with cash on our balance sheet and availability under our Revolving Facility.
Capital Resources and Requirements
Capital expenditures increased 32% from 2019 to 2020. The majority of the increase was due to maintenance and upkeep of our GSPL pipeline which is used to transport our feedstock to the Silsbee facility. In addition, we had capital expenditures for storage tank replacements and upgrades and levee upgrades also at SHR. During 2020 we expended approximately $4.5 million on upgrades to the pipeline for GSPL, approximately $1.7 million to replace and upgrade tanks, and $0.4 million on levee upgrades.
At December 31, 2020, there was borrowing availability of approximately $52.4 million on our Revolving Facility. We believe that operating cash flows along with cash on the balance sheet and credit availability will be sufficient to finance our 2021 operations and capital expenditures. See Note 13 to the Consolidated Financial Statements for additional discussion regarding credit availability.
The table below summarizes the following contractual obligations of the Company:
| | | | | | | | | | | | | | | | | | | | | | | | | | | | | |
| Payments due by period |
Contractual Obligations | Total | | Less than 1 year | | 1-3 years | | 3-5 years | | More than 5 years |
| (thousands of dollars) |
Operating Lease Obligations | $ | 14,898 | | | $ | 3,703 | | | $ | 6,758 | | | $ | 3,355 | | | $ | 1,082 | |
Purchase Obligations | 9,799 | | | 9,799 | | | — | | | — | | | — | |
Long-Term Debt Obligations | 46,563 | | | 4,375 | | | 42,188 | | | — | | | — | |
Total | $ | 71,260 | | | $ | 17,877 | | | $ | 48,946 | | | $ | 3,355 | | | $ | 1,082 | |
The majority of our operating lease obligations are for railcars as discussed in Note 9 of the Notes to Consolidated Financial Statements. Purchase obligations are primarily related to commitments for our undelivered feedstock and capital construction projects. The anticipated source of funds for payments due within three years that relate to contractual obligations is from a combination of cash flow from continuing operations supplemented with borrowings under our credit facility.
Results of Operations
Our Annual Report on Form 10-K for the year ended December 31, 2019 includes a discussion and analysis of our financial condition and results of operations for the year ended December 31, 2018 in Item 7 of Part II, Management’s Discussion and Analysis of Financial Condition and Results of Operations.
Comparison of Years 2020 and 2019
The tables containing financial and operating information set forth below are presented to facilitate the discussion of the results of operations, and should not be considered a substitute for, and should be read in conjunction with, the Consolidated Financial Statements.
Specialty Petrochemicals Segment
| | | | | | | | | | | | | | | | | | | | | | | |
| 2020 | | 2019 | | Change | | % Change |
| (thousands of dollars) | | |
Specialty Petrochemicals Product Sales | $ | 167,054 | | | $ | 218,743 | | | $ | (51,689) | | | (23.6) | % |
Processing | 5,296 | | | 5,568 | | | (272) | | | (4.9) | % |
Gross Revenue | $ | 172,350 | | | $ | 224,311 | | | $ | (51,961) | | | (23.2) | % |
| | | | | | | |
Volume of Sales (gallons) | | | | | | | |
Specialty Petrochemicals Products | 75,101 | | | 84,780 | | | (9,679) | | | (11.4) | % |
Prime Products Sales | 61,650 | | | 68,099 | | | (6,449) | | | (9.5) | % |
By-product Sales | 13,451 | | | 16,681 | | | (3,230) | | | (19.4) | % |
| | | | | | | |
Cost of Sales | $ | 145,166 | | | $ | 184,666 | | | $ | (39,500) | | | (21.4) | % |
Gross Margin | 15.8 | % | | 17.7 | % | | (1.9) | % | | |
Total Operating Expense* | 70,224 | | | 72,206 | | | (1,982) | | | (2.7) | % |
Natural Gas Expense* | 3,737 | | | 4,800 | | | (1,063) | | | (22.1) | % |
Operating Labor Costs* | 16,138 | | | 14,222 | | | 1,916 | | | 13.5 | % |
Transportation Costs* | 22,181 | | | 28,270 | | | (6,089) | | | (21.5) | % |
General & Administrative Expense | 10,618 | | | 10,650 | | | (32) | | | (0.3) | % |
Depreciation** | 10,611 | | | 10,556 | | | 55 | | | 0.5 | % |
Capital Expenditures | 11,334 | | | 6,955 | | | 4,379 | | | 63.0 | % |
*Included in cost of sales
**Includes $9,872 and $9,865 for 2020 and 2019 which is included in cost of sales and operating expenses
Gross Revenue
Gross revenue for the Specialty Petrochemicals segment decreased from 2019 to 2020 by approximately 23.2% due to a decrease in specialty petrochemicals sales volume and a decrease in average selling prices. Decline in selling price was primarily attributable to lower feedstock costs in 2020 which impacts pricing for our formula customers.
Specialty Petrochemicals Product Sales
Specialty petrochemicals product sales revenue decreased 23.6% from 2019 to 2020 due to a decrease in total sales volume of 11.4% and a decrease in average selling price of 5.3%. Much of the decline in sales volume was due to lower demand due to the COVID-19 pandemic, primarily driven by lower sales to polyethylene end-use markets as well as lower sales to Canadian oil sands customers. Sales to other end-use markets were also generally weaker compared to 2019. By-product sales volumes declined 19.4% as compared to 2019 primarily due to lower prime product production and sales. By-products are produced as a result of prime product production and their margins are significantly lower than margins for our prime products.
Our average selling price decreased primarily because of lower feedstock costs. A large portion of our prime products sales are contracted with pricing formulas which are tied to prior month natural gasoline prices which is our primary feedstock. Average delivered feedstock price for 2020 was approximately 27% lower than 2019 as natural gasoline prices fell with crude oil prices in the first half of 2020, while partially offset by increases in the second half of 2020. Additionally, prices for by-products in 2020 were lower than in 2019 due to lower prices for the components in our by-products stream. This also contributed to lower overall selling price.
Foreign sales volume accounted for approximately 23.6% of specialty petrochemicals sales volume and approximately 25.4% of revenue for specialty petrochemicals product sales during 2020 as compared to approximately 23.3% of volume and approximately 23.4% of revenue for specialty petrochemicals product sales during 2019. Excluding oil sands, foreign sales volumes in 2020 declined by approximately 16% from 2019, primarily due to reduced customer demand relating to the COVID-19 pandemic.
Processing Fees
Processing fees declined approximately 4.9% from 2019 to 2020 due to reduced demand impacted by the COVID-19 pandemic.
Cost of Sales (includes but is not limited to raw materials, total operating expense, natural gas, operating labor and transportation)
Cost of Sales decreased 21.4% from 2019 to 2020 due to lower raw material costs, lower operating expense and the decrease in sales volume. Our average delivered feedstock cost per gallon decreased approximately 28%. Our feedstock is natural gasoline. The market price for natural gasoline declined 33% from 2019 to 2020 mostly tracking the decline in crude oil price. The price of natural gasoline is highly correlated with the price of crude oil. Natural gasoline is the heavier liquid component remaining after ethane, propane and mixed butanes are removed from liquids produced by natural gas wells. The material is a commodity product in the oil/petrochemical markets and generally is readily available.
Total Operating Expense (includes but is not limited to natural gas, operating labor, depreciation, and transportation)
Total Operating Expense decreased 2.7% from 2019 to 2020 or approximately $2.0 million. The key driver for the decrease was lower transportation costs primarily due to lower sales volume.
Natural gas expense decreased approximately 22% from 2019 to 2020 due to a decrease in the average per unit cost and volume consumed. Consumption was lower than in 2019 primarily due to lower sales volume. The average price per MMBTU for 2020 was down approximately 4% from 2019 while volume consumed decreased to approximately 1.5 MMBTU from approximately 1.7 MMBTU.
These decreases were partially offset by an increase in operating labor driven by bonus accruals and compensation increases.
Gross Margin
Gross margin decreased from 17.7% of gross revenue in 2019 to 15.8% of gross revenue in 2020. The decrease in gross margin was driven by a decrease in margins for both prime products and by-products. Prime product margins were reduced due to lower feedstock costs and by-product margins were impacted by the lower component prices and were partially offset by lower operating costs.
Capital Expenditures
Capital expenditures in 2020 increased 63% or approximately $4.4 million from 2019 primarily due to the maintenance and upkeep of our GSPL pipeline which is used to transport our feedstock.
Specialty Waxes Segment
| | | | | | | | | | | | | | | | | | | | | | | |
| 2020 | | 2019 | | Change | | % Change |
| (thousands of dollars) |
Product Sales | $ | 25,321 | | | $ | 24,571 | | | $ | 750 | | | 3.1 | % |
Processing | 10,955 | | | 10,078 | | | 877 | | | 8.7 | % |
Gross Revenue | $ | 36,276 | | | $ | 34,649 | | | $ | 1,627 | | | 4.7 | % |
| | | | | | | |
Volume of specialty waxes sales (pounds) | 36,387 | | | 34,369 | | | 2,018 | | | 5.9 | % |
| | | | | | | |
Cost of Sales | $ | 34,782 | | | $ | 35,778 | | | $ | (996) | | | (2.8) | % |
Gross Margin (Loss) | 4.1 | % | | (3.3) | % | | 7.4 | % | | |
General & Administrative Expense* | 5,160 | | | 4,546 | | | 614 | | | 13.5 | % |
Impairment of Goodwill and Certain Intangibles | — | | | 24,152 | | | (24,152) | | | (100.0) | % |
Depreciation and Amortization** | 5,522 | | | 5,593 | | | (71) | | | (1.3) | % |
Capital Expenditures | 1,995 | | | 3,124 | | | (1,129) | | | (36.1) | % |
*Excludes impairment of goodwill and certain intangibles
**Includes $5,428 and $5,497 for 2020 and 2019, respectively, which is included in cost of sales
Product Sales
Product sales revenue increased 3.1% and product sales volume increased 5.9% from 2019 to 2020. The increase in revenues was due to an increase in wax feed supply as compared to 2019, where wax feed supply disruptions were impacted due to operating issues at our wax feed suppliers. Polyethylene wax sales saw volume increases of 8.7% and revenue from polyethylene wax increased approximately 5.9% both as a result of higher sales volume and a higher value sales mix. While product revenues and volumes increased in 2020 compared to 2019, customer demand for our specialty wax products was negatively impacted due to the COVID-19 pandemic. Average wax sales price remained relatively flat in 2020 compared to 2019.
Processing Fees
Processing fees increased 8.7% from 2019 to 2020 primarily due to higher revenues from the hydrogenation/distillation unit primarily in the first quarter of 2020. Subsequent to the first quarter, processing fees were significantly impacted by reduced customer demand for custom processing services driven by the COVID-19 pandemic.
Cost of Sales
Cost of Sales decreased approximately $1.0 million, or 2.8%, from 2019 to 2020. This decrease was driven by lower polyethylene wax feed cost and reduced operating expenses.
General and Administrative Expense
General and Administrative costs increased 13.5% from 2019 to 2020 driven by bonus accruals and insurance costs.
Capital Expenditures
Capital expenditures decreased from approximately $3.1 million to $2.0 million or 36.1% from 2019 to 2020, primarily driven by purchases of new equipment to facilitate a new customer in 2019 which was not repeated in 2020. The purchase of this specific new equipment in 2019 and 2020 was reimbursed to the Company and will be recognized as an offset to depreciation expense over the useful life of the equipment.
Corporate Segment
| | | | | | | | | | | | | | | | | | | | | | | |
| 2020 | | 2019 | | Change | | %Change |
| (in thousands) | | |
General & Administrative Expense | $ | 9,125 | | | $ | 9,190 | | | $ | (65) | | | (0.7) | % |
General corporate expenses were relatively flat from 2019 to 2020.
Investment in AMAK - Discontinued Operations
| | | | | | | | | | | | | | | | | | | | | | | |
| 2020 | | 2019 | | Change | | %Change |
| (in thousands) | | |
Equity in earnings (losses) of AMAK | $ | 702 | | | $ | (986) | | | $ | 1,688 | | | 171.2 | % |
Information concerning our investment in AMAK is set forth in Note 6 to Consolidated Financial Statements.
Recently Adopted Accounting Pronouncements
Effective January 1, 2020, we adopted Financial Accounting Standard Board (“FASB”) Accounting Standards Update (“ASU”) 2016-13, Measurement of Credit Losses on Financial Instruments, which changed the way entities recognize impairment of most financial assets. Short-term and long-term financial assets, as defined by the standard, are impacted by immediate recognition of estimated credit losses in the financial statements, reflecting the net amount expected to be collected. The adoption of this standard did not have a material impact on our Consolidated Financial Statements.
Recent Accounting Pronouncements Not Yet Adopted
In December 2019, the FASB issued ASU No. 2019-12, Income Taxes (Topic 740): Simplifying the Accounting for Income Taxes (ASU 2019-12), which simplifies the accounting for income taxes. This guidance will be effective for us in the first quarter of 2021 on a prospective basis, and early adoption is permitted. The Company does not expect that the adoption of this guidance will have a material impact on our Consolidated Financial Statements.
In March 2020, the FASB issued ASU No. 2020–04, Reference Rate Reform (Topic 848): Facilitation of the Effects of Reference Rate Reform on Financial Reporting (ASU 2020-04), which provides guidance to alleviate the burden in accounting for reference rate reform by allowing certain expedients and exceptions in applying generally accepted accounting principles to contracts, hedging relationships, and other transactions impacted by reference rate reform. The provisions of ASU 2020-04
apply only to those transactions that reference LIBOR or another reference rate expected to be discontinued due to reference rate reform. This guidance is effective from March 12, 2020 through December 31, 2022 and adoption is optional. We are currently evaluating the impact of ASU 2020-04 on our Consolidated Financial Statements.
Critical Accounting Policies
Our Consolidated Financial Statements are based on the selection and application of significant accounting policies. The preparation of Consolidated Financial Statements in conformity with GAAP requires management to make estimates and assumptions that affect the reported amounts of assets and liabilities and the reported amounts of net sales, expenses and allocated charges during the reported period. Actual results could differ from those estimates. However, we are not currently aware of any reasonably likely events or circumstances that would result in materially different results.
We believe the following accounting policies and estimates are critical to understanding the financial reporting risks present currently. These matters, and the judgments and uncertainties affecting them, are essential to understanding our reported results. See Note 2 to the Consolidated Financial Statements for further information.
Discontinued Operations
Assets that are sold or classified as held for sale are classified as discontinued operations provided that the disposal represents a strategic shift that has (or will have) a major effect on our operations and financial results (e.g., a disposal of a major geographical area, a major line of business, a major equity method investment or other major parts of an entity).
Inventories
For SHR, finished products and feedstock are recorded at the lower of cost, determined on the first-in, first-out method (“FIFO”), or market. For TC, inventory is recorded at the lower of cost or market as follows: (1) raw material cost is calculated using the weighted-average cost method and (2) product inventory cost is calculated using the specific cost method. See Note 5 to the Consolidated Financial Statements for more information.
Revenue recognition
Accounting Policy
Revenue is measured based on a consideration specified in a contract with a customer. The Company recognizes revenue when it satisfies a performance obligation by transferring control over a product or service to a customer. In evaluating when a customer has control of the asset we primarily consider whether the transfer of legal title and physical delivery has occurred, whether the customer has significant risks and rewards of ownership, and whether the customer has accepted delivery and a right to payment exists. Taxes assessed by a governmental authority that are both imposed on and concurrent with a specific revenue-producing transaction, that are collected by the Company from a customer, are excluded from revenue. Shipping and handling costs associated with outbound freight after control over a product has transferred to a customer are accounted for as a fulfillment cost and are included in cost of product sales and processing. The Company does not offer material rights of return or service-type warranties.
Nature of goods and services
The following is a description of principal activities – separated by reportable segments – from which the Company generates its revenue. For more detailed information about reportable segments, disaggregation of revenues, and contract balance disclosures, see Note 17 to the Consolidated Financial Statements.
Specialty Petrochemicals Segment
The Specialty Petrochemicals segment of the Company produces eight high purity hydrocarbons and other petroleum based products including isopentane, normal pentane, isohexane and hexane. These products are used in the production of polyethylene, packaging, polypropylene, expandable polystyrene, poly-iso/urethane foams, crude oil from the Canadian tar sands, and in the catalyst support industry. SHR’s Specialty Petrochemicals products are typically transported to customers by rail car, tank truck, iso-container and ship.
Product Sales - The Company sells individual (distinct) products to its customers on a stand-alone basis (point-of-sale) without any further integration. There is no significant modification of any one or more products sold to fulfill another promised product or service within any of the Company’s product sale transactions. The amount of consideration received for product sales is stated within the executed invoice with the customer. Payment for prime product sales is typically due and collected 30 to 60 days subsequent to point of sale.
Processing Fees - The Company’s services consist of processing customer supplied feedstocks into custom products including, if requested, services for forming, packaging, and arranging shipping. Pursuant to tolling agreements the customer retains title to the feedstocks and processed products. The performance obligation in each tolling agreement transaction is the processing of customer provided feedstocks into custom products and is satisfied over time. The amount of consideration received for product
sales is stated within the executed invoice with the customer. Payment is typically due and collected within 30 days subsequent to point of sale.
Specialty Waxes Segment
The Specialty Waxes segment of the Company manufactures and sells specialty polyethylene and poly alpha olefin waxes and also provides custom processing services for customers.
Product Sales - The Company sells individual (distinct) products to its customers on a stand-alone basis (point-of-sale) without any further integration. There is no significant modification of any one or more products sold to fulfill another promised product or service within any of the Company’s product sale transactions. The amount of consideration received for product sales is stated within the executed invoice with the customer. Payment is typically due and collected within 30 days subsequent to point of sale.
Processing Fees - The Company’s promised services consist of processing customer supplied feedstocks into custom products including, if requested, services for forming, packaging, and arranging shipping. Pursuant to tolling agreements and purchase order arrangements, the customer typically retains title to the feedstocks and processed products. The performance obligation in each tolling agreement transaction and purchase order arrangement is the processing of customer provided feedstocks into custom products and is satisfied over time. The amount of consideration received for product sales is stated within the executed invoice with the customer. Payment is typically due and collected within 30 days subsequent to point of sale.
Long-lived Assets
Long-lived assets are reviewed for impairment whenever events or changes in circumstances indicate that the carrying amount may not be recoverable from estimated future undiscounted cash flows. If the estimated future undiscounted cash flows are less than the carrying value of the assets, we calculate the amount of impairment if the carrying value of the long-lived assets exceeds the fair value of the assets. Our long-lived assets include our specialty petrochemicals facility and our specialty waxes facility.
Our specialty petrochemicals facility and specialty waxes facility are currently our revenue generating assets. The facilities were in full operation at December 31, 2020.
Goodwill and other intangible assets
Goodwill and indefinite-lived intangible assets are tested for impairment at least annually; however, these tests are performed more frequently when events or changes in circumstances indicate that the asset may be impaired. Impairment exists when carrying value exceeds fair value.
Definite-lived intangible assets are being amortized using discounted estimated future cash flows over the term of the related agreements. We continually evaluate the reasonableness of the useful lives of these assets. Once these assets are fully amortized, they will be removed from the consolidated balance sheets.
See Note 10 to the Consolidated Financial Statements for additional information.
Investment in AMAK (Held-for-Sale)
Prior to the completion of the sale of our ownership interest in AMAK, we accounted for our investment in AMAK using the equity method of accounting under which we recorded in income our share of AMAK’s income or loss for each period. The amount recorded was also adjusted to reflect the amortization of certain differences between the basis in our investment in AMAK and our share of the net assets of AMAK as reflected in AMAK’s financial statements. Any proceeds received from or payments made to AMAK were recorded as decreases or increases in the balance of our investment. See Note 6 to the Consolidated Financial Statements.
Environmental Liabilities
Our operations are subject to the rules and regulations of the TCEQ which inspects the facilities at various times for possible violations relating to air, water and industrial solid waste requirements. As noted in Item 1. Business, evidence of groundwater contamination was discovered at SHR in 1993. The recovery process, initiated in 1998, is proceeding as planned and is expected to continue for many years. See Note 14 to the Consolidated Financial Statements.
Share-Based Compensation
We expense the cost of director and employee services received in exchange for an award of equity instruments based on the grant date fair value of such instruments. For options we use the Black-Sholes model to calculate the fair value of the equity instrument on the grant date. See Note 15 to the Consolidated Financial Statements.
Income Taxes
We record deferred tax assets and liabilities to account for the expected future tax consequences of events that have been recognized in our financial statements and our tax returns. We routinely assess our deferred tax assets and reduce such assets by a valuation allowance if we deem it is more likely than not that some portion, or all, of the deferred tax assets will not be realized. In assessing the need for adjustments to existing valuation allowances, we consider all available positive and negative evidence.
We regularly assess and, if required, establish accruals for uncertain tax positions that could result from assessments of additional tax by taxing jurisdictions where we operate. We recognize a tax benefit from an uncertain tax position when it is more likely than not that the position will be sustained upon examination, based on the technical merits of the position. These accruals for uncertain tax positions are subject to a significant amount of judgment and are reviewed and adjusted on a periodic basis in light of changing facts and circumstances considering the progress of ongoing tax audits, court proceedings, changes in applicable tax laws, including tax case rulings and legislative guidance, or expiration of the applicable statute of limitations. See Note 16 to the Consolidated Financial Statements.
ITEM 7A. Quantitative and Qualitative Disclosures about Market Risk.
The market risk inherent in our financial instruments represents the potential loss resulting from adverse changes in interest rates, foreign currency rates and commodity prices. Our exposure to interest rate changes results from our variable rate debt instruments which are vulnerable to changes in short term United States prime interest rates. At December 31, 2020, 2019 and 2018, we had approximately $46.6 million, $83.9 million, and $103.3 million, respectively, in variable rate debt outstanding, excluding deferred financing costs. A hypothetical 10% change in interest rates underlying these borrowings would result in annual changes in our earnings and cash flows of approximately $0.1 million, $0.4 million, and $0.4 million at December 31, 2020, 2019 and 2018, respectively.
We do not view exchange rates exposure as significant and have not acquired or issued any foreign currency derivative financial instruments.
We purchase all of our raw materials, consisting of feedstock and natural gas, on the open market. The cost of these materials is a function of non-formula market oil and gas prices. As a result, our revenues and gross margins could be affected by changes in the price and availability of feedstock and natural gas.
At the end of 2020, market risk for 2021 was estimated as a hypothetical 10% increase in the cost of natural gas and feedstock over the market price prevailing on December 31, 2020. Assuming that 2021 total specialty petrochemicals product sales volumes stay at the same rate as 2020, the 10% market risk increase will result in an increase in the cost of natural gas and feedstock of approximately $7.8 million in fiscal 2021.
ITEM 8. Financial Statements and Supplementary Data.
The Consolidated Financial Statements of the Company and the consolidated financial statement schedules, including the report of our independent registered public accounting firm thereon, are set forth beginning on Page F-1.
ITEM 9. Changes In and Disagreements with Accountants on Accounting and Financial Disclosure.
None.
ITEM 9A. Controls and Procedures.
(a)Disclosure Controls and Procedures.
We maintain disclosure controls and procedures (as defined in Rule 13a-15(e) and 15d-15(e)) under the Exchange Act that are designed to provide reasonable assurance that the information that we are required to disclose in the reports we file or submit under the Exchange Act is recorded, processed, summarized and reported within the time periods specified in the SEC’s rules and forms, and such information is accumulated and communicated to our management, including our Chief Executive Office and Chief Financial Officer, as appropriate, to allow timely decisions regarding required disclosure. It should be noted that because of inherent limitations, our disclosure controls and procedures, however well designed and operated, can provide only reasonable, and not absolute, assurance that the objective of the disclosure controls and procedures are met.
As required by paragraph (b) of Rules 13a-15 and 15d-15 under the Exchange Act, our Chief Executive Officer, and Chief Financial Officer have evaluated the effectiveness of our disclosure controls and procedures (as such term is defined in Rules 13a-15(e) and 15d-15(e) under the Exchange Act) as of the end of the period covered by this report. Based on such evaluation, our Chief Executive Officer and Chief Financial Officer have concluded, as of the end of the period covered by this report, that our disclosure controls and procedures were effective at a reasonable assurance level to ensure that the information that we are required to disclose in the reports we file or submit under the Exchange Act is recorded, processed, summarized and reported within the time periods specified in SEC rules and forms and such information is accumulated and communicated to our
management, including our Chief Executive Officer and Chief Financial Officer as appropriate, to allow timely decisions regarding required disclosure because of the material weakness in our internal control over financial reporting described below.
(b)Management’s Annual Report on Internal Control over Financial Reporting.
Our management is responsible for establishing and maintaining adequate internal control over financial reporting. Our internal control over financial reporting is a process that is designed under the supervision of our Chief Executive Officer and Chief Financial Officer, and effected by our Board of Directors, management and other personnel, to provide assurance regarding financial reporting and the preparation of the financial statements for external purposes in accordance with accounting principles generally accepted in the United States. Our internal control of financial reporting includes those policies and procedures that:
•Pertain to the maintenance of records that, in reasonable detail, accurately and fairly reflect the transactions and dispositions of our assets;
•Provide reasonable assurance that transactions are recorded as necessary to permit preparation of financial statements in accordance with accounting principles generally accepted in the United States, and that receipts and expenditures recorded by us are being made only in accordance with authorizations of our management and Board of Directors; and
•Provide reasonable assurance regarding prevention or timely detection of unauthorized acquisition, use or disposition of our assets that could have a material effect on our financial statements.
Internal control over financial reporting has inherent limitations. Internal control over financial reporting is a process that involves human diligence and compliance and is subject to lapses in judgment and breakdowns resulting from human failures. Internal control over financial reporting also can be circumvented by collusion or improper management override. Because of such limitations, there is a risk that material misstatements will not be prevented or detected on a timely basis by internal control over financial reporting. However, these inherent limitations are known features of the financial reporting process. Therefore, it is possible to design into the process safeguards to reduce, though not eliminate, this risk. Also, projections of any evaluation of effectiveness to future periods are subject to the risk that controls may become inadequate because of changes in conditions, or that the degree of compliance with the policies and procedures may deteriorate.
Management has conducted its evaluation of the effectiveness of our internal control over financial reporting as of December 31, 2020, based upon the framework in Internal Control – Integrated Framework (2013) by the Committee of Sponsoring Organizations of the Treadway Commission. Management’s assessment included an evaluation of the design of our internal control over financial reporting and testing the operating effectiveness of our internal control over financial reporting. Management reviewed the results of the assessment with the Audit Committee of the Board of Directors. Based on its assessment and review with the Audit Committee, management concluded that our internal control over financial reporting was effective as of December 31, 2020.
(c)Attestation Report of the Registered Public Accounting Firm.
BKM Sowan Horan, LLP, an independent registered public accounting firm, has audited the Consolidated Financial Statements included in this Annual Report on Form 10-K and, as part of their audit, has issued their report, included herein, on the effectiveness of our internal control over financial reporting.
(d) Changes in Internal Control over Financial Reporting.
There have been no changes in our internal control over financial reporting during the fourth quarter of 2020 that have materially affected, or are reasonable likely to materially affect, our internal control over financial reporting. From time to time, we make changes to our internal control over financial reporting that are intended to enhance its effectiveness and which do not have a material effect on our overall internal control over financial reporting.
REPORT OF INDEPENDENT REGISTERED PUBLIC ACCOUNTING FIRM
To the Board of Directors and
Stockholders of Trecora Resources
Opinion on Internal Control over Financial Reporting
We have audited Trecora Resources’ (the Company’s) internal control over financial reporting as of December 31, 2020, based on criteria established in Internal Control-Integrated Framework (2013) issued by the Committee of Sponsoring Organizations of the Treadway Commission (COSO). In our opinion, the Company maintained, in all material respects, effective internal control over financial reporting as of December 31, 2020, based on criteria established in Internal Control-Integrated Framework (2013) issued by COSO.
We also have audited, in accordance with the standards of the Public Company Accounting Oversight Board (United States) (PCAOB), the balance sheets and the related statements of operations, stockholders’ equity, and cash flows of the Company, and our report dated March 9, 2021, expressed an unqualified opinion.
Basis for Opinion
The Company’s management is responsible for maintaining effective internal control over financial reporting, and for its assessment of the effectiveness of internal control over financial reporting, included in the accompanying Management’s Annual Report on Internal Control Over Financial Reporting. Our responsibility is to express an opinion on the Company’s internal control over financial reporting based on our audit. We are a public accounting firm registered with the PCAOB and are required to be independent with respect to the Company in accordance with the U.S. federal securities laws and the applicable rules and regulations of the Securities and Exchange Commission and the PCAOB.
We conducted our audit in accordance with the standards of the PCAOB. Those standards require that we plan and perform the audit to obtain reasonable assurance about whether effective internal control over financial reporting was maintained in all material respects. Our audit of internal control over financial reporting included obtaining an understanding of internal control over financial reporting, assessing the risk that a material weakness exists, and testing and evaluating the design and operating effectiveness of internal control based on the assessed risk. Our audit also included performing such other procedures as we considered necessary in the circumstances. We believe that our audit provides a reasonable basis for our opinion.
Definition and Limitations of Internal Control over Financial Reporting
A company’s internal control over financial reporting is a process designed to provide reasonable assurance regarding the reliability of financial reporting and the preparation of financial statements for external purposes in accordance with generally accepted accounting principles. A company’s internal control over financial reporting includes those policies and procedures that (1) pertain to the maintenance of records that, in reasonable detail, accurately and fairly reflect the transactions and dispositions of the assets of the company; (2) provide reasonable assurance that transactions are recorded as necessary to permit preparation of financial statements in accordance with generally accepted accounting principles, and that receipts and expenditures of the company are being made only in accordance with authorizations of management and directors of the company; and (3) provide reasonable assurance regarding prevention or timely detection of unauthorized acquisition, use, or disposition of the company’s assets that could have a material effect on the financial statements.
Because of its inherent limitations, internal control over financial reporting may not prevent or detect misstatements. Also, projections of any evaluation of effectiveness to future periods are subject to the risk that controls may become inadequate because of changes in conditions, or that the degree of compliance with the policies or procedures may deteriorate.
/s/ BKM Sowan Horan, LLP
Addison, Texas
March 9, 2021
ITEM 9B. Other Information.
On March 5, 2021, Joseph M. Tanner, the Senior Vice President, Commercial of the Company, provided notice that he intends to retire effective as of March 15, 2021. The Company has initiated a search for Mr. Tanner’s replacement. To ensure an orderly transition of his responsibilities, Mr. Tanner will provide consulting services to the Company under the terms of a consulting services agreement entered into with the Company on March 5, 2021 (the “Consulting Agreement”). Under the Consulting Agreement, Mr. Tanner will provide commercial support for sales of the Company’s products. The initial term of the Consulting Agreement will begin on the effective date of Mr. Tanner’s retirement, and expire on June 30, 2021, subject to automatic extension for one month periods (unless the Consulting Agreement is otherwise terminated in accordance with its terms by either party). Mr. Tanner will be entitled to a consulting fee of $1,800 per week plus reimbursement of certain out-of-pocket expenses. During the term of the Consulting Agreement, Mr. Tanner will be subject to customary provisions related to confidentiality and use of intellectual property.
The summary description of the Consulting Agreement set forth above does not purport to be complete and is qualified in its entirety by the Consulting Agreement, which is filed with this Annual Report on Form 10-K.
PART III
ITEM 10. Directors, Executive Officers and Corporate Governance.
Incorporated by reference from our Proxy Statement for our 2021 Annual Meeting of Stockholders to be filed with the SEC within 120 days after the end of the year ended December 31, 2020.
We have adopted a code of ethics entitled Standards of Business Conduct that applies to all of the Company’s directors, officers and employees, including its principal executive officer, principal financial officer, principal accounting officer and controller, and to persons performing similar functions. A copy of the Standards of Business Conduct is available on our website, www.trecora.com.
ITEM 11. Executive Compensation.
Incorporated by reference from our Proxy Statement for our 2021 Annual Meeting of Stockholders to be filed with the SEC within 120 days after the end of the year ended December 31, 2020.
ITEM 12. Security Ownership of Certain Beneficial Owners and Management and Related Stockholder Matters.
Incorporated by reference from our Proxy Statement for our 2021 Annual Meeting of Stockholders to be filed with the SEC within 120 days after the end of the year ended December 31, 2020.
ITEM 13. Certain Relationships and Related Transactions, and Director Independence.
Incorporated by reference from our Proxy Statement for our 2021 Annual Meeting of Stockholders to be filed with the SEC within 120 days after the end of the year ended December 31, 2020.
ITEM 14. Principal Accounting Fees and Services.
Incorporated by reference from our Proxy Statement for our 2021 Annual Meeting of Stockholders to be filed with the SEC within 120 days after the end of the year ended December 31, 2020.
PART IV
ITEM 15. Exhibits, Financial Statement Schedules.
(a) 1. The following financial statements are filed with this Report:
Reports of Independent Registered Public Accounting Firm
Consolidated Balance Sheets dated December 31, 2020 and 2019
Consolidated Statements of Operations for the three years ended December 31, 2020
Consolidated Statement of Stockholders' Equity for the three years ended December 31, 2020
Consolidated Statements of Cash Flows for the three years ended December 31, 2020
Notes to Consolidated Financial Statements
2. The following financial statement schedules are filed with this Report:
Schedule II -- Valuation and Qualifying Accounts for the three years ended December 31, 2020
3. The following financial statements are filed with this Report:
The financial statements of Al Masane Al Kobra Mining Company (AMAK) for the nine months ended September 30, 2020 and the years ended December 31, 2019 and 2018, required by Rule 3-09 of Regulation S-X
4. The following documents are filed or incorporated by reference as exhibits to this Report. Exhibits marked with an asterisk (*) are filed herewith. Exhibits marked with a plus sign (+) are management contracts or a compensatory plan, contract or arrangement. The below exhibit marked with a degree sign (°) has been redacted in part, in compliance with Regulation S-K Item 601. The Company agrees to furnish supplementally an unredacted copy of such exhibit to the Securities and Exchange Commission upon its request.
| | | | | |
Exhibit Number | Description |
2.1 | |
2.2 | |
2.3 | |
2.4 | |
3.1 | |
3.2 | |
4.1 | |
10.1+ | |
10.2+ | |
10.3+ | |
10.4+ | |
10.5+ | |
10.6+ | |
10.7+ | |
10.8+ | |
10.9+ | |
10.10+ | |
| | | | | |
Exhibit Number | Description |
10.11+ | |
10.12+ | |
10.13+ | |
10.14+* | |
10.15+* | |
10.16° | |
10.17 | Amended and Restated Credit Agreement, dated as of October 1, 2014, among Texas Oil & Chemical Co. II, Inc., as Borrower, certain subsidiaries of the Borrower, as Guarantors, the Lenders from time to time party thereto and Bank of America, N.A., as Administrative Agent, Swingline Lender and an L/C Issuer (incorporated by reference to Exhibit 10.2 to the Company’s Form 8–K filed on October 3, 2014 (file No. 001–33926)) |
10.18 | Second Amendment to Amended and Restated Credit Agreement, dated as of March 28, 2017, among Texas Oil & Chemical Co. II, Inc., as Borrower, certain subsidiaries of the Borrower, as Guarantors, the Lenders from time to time party thereto and Bank of America, N.A., as Administrative Agent, Swingline Lender and an L/C Issuer (incorporated by reference to Exhibit 99.1 to the Company’s form 8–K filed on March 30, 2017 (file No. 001-33926)) |
10.19 | Third Amendment to Amended and Restated Credit Agreement, dated as of July 25, 2017, among Texas Oil & Chemical Co. II, Inc., as Borrower, certain subsidiaries of the Borrower, as Guarantors, the Lenders from time to time party thereto and Bank of America, N.A., as Administrative Agent, Swingline Lender and an L/C Issuer (incorporated by reference to Exhibit 99.1 to the company’s Form 8–K filed on July 27, 2017 (file No. 001–33926)) |
10.20 | Fourth Amendment to Amended and Restated Credit Agreement, dated as of July 31, 2018, among Texas Oil & Chemical Co. II, Inc., as Borrower, certain subsidiaries of the Borrower, as Guarantors, the Lenders from time to time party thereto, Citibank, N.A., as an L/C Issuer, and Bank of America, N.A., as Administrative Agent, Swingline Lender and an L/C Issuer (incorporated by reference to Exhibit 10.1 of the Company’s Current Report on Form 8-K dated July 31, 2018 (file No. 001-33926)) |
10.21 | Fifth Amendment to Amended and Restated Credit Agreement, dated as of December 19, 2018, among Texas Oil & Chemical Co. II, Inc., as Borrower, certain subsidiaries of the Borrower, as Guarantors, the Lenders from time to time party thereto, Citibank, N.A., as an L/C Issuer, and Bank of America, N.A., as Administrative Agent, Swingline Lender and an L/C Issuer (incorporated by reference to Exhibit 10.1 of the Company’s Current Report on Form 8-K dated December 14, 2018 (file No. 001-33926)) |
10.22 | Sixth Amendment to Amended and Restated Credit Agreement, dated as of March 29, 2019, among Texas Oil & Chemical Co. II, Inc., as Borrower, certain subsidiaries of the borrower, as Guarantors, The Lenders from time to time party thereto, Citibank, N.A., as an L/C Issuer, and Bank of America, N.A. as Administrative agent, Swingline Lender and an L/C Issuer (incorporated by reference to Exhibit 10.1 of the Company’s Current Report on Form 8-K filed April 2, 2019 (file No. 001-33926)) |
10.23 | Seventh Amendment to Amended and Restated Credit Agreement, dated as of May 8, 2020, among Texas Oil & Chemical Co. II, Inc., as Borrower, certain subsidiaries of the Borrower, as Guarantors, the Lenders from time to time party thereto, Citibank, N.A., as an L/C Issuer, and Bank of America, N.A., as Administrative Agent, Swingline Lender and an L/C Issuer (incorporated by reference to Exhibit 10.1 of the Company’s Quarterly Report on Form 10-Q for the quarter ended June 30, 2020 (file No. 001-33926)) |
10.24 | |
10.25 | |
21 | |
23.1* | |
23.2* | |
| | | | | |
Exhibit Number | Description |
24* | |
31.1* | |
31.2* | |
32* | |
101.INS | XBRL Instance Document |
101.SCH | XBRL Taxonomy Schema Document |
101.CAL | XBRL Taxonomy Calculation Linkbase Document |
101.LAB | XBRL Taxonomy Label Linkbase Document |
101.PRE | XBRL Taxonomy Extension Presentation Linkbase Document |
101.DEF | XBRL Taxonomy Extension Definition Linkbase Document |
104* | Cover Page Interactive Data File (formatted as inline XBRL and included as Exhibit 101) |
ITEM 16. Form 10-K Summary.
None.
SIGNATURES
Pursuant to the requirements of Section 13 or 15(d) of the Securities Exchange Act of 1934, the Registrant has duly caused this Report to be signed on its behalf by the undersigned, thereunto duly authorized.
| | | | | | | | |
| TRECORA RESOURCES |
| | |
Dated: March 09, 2021 | By: | /s/ Patrick Quarles |
| | Patrick Quarles |
| | Chief Executive Officer and President |
KNOW ALL MEN BY THESE PRESENTS that each of the undersigned directors and officers of Trecora Resources hereby constitutes and appoints Patrick Quarles and Sami Ahmad his or her true and lawful attorney-in-fact and agent, for him or her and in his or her name, place and stead, in any and all capacities, with full power to act alone, to sign any and all amendments to this Report, and to file each such amendment to the Report, with all exhibits thereto, and any and all other documents in connection therewith, with the Securities and Exchange Commission, hereby granting unto said attorney-in-fact and agent full power and authority to do and perform any and all acts and things requisite and necessary to be done in and about the premises as fully to all intents and purposes as he or she might or could do in person, hereby ratifying and confirming all that said attorney-in-fact and agent may lawfully do or cause to be done by virtue hereof.
Pursuant to the requirements of the Securities Exchange Act of 1934, this Report has been signed below by the following persons on behalf of the Registrant in the capacities indicated on March 9, 2021.
| | | | | |
Signature | Title |
/s/ Patrick Quarles Patrick Quarles | Chief Executive Officer, President and Director (principal executive officer) |
/s/ Sami Ahmad Sami Ahmad | Chief Financial Officer (principal financial officer) |
/s/ Christopher Groves Christopher Groves | Corporate Controller (principal accounting officer) |
/s/ Karen A. Twitchell Karen A. Twitchell | Chair of the Board and Director |
/s/ Gary K. Adams Gary K. Adams | Director |
/s/ Pamela R. Butcher Pamela R. Butcher | Director |
/s/ Nicholas Carter Nicholas Carter | Director |
/s/ Adam C. Peakes Adam C. Peakes | Director |
/s/ Janet S. Roemer Janet S. Roemer | Director |
| | | | | |
INDEX TO FINANCIAL STATEMENTS | Page |
| |
| |
| |
| |
| |
| |
| |
| |
| |
| |
| |
| |
INDEX TO FINANCIAL STATEMENT SCHEDULES | |
| |
| |
| |
| |
REPORT OF INDEPENDENT REGISTERED PUBLIC ACCOUNTING FIRM
To the Board of Directors and
Stockholders of Trecora Resources
Opinion on the Consolidated Financial Statements
We have audited the accompanying consolidated balance sheets of Trecora Resources and Subsidiaries (the “Company”) as of December 31, 2020 and 2019, and the related consolidated statements of operations, stockholders’ equity and cash flows for each of the years in the three-year period ended December 31, 2020 and the related notes and schedules listed in the index at Item 15(a) (collectively referred to as the “Consolidated Financial Statements”). In our opinion, the Consolidated Financial Statements present fairly, in all material respects, the financial position of the Company as of December 31, 2020 and 2019, and the results of its operations and its cash flows for each of the years in the three-year period ended December 31, 2020, in conformity with accounting principles generally accepted in the United States of America.
We also have audited, in accordance with the standards of the Public Company Accounting Oversight Board (United States) (PCAOB), the Company’s internal control over financial reporting as of December 31, 2020, based on criteria established in Internal Control—Integrated Framework (2013) issued by the Committee of Sponsoring Organizations of the Treadway Commission (COSO), and our report dated March 9, 2021, expressed an unqualified opinion.
Basis for Opinion
These Consolidated Financial Statements are the responsibility of the Company’s management. Our responsibility is to express an opinion on the Company’s Consolidated Financial Statements based on our audits. We are a public accounting firm registered with the PCAOB and are required to be independent with respect to the Company in accordance with the U.S. federal securities laws and the applicable rules and regulations of the Securities and Exchange Commission and the PCAOB.
We conducted our audits in accordance with the standards of the PCAOB. Those standards require that we plan and perform the audit to obtain reasonable assurance about whether the Consolidated Financial Statements are free of material misstatement, whether due to error or fraud. Our audits included performing procedures to assess the risks of material misstatement of the Consolidated Financial Statements, whether due to error or fraud, and performing procedures that respond to those risks. Such procedures included examining, on a test basis, evidence regarding the amounts and disclosures in the Consolidated Financial Statements. Our audits also included evaluating the accounting principles used and significant estimates made by management, as well as evaluating the overall presentation of the Consolidated Financial Statements. We believe that our audits provide a reasonable basis for our opinion.
Critical Audit Matter
The critical audit matter communicated below is a matter arising from the current-period audit of the Consolidated Financial Statements that were communicated or required to be communicated to the audit committee and that: (1) relates to accounts or disclosures that are material to the Consolidated Financial Statements and (2) involved our especially challenging, subjective, or complex judgments. The communication of a critical audit matter does not alter in any way our opinion on the Consolidated Financial Statements, taken as a whole, and we are not, by communicating the critical audit matters below, providing a separate audit opinion on the critical audit matter or on the accounts or disclosures to which it relates.
Recoverability of the Specialty Waxes segment long-lived assets
The Company’s Specialty Waxes segment has total assets of $83.1 million, including Net Plant, Pipeline, and Equipment of $60.3 million and Net Intangibles Assets of $12.9 million. The Company considers the Specialty Waxes segment to be a single long lived asset group. A long-lived asset (asset group) shall be tested for recoverability whenever events or changes in circumstances indicate that it’s carrying amount may not be recoverable. For the year ended December 31, 2020, the Specialty Waxes segment had a net loss of $3.6 million.
We identified the recoverability of the Specialty Waxes segment long-lived assets as a critical audit matter because of the significant estimates and assumptions management used in the undiscounted cash flow analysis. Performing audit procedures to evaluate the reasonableness of these estimates and assumptions required a high degree of auditor judgment and an increased extent of effort.
How the Critical Audit Matter Was Addressed in the Audit
Our audit procedures related to the following:
•We obtained an understanding and evaluated the design of internal controls over management’s evaluation of the recoverability of long-lived assets based on the Company’s undiscounted cash flows analysis.
•We evaluated management’s ability to forecast future sales, gross profit and future capital needs by comparing actual results to management’s historical forecasts.
•We evaluated the reasonableness of significant assumptions in the undiscounted cash flow analysis, including future sales, operating costs, gross profit, and capitalization rates. In addition, we tested the mathematical accuracy of the undiscounted cash flows analysis.
/s/ BKM Sowan Horan, LLP
We have served as the Company’s auditor since 2010.
Addison, Texas
March 9, 2021
| | | | | | | | | | | |
TRECORA RESOURCES AND SUBSIDIARIES |
CONSOLIDATED BALANCE SHEETS |
| December 31, |
| 2020 | | 2019 |
| (thousands of dollars) |
ASSETS | | | |
CURRENT ASSETS | | | |
Cash and cash equivalents | $ | 55,664 | | | $ | 6,145 | |
Trade receivables, net (Note 4) | 25,301 | | | 26,320 | |
Inventories (Note 5) | 12,945 | | | 13,624 | |
Investment in AMAK (held-for-sale) (Note 6) | — | | | 32,872 | |
Prepaid expenses and other assets (Note 7) | 9,198 | | | 4,947 | |
Taxes receivable | 2,788 | | | 182 | |
Total current assets | 105,896 | | | 84,090 | |
| | | |
| | | |
| | | |
PLANT, PIPELINE, AND EQUIPMENT, NET (Note 8) | 187,104 | | | 188,919 | |
OPERATING LEASE ASSETS, NET (Note 9) | 10,528 | | | 13,512 | |
| | | |
INTANGIBLE ASSETS, NET (Note 10) | 12,893 | | | 14,736 | |
MINERAL PROPERTIES (Note 11) | 412 | | | 562 | |
TOTAL ASSETS | $ | 316,833 | | | $ | 301,819 | |
| | | |
LIABILITIES | | | |
CURRENT LIABILITIES | | | |
Accounts payable | $ | 14,447 | | | $ | 14,603 | |
| | | |
Accrued liabilities (Note 12) | 6,857 | | | 5,742 | |
| | | |
Current portion of long-term debt (Note 13) | 4,194 | | | 4,194 | |
Current portion of operating lease (Note 9) | 3,195 | | | 3,174 | |
Current portion of other liabilities | 891 | | | 922 | |
Total current liabilities | 29,584 | | | 28,635 | |
| | | |
CARES ACT, PPP Loans | 6,123 | | | — | |
LONG-TERM DEBT, net of current portion (Note 13) | 41,901 | | | 79,095 | |
POST- RETIREMENT BENEFIT, net of current portion (Note 22) | 320 | | | 338 | |
OPERATING LEASE LONG TERM (Note 9) | 7,333 | | | 10,338 | |
OTHER LIABILITIES, net of current portion | 648 | | | 595 | |
DEFERRED INCOME TAXES (Note 16) | 26,517 | | | 11,375 | |
Total liabilities | 112,426 | | | 130,376 | |
| | | |
COMMITMENTS AND CONTINGENCIES (Note 14) | | | |
| | | |
EQUITY | | | |
Common Stock ‑ authorized 40 million shares of $.10 par value; issued 24.8 and 24.6 million in 2020 and 2019, respectively, and outstanding 24.8 and 24.5 million in 2020 and 2019, respectively | 2,483 | | | 2,475 | |
Additional Paid-in Capital | 61,311 | | | 59,530 | |
| | | |
Retained Earnings | 140,324 | | | 109,149 | |
Total Trecora Resources Stockholders' Equity | 204,118 | | | 171,154 | |
Noncontrolling interest | 289 | | | 289 | |
Total equity | 204,407 | | | 171,443 | |
| | | |
TOTAL LIABILITIES AND EQUITY | $ | 316,833 | | | $ | 301,819 | |
| | | | | | | | | | | | | | | | | |
TRECORA RESOURCES AND SUBSIDIARIES |
CONSOLIDATED STATEMENTS OF OPERATIONS |
For the years ended December 31, |
| 2020 | | 2019 | | 2018 |
| (thousands of dollars) |
Revenues | | | | | |
Product sales | $ | 192,375 | | | $ | 243,314 | | | $ | 269,780 | |
Processing fees | 16,251 | | | 15,645 | | | 18,152 | |
| 208,626 | | | 258,959 | | | 287,932 | |
Operating costs and expenses | | | | | |
Cost of sales and processing (including depreciation and amortization of $15,300, $15,361, and $13,618, respectively) | 179,948 | | | 220,444 | | | 260,114 | |
Gross Profit | 28,678 | | | 38,515 | | | 27,818 | |
| | | | | |
General and Administrative Expenses | | | | | |
General and administrative | 24,892 | | | 24,386 | | | 22,532 | |
Impairment of goodwill and certain intangibles (Note 10) | — | | | 24,152 | | | — | |
Restructuring and severance (Note 21) | — | | | — | | | 2,347 | |
Depreciation | 848 | | | 840 | | | 740 | |
| 25,740 | | | 49,378 | | | 25,619 | |
| | | | | |
Operating income (loss) | 2,938 | | | (10,863) | | | 2,199 | |
| | | | | |
Other expenses | | | | | |
Interest expense | 2,491 | | | 5,139 | | | 4,100 | |
Loss on extinguishment of debt | — | | | — | | | 315 | |
Loss on disposal of assets | 39 | | | 680 | | | — | |
Miscellaneous (income) expense | (595) | | | (232) | | | 158 | |
| 1,935 | | | 5,587 | | | 4,573 | |
| | | | | |
Income (loss) from continuing operations before income tax benefit | 1,003 | | | (16,450) | | | (2,374) | |
| | | | | |
Income tax benefit | 3,963 | | | 3,566 | | | 646 | |
| | | | | |
| | | | | |
| | | | | |
| | | | | |
| | | | | |
Income (loss) from continuing operations | 4,966 | | | (12,884) | | | (1,728) | |
| | | | | |
Income (loss) from discontinued operations, net of tax | 26,209 | | | (2,090) | | | (604) | |
| | | | | |
Net income (loss) | $ | 31,175 | | | $ | (14,974) | | | $ | (2,332) | |
| | | | | |
Basic income (loss) per common share: | | | | | |
Net income (loss) from continuing operations (dollars) | $ | 0.20 | | | $ | (0.52) | | | $ | (0.07) | |
Net income (loss) from discontinued operations, net of tax (dollars) | $ | 1.06 | | | $ | (0.08) | | | $ | (0.02) | |
Net income (loss) (dollars) | $ | 1.26 | | | $ | (0.61) | | | $ | (0.10) | |
| | | | | |
Basic weighted average number of common shares outstanding | 24,802 | | | 24,698 | | | 24,438 | |
| | | | | |
Diluted income (loss) per common share: | | | | | |
Net income (loss) from continuing operations (dollars) | $ | 0.20 | | | $ | (0.52) | | | $ | (0.07) | |
Net income (loss) from discontinued operations, net of tax (dollars) | $ | 1.03 | | | $ | (0.08) | | | $ | (0.02) | |
Net income (loss) (dollars) | $ | 1.23 | | | $ | (0.61) | | | $ | (0.10) | |
| | | | | |
Diluted weighted average number of common shares outstanding | 25,356 | | | 24,698 | | | 24,438 | |
TRECORA RESOURCES AND SUBSIDIARIES
CONSOLIDATED STATEMENTS OF STOCKHOLDERS' EQUITY
For the years ended December 31, 2020, 2019, and 2018
| | | | | | | | | | | | | | | | | | | | | | | | | | | | | | | | | | | | | | | | | | | | | | | |
| TRECORA RESOURCES STOCKHOLDERS | | | | | | | | | | |
| | | | | Additional | | | | | | | | Non- | | |
| Common Stock | | Paid-In | | Treasury | | Retained | | | | Controlling | | Total |
| Shares | | Amount | | Capital | | Stock | | Earnings | | Total | | Interest | | Equity |
| (thousands) | | | | | | | | | | | | | | |
January 1, 2018 | 24,311 | | | $ | 2,451 | | | $ | 56,012 | | | $ | (196) | | | $ | 126,455 | | | $ | 184,722 | | | $ | 289 | | | $ | 185,011 | |
| | | | | | | | | | | | | | | |
Stock options | | | | | | | | | | | | | | | |
Issued to Directors | — | | | — | | | (10) | | | — | | | — | | | (10) | | | — | | | (10) | |
Issued to Employees | — | | | — | | | 154 | | | — | | | — | | | 154 | | | — | | | 154 | |
Cancellations (see Note 15) | — | | | — | | | (680) | | | — | | | — | | | (680) | | | — | | | (680) | |
Restricted stock units | | | | | | | | | | | | | | | |
Issued to Directors | — | | | — | | | 338 | | | — | | | — | | | 338 | | | — | | | 338 | |
Issued to Employees | — | | | — | | | 1,939 | | | — | | | — | | | 1,939 | | | — | | | 1,939 | |
Common stock | | | | | | | | | | | | | | | |
Issued to Directors | 188 | | | 10 | | | 489 | | | 89 | | | — | | | 588 | | | — | | | 588 | |
Issued to Employees | 183 | | | 2 | | | 127 | | | 155 | | | — | | | 284 | | | — | | | 284 | |
Stock Exchange | (65) | | | — | | | (66) | | | (65) | | | — | | | (131) | | | — | | | (131) | |
Warrants exercised | 9 | | | — | | | (9) | | | 9 | | | — | | | — | | | — | | | — | |
Net Loss | — | | | — | | | — | | | — | | | (2,332) | | | (2,332) | | | — | | | (2,332) | |
| | | | | | | | | | | | | | | |
December 31, 2018 | 24,626 | | | $ | 2,463 | | | $ | 58,294 | | | $ | (8) | | | $ | 124,123 | | | $ | 184,872 | | | $ | 289 | | | $ | 185,161 | |
| | | | | | | | | | | | | | | |
| | | | | | | | | | | | | | | |
| | | | | | | | | | | | | | | |
| | | | | | | | | | | | | | | |
Restricted stock units | | | | | | | | | | | | | | | |
Issued to Directors | — | | | — | | | 353 | | | — | | | — | | | 353 | | | — | | | 353 | |
Issued to Employees | — | | | — | | | 883 | | | — | | | — | | | 883 | | | — | | | 883 | |
Common stock | | | | | | | | | | | | | | | |
Issued to Directors | 20 | | | 1 | | | — | | | 8 | | | — | | | 9 | | | — | | | 9 | |
Issued to Employees | 104 | | | 11 | | | — | | | — | | | — | | | 11 | | | — | | | 11 | |
Net Loss | — | | | — | | | — | | | — | | | (14,974) | | | (14,974) | | | — | | | (14,974) | |
| | | | | | | | | | | | | | | |
December 31, 2019 | 24,750 | | | $ | 2,475 | | | $ | 59,530 | | | $ | — | | | $ | 109,149 | | | $ | 171,154 | | | $ | 289 | | | $ | 171,443 | |
| | | | | | | | | | | | | | | |
| | | | | | | | | | | | | | | |
| | | | | | | | | | | | | | | |
| | | | | | | | | | | | | | | |
Restricted stock units | | | | | | | | | | | | | | | |
Issued to Directors | — | | | — | | | 1,369 | | | — | | | — | | | 1,369 | | | — | | | 1,369 | |
Issued to Employees | — | | | — | | | 420 | | | — | | | — | | | 420 | | | — | | | 420 | |
Common stock | | | | | | | | | | | | | | | |
Issued to Directors | 56 | | | 5 | | | (5) | | | — | | | — | | | — | | | — | | | — | |
Issued to Employees | 27 | | | 3 | | | (3) | | | — | | | — | | | — | | | — | | | — | |
Net Income | — | | | — | | | — | | | — | | | 31,175 | | | 31,175 | | | — | | | 31,175 | |
| | | | | | | | | | | | | | | |
December 31, 2020 | 24,833 | | | $ | 2,483 | | | $ | 61,311 | | | $ | — | | | $ | 140,324 | | | $ | 204,118 | | | $ | 289 | | | $ | 204,407 | |
| | | | | | | | | | | | | | | | | |
TRECORA RESOURCES AND SUBSIDIARIES |
CONSOLIDATED STATEMENTS OF CASH FLOWS |
For the years ended December 31, |
| | | | | |
| 2020 | | 2019 | | 2018 |
| (thousands of dollars) |
OPERATING ACTIVITIES | | | | | |
Net Income (Loss) | $ | 31,175 | | | $ | (14,974) | | | $ | (2,332) | |
Income (Loss) from Discontinued Operations | 26,209 | | | (2,090) | | | (604) | |
Income (Loss) from Continuing Operations | $ | 4,966 | | | $ | (12,884) | | | $ | (1,728) | |
Adjustments to reconcile Income (Loss) from Continuing Operations to Net Cash Provided by Operating Activities: | | | | | |
Depreciation and Amortization | 14,306 | | | 14,345 | | | 12,497 | |
Amortization of Intangible Assets | 1,842 | | | 1,856 | | | 1,861 | |
| | | | | |
Stock-based Compensation | 1,912 | | | 1,250 | | | 1,753 | |
Deferred Income Taxes | 14,553 | | | (2,993) | | | (1,377) | |
Postretirement Obligation | (7) | | | (38) | | | (825) | |
Bad Debt Expense (Recoveries) | — | | | (23) | | | 152 | |
Amortization of Loan Fees | 181 | | | 181 | | | 261 | |
Loss on Extinguishment of Debt | — | | | — | | | 315 | |
Loss on Disposal of Assets | 39 | | | 680 | | | — | |
Impairment of Goodwill and Certain Intangibles | — | | | 24,152 | | | — | |
Changes in Operating Assets and Liabilities: | | | | | |
(Increase) Decrease in Trade Receivables | 1,018 | | | 816 | | | (1,485) | |
(Increase) Decrease in Taxes Receivable | (2,606) | | | — | | | 5,401 | |
Decrease in Inventories | 680 | | | 2,914 | | | 1,911 | |
(Increase) Decrease in Prepaid Expenses and Other Assets | (2,403) | | | (304) | | | (1,222) | |
Increase (Decrease) in Other Liabilities | (5,739) | | | 581 | | | 33 | |
Increase (Decrease) in Accounts Payable and Accrued Liabilities | 831 | | | (4,944) | | | 2,202 | |
| | | | | |
Net Cash Provided by Operating Activities - Continuing Operations | 29,573 | | | 25,589 | | | 19,749 | |
Net Cash (Used in) Provided by Operating Activities - Discontinued Operations | (4,008) | | | (468) | | | 146 | |
Net Cash Provided by Operating Activities | 25,565 | | | 25,121 | | | 19,895 | |
INVESTING ACTIVITIES | | | | | |
Additions to Plant, Pipeline and Equipment | (13,351) | | | (10,079) | | | (25,285) | |
Proceeds from PEVM | 150 | | | 27 | | | — | |
Net Cash Used in Investing Activities - Continuing Operations | (13,201) | | | (10,052) | | | (25,285) | |
Net Cash Provided by Investing Activities - Discontinued Operations | 68,530 | | | 4,021 | | | 5,414 | |
Net Cash Provided by (Used in) Investing Activities | 55,329 | | | (6,031) | | | (19,871) | |
FINANCING ACTIVITIES | | | | | |
| | | | | |
Net Cash (Paid) Received Related to Stock-Based Compensation | (123) | | | (305) | | | 860 | |
Additions to CARES Act, PPP Loans | 6,123 | | | — | | | — | |
Additions to Long-Term Debt | 20,000 | | | 2,000 | | | 18,177 | |
Repayment of Long-Term Debt | (57,375) | | | (21,375) | | | (15,354) | |
Net Cash (Used in) Provided by Financing Activities | (31,375) | | | (19,680) | | | 3,683 | |
| | | | | |
NET INCREASE (DECREASE) IN CASH AND CASH EQUIVALENTS | 49,519 | | | (590) | | | 3,707 | |
CASH AND CASH EQUIVALENTS AT BEGINNING OF YEAR | 6,145 | | | 6,735 | | | 3,028 | |
| | | | | | | | | | | | | | | | | |
TRECORA RESOURCES AND SUBSIDIARIES |
CONSOLIDATED STATEMENTS OF CASH FLOWS |
For the years ended December 31, |
| | | | | |
| 2020 | | 2019 | | 2018 |
| (thousands of dollars) |
CASH AND CASH EQUIVALENTS AT END OF YEAR | $ | 55,664 | | | $ | 6,145 | | | $ | 6,735 | |
| | | | | |
Supplemental disclosure of cash flow information: | | | | | |
Cash payments for interest | $ | 2,266 | | | $ | 4,731 | | | $ | 4,560 | |
Cash payments (net of refunds) for taxes | $ | (11,069) | | | $ | 53 | | | $ | (4,182) | |
| | | | | |
Supplemental disclosure of non-cash items: | | | | | |
Capital expansion amortized to depreciation expense | $ | 821 | | | $ | 792 | | | $ | 787 | |
Cash held in escrow by AMAK | $ | 1,877 | | | $ | — | | | $ | — | |
Foreign taxes paid by AMAK | $ | 270 | | | $ | — | | | $ | — | |
Stock exchange (Notes 10 & 18) | $ | — | | | $ | — | | | $ | 131 | |
NOTE 1 - BUSINESS AND OPERATIONS OF THE COMPANY
Trecora Resources (the “Company”) was organized as a Delaware corporation in 1967. The Company’s principal business activities are the manufacturing of various specialty petrochemicals products, specialty waxes and providing custom processing services.
The Company’s specialty petrochemicals operations are primarily conducted through a wholly-owned subsidiary, Texas Oil and Chemical Co. II, Inc. (“TOCCO”). TOCCO owns all of the capital stock of South Hampton Resources, Inc. (“SHR”) and Trecora Chemical, Inc. (“TC”). SHR owns all of the capital stock of Gulf State Pipe Line Company, Inc. (“GSPL”). SHR owns and operates a specialty petrochemicals product facility in Silsbee, Texas which manufactures high purity hydrocarbons used primarily in polyethylene, packaging, polypropylene, expandable polystyrene, poly-iso/urethane foams, Canadian tar sands, and in the catalyst support industry. TC owns and operates a facility located in Pasadena, Texas which manufactures specialty waxes and provides custom processing services. These specialty waxes are used in the production of coatings, hot melt adhesives and lubricants. GSPL owns and operates pipelines that connect the SHR facility to a natural gas line, to SHR’s truck and rail loading terminal and to a major petroleum pipeline owned by an unaffiliated third party.
The Company owns approximately 55% of the capital stock of a Nevada mining company, Pioche Ely Valley Mines, Inc. (“PEVM”), which does not conduct any substantial business activity but owns undeveloped properties in the United States.
The Company also previously owned 33% of a Saudi Arabian joint stock company, Al Masane Al Kobra Mining Company (“AMAK”). On October 2, 2019, we announced that we had entered into a Share Sale and Purchase Agreement (as amended, the “Purchase Agreement”) pursuant to which we agreed to sell our entire investment in AMAK. The share sale was completed on September 28, 2020. For more information, see Note 6.
We attribute revenues to countries based upon the origination of the transaction. All of our revenues for the years ended December 31, 2020, 2019, and 2018, originated in the United States. In addition, all of our long-lived assets are in the United States.
For convenience in this report, the terms “Company", “our", “us", “we" or “TREC" may be used to refer to Trecora Resources and its subsidiaries.
NOTE 2 - SUMMARY OF SIGNIFICANT ACCOUNTING POLICIES
Principles of Consolidation – The Consolidated Financial Statements include the balance sheets, statements of operations, stockholders' equity, and cash flows of the Company, TOCCO, TC, SHR, GSPL and PEVM. Other entities which are not controlled but over which the Company has the ability to exercise significant influence are accounted for using the equity method of accounting. All intercompany profits, transactions and balances have been eliminated.
Cash, Cash Equivalents and Short-Term Investments – Our principal banking and short-term investing activities are with local and national financial institutions. Short-term investments with an original maturity of three months or less are classified as cash equivalents.
Inventories – For SHR, finished products and feedstock are recorded at the lower of cost, determined on the first-in, first-out method (FIFO), or market. For TC, inventory is recorded at the lower of cost or market as follows: (1) raw material cost is calculated using the weighted-average cost method and (2) product inventory cost is calculated using the specific cost method.
Trade Receivables and Allowance for Doubtful Accounts – We evaluate the collectability of our trade receivables and adequacy of the allowance for doubtful accounts based upon historical experience and any specific customer financial difficulties of which we become aware. For the year ended December 31, 2020, we decreased the allowance for doubtful accounts balance by $129,000 due to the write off of previously allowed for receivables. For the year ended December 31, 2019, we decreased the balance by $23,000 due to collections of previously allowed for receivables. For the year ended December 31, 2018, we increased the balance by $152,000 due to concerns regarding collectability for a specific customer. We track customer balances and past due amounts to determine if customers may be having financial difficulties. This, along with historical experience and a working knowledge of each customer, helps determine accounts that should be written off. Amounts written off were $129,000, nil and nil in 2020, 2019 and 2018, respectively.
Discontinued Operations – Assets that are sold or classified as held for sale are classified as discontinued operations provided that the disposal represents a strategic shift that has (or will have) a major effect on our operations and financial results (e.g., a disposal of a major geographical area, a major line of business, a major equity method investment or other major parts of an entity).
Plant, Pipeline and Equipment – Plant, pipeline and equipment are stated at cost. Depreciation is provided over the estimated service lives using the straight-line method. Gains and losses from disposition are included in operations in the period incurred. Maintenance and repairs are expensed as incurred. Major renewals and improvements are capitalized.
Interest costs incurred to finance expenditures during construction phase are capitalized as part of the historical cost of constructing the assets. Construction commences with the development of the design and ends when the assets are ready for use. Capitalized interest costs are included in plant, pipeline and equipment and are depreciated over the service life of the related assets.
Labor costs incurred to self-construct assets are capitalized as part of the historical cost the assets. Construction commences with the development of the design and ends when the assets are ready for use. Capitalized labor costs are included in plant, pipeline and equipment and are depreciated over the service life of the related assets.
Platinum catalyst is included in plant, pipeline and equipment at cost. Amortization of the catalyst is based upon cost less estimated salvage value of the catalyst using the straight line method over the estimated useful life (see Note 8).
Leases – The Company enters into leases as a lessee for rail cars, rail equipment, office space and office equipment in the ordinary course of business. When procuring services, or upon entering into a contract, the Company determines whether an arrangement contains a lease at its inception. As part of that evaluation the Company considers whether there is an implicitly or explicitly identified asset in the arrangement and whether the Company, as the lessee, has the right to control the use of that asset. The Company also reviews all options to extend, terminate, or purchase its right-of-use assets at the inception of the lease and accounts for these options when they are reasonably certain of being exercised. All leases with a term of more than 12 months are recognized as right-of-use (“ROU”) assets and associated lease liabilities in the combined balance sheet. Lease liabilities are measured at the lease commencement date and determined using the present value of the lease payments not yet paid, at the Company’s incremental borrowing rate, which approximates the rate at which the Company would borrow on a secured basis. The interest rate implicit in the lease is generally not determinable in the transactions where the Company is the lessee. The ROU asset equals the lease liability adjusted for any initial direct costs, prepaid rent and lease incentives.
All of the Company’s leases are classified as operating leases. The leases include options to extend or terminate the lease when it is reasonably certain that the Company will exercise that option. The Company made a policy election to not recognize leases with a lease term of 12 months or less in the combined balance sheet. Lease expense for these leases is recognized on a straight-line basis over the lease term.
Goodwill and Other Intangible Assets – Goodwill and indefinite-lived intangible assets are tested for impairment at least annually; however, these tests are performed more frequently when events or changes in circumstances indicate that the asset may be impaired. Impairment exists when carrying value exceeds fair value. Estimates of fair value are based on appraisals, market prices for comparable assets, or internal estimates of future net cash flows.
Definite-lived intangible assets consist of customer relationships, licenses, permits and developed technology. The majority of these assets are being amortized using discounted estimated future cash flows over the term of the related agreements. Intangible assets associated with customer relationships are being amortized using the discounted estimated future cash flows method based upon assumed rates of annual customer attrition. We continually evaluate the reasonableness of the useful lives of these assets. Once these assets are fully amortized, they will be removed from the consolidated balance sheets.
During 2019 we adopted new accounting guidance and removed the second step of the goodwill impairment test. Under step two, an entity was required to determine the fair value of individual assets and liabilities of a reporting unit (including unrecognized assets and liabilities) using the procedure for determining fair values in a business combination. As a result, goodwill impairment is now measured at the amount by which a reporting unit’s carrying amount exceeds its fair value, with any impairment charge limited to the carrying amount of goodwill.
Business Combinations and Related Business Acquisition Costs – Assets and liabilities associated with business acquisitions are recorded at fair value using the acquisition method of accounting. We allocate the purchase price of acquisitions based upon the fair value of each component which may be derived from various observable and unobservable inputs and assumptions. We may use third-party valuation specialists to assist us in this allocation. Initial purchase price allocations are preliminary and subject to revision within the measurement period, not to exceed one year from the date of acquisition. The fair value of property, plant and equipment and intangible assets are based upon the discounted cash flow method that involves inputs that are not observable in the market (Level 3). Goodwill assigned represents the amount of consideration transferred in excess of the fair value assigned to identifiable assets acquired and liabilities assumed.
Business acquisition costs are expensed as incurred and are reported as general and administrative expenses in the consolidated statements of income. We define these costs to include finder’s fees, advisory, legal, accounting, valuation, and other professional consulting fees, as well as, travel associated with the evaluation and effort to acquire specific businesses.
Investment in AMAK – Prior to the completion of the sale of our ownership interest in AMAK, we accounted for our investment in AMAK using the equity method of accounting under which we recorded in income our share of AMAK’s income or loss for each period. The amount recorded was also adjusted to reflect the amortization of certain differences between the basis in our investment in AMAK and our share of the net assets of AMAK was reflected in AMAK’s financial statements (see Note 6). Any proceeds received from or payments made to AMAK were recorded as decreases or increases in the balance of our investment.
Other Assets – Other assets include a license used in specialty petrochemicals operations, spare parts inventory, insurance receivables and certain specialty petrochemicals assets. Spare parts are accounted for using FIFO.
Long-Lived Assets Impairment – Long-lived assets are reviewed for impairment whenever events or changes in circumstances indicate that the carrying amount may not be recoverable based on the undiscounted net cash flows to be generated from the asset’s use. The amount of the impairment loss to be recorded is calculated by the excess of the asset’s carrying value over its fair value. Fair value is generally determined using a discounted cash flow analysis although other factors including the state of the economy are considered.
Revenue Recognition – Revenue is measured based on a consideration specified in a contract with a customer. The Company recognizes revenue when it satisfies a performance obligation by transferring control over a product or service to a customer. In evaluating when a customer has control of the asset we primarily consider whether the transfer of legal title and physical delivery has occurred, whether the customer has significant risks and rewards of ownership, and whether the customer has accepted delivery and a right to payment exists. Taxes assessed by a governmental authority that are both imposed on and concurrent with a specific revenue-producing transaction, that are collected by the Company from a customer, are excluded from revenue. Shipping and handling costs associated with outbound freight after control over a product has transferred to a customer are accounted for as a fulfillment cost and are included in cost of product sales and processing. The Company does not offer material rights of return or service-type warranties.
The following is a description of principal activities – separated by reportable segments – from which the Company generates its revenue. For more detailed information about reportable segments, disaggregation of revenues, and contract balance disclosures, see Note 17.
Specialty Petrochemicals segment
The Specialty Petrochemicals segment of the Company produces eight high purity hydrocarbons and other petroleum based products including isopentane, normal pentane, isohexane and hexane. These products are used in the production of polyethylene, packaging, polypropylene, expandable polystyrene, poly-iso/urethane foams, crude oil from the Canadian tar sands, and in the catalyst support industry. SHR’s specialty petrochemicals products are typically transported to customers by rail car, tank truck, iso-container and ship.
Product Sales – The Company sells individual (distinct) products to its customers on a stand-alone basis (point-of-sale) without any further integration. There is no significant modification of any one or more products sold to fulfill another promised product or service within any of the Company’s product sale transactions. The amount of consideration received for product sales is stated within the executed invoice with the customer. Payment for prime product sales is typically due and collected 30 to 60 days subsequent to point of sale.
Processing Fees – The Company’s services consist of processing customer supplied feedstocks into custom products including, if requested, services for forming, packaging, and arranging shipping. Pursuant to Tolling Agreements the customer retains title to the feedstocks and processed products. The performance obligation in each Tolling Agreement transaction is the processing of customer provided feedstocks into custom products and is satisfied over time. The amount of consideration received for product sales is stated within the executed invoice with the customer. Payment is typically due and collected within 30 days subsequent to point of sale.
Specialty Waxes segment
The Specialty Waxes segment of the Company manufactures and sells specialty polyethylene and poly alpha olefin waxes and also provides custom processing services for customers.
Product Sales – The Company sells individual (distinct) products to its customers on a stand-alone basis (point-of-sale) without any further integration. There is no significant modification of any one or more products sold to fulfill another promised product or service within any of the Company’s product sale transactions. The amount of consideration received for product sales is stated within the executed invoice with the customer. Payment is typically due and collected within 30 days subsequent to point of sale.
Processing Fees – The Company’s promised services consist of processing customer supplied feedstocks into custom products including, if requested, services for forming, packaging, and arranging shipping. Pursuant to Tolling Agreements and Purchase Order Arrangements, the customer typically retains title to the feedstocks and processed products. The
performance obligation in each Tolling Agreement transaction and Purchase Order Arrangement is the processing of customer provided feedstocks into custom products and is satisfied over time. The amount of consideration received for product sales is stated within the executed invoice with the customer. Payment is typically due and collected within 30 days subsequent to point of sale.
Shipping and Handling Costs – Shipping and handling costs are classified as cost of product sales and processing and are expensed as incurred.
Retirement Plan – We offer employees the benefit of participating in a 401(k) plan. We match 100% up to 6% of pay with vesting occurring over 2 years. For years ended December 31, 2020, 2019, and 2018, matching contributions of approximately $1,271,000, $1,321,000, and $1,502,000, respectively, were made on behalf of employees.
Environmental Liabilities – Remediation costs are accrued based on estimates of known environmental remediation exposure. Ongoing environmental compliance costs, including maintenance and monitoring costs, are expensed as incurred.
Other Liabilities – We periodically make changes in or expand our custom processing units at the request of the customer. The cost to make these changes is shared by the customer. Upon completion of a project a note receivable and a deferred liability are recorded to recover the project costs which are then capitalized. At times instead of a note receivable being established, the customer pays an upfront cost. The amortization of other liabilities is recorded as a reduction to depreciation expense over the life of the contract with the customer. As of December 31 of each year, depreciation expense was offset and reduced by approximately $0.8 million, $0.8 million, and $0.8 million, for 2020, 2019, and 2018, respectively.
Net Income Per Share – We compute basic income per common share based on the weighted-average number of common shares outstanding. Diluted income per common share is computed based on the weighted-average number of common shares outstanding plus the number of additional common shares that would have been outstanding if potential dilutive common shares, consisting of stock options, unvested restricted stock units, and shares which could be issued upon conversion of debt, had been issued (see Note 18).
Foreign Currency – The functional currency for the Company and each of the Company’s subsidiaries is the US dollar (USD). Transaction gains or losses as a result of transactions denominated and settled in currencies other than the USD are reflected in the statements of income as foreign exchange transaction gains or losses. We do not employ any practices to minimize foreign currency risks. The functional and reporting currency of AMAK is the Saudi Riyal (SR). In June 1986 the SR was officially pegged to the USD at a fixed exchange rate of 1 USD to 3.75 SR; therefore, we translate SR into our reporting currency of the USD for income statement and balance sheet purposes using the fixed exchange rate. As of December 31, 2020, 2019 and 2018, foreign currency translation adjustments were not significant.
Management Estimates – The preparation of consolidated financial statements in conformity with accounting principles generally accepted in the United States of America requires management to make estimates and assumptions that affect the reported amounts of assets and liabilities and disclosure of contingent assets and liabilities at the date of the consolidated financial statements and the reported amounts of revenues and expenses during the reporting periods. Significant estimates include allowance for doubtful accounts receivable and inventory obsolescence; assessment of impairment of our long-lived assets and intangible assets; litigation liabilities, post-retirement benefit obligations, guarantee obligations, environmental liabilities, and current and deferred income taxes. Actual results could differ from these estimates.
In early 2020, the World Health Organization declared the rapidly spreading coronavirus disease (“COVID-19”) outbreak a pandemic. This pandemic has resulted in governments worldwide enacting emergency measures to combat the spread of the virus. The Company considered the impact of COVID-19 on the assumptions and estimates used and determined that there were no material adverse impacts on the Company’s results of operations and financial position at December 31, 2020. The Company is not aware of any specific event or circumstance that would require an update to its estimates or judgments or a revision of the carrying value of its assets or liabilities as of the date of issuance of the financial statements. These estimates may change, as new events occur and additional information is obtained.
Share-Based Compensation – We recognize share-based compensation of stock options granted based upon the fair value of options on the grant date using the Black-Scholes pricing model (see Note 15). Share-based compensation expense recognized during the period is based on the fair value of the portion of share-based payments awards that is ultimately expected to vest. Share-based compensation expense recognized in the consolidated statements of operations for the years ended December 31, 2020, 2019, and 2018 includes compensation expense based on the estimated grant date fair value for awards that are ultimately expected to vest, and accordingly has been reduced for estimated forfeitures. Estimated forfeitures at the time of grant are revised, if necessary, in subsequent periods if actual forfeitures differ from those estimates.
Fair Value – The carrying value of cash and cash equivalents, trade receivables, taxes receivable, accounts payable, accrued liabilities, and other liabilities approximate fair value due to the immediate or short-term maturity of these financial instruments. The fair value of variable rate long term debt and notes payable reflect recent market transactions and approximate carrying value. We used other observable inputs that would qualify as Level 2 inputs to make our assessment of the approximate fair value of our cash and cash equivalents, trade receivables, taxes receivable, accounts payable, accrued liabilities, other liabilities, notes payable and variable rate long term debt.
We measure fair value by ASC Topic 820 Fair Value. ASC Topic 820 defines fair value, establishes a framework for measuring fair value, and expands disclosures about fair value measurements. ASC Topic 820 applies to reported balances that are required or permitted to be measured at fair value under existing accounting pronouncements; accordingly, the standard amends numerous accounting pronouncements but does not require any new fair value measurements of reported balances. ASC Topic 820 emphasizes that fair value, among other things, is based on exit price versus entry price, should include assumptions about risk such as nonperformance risk in liability fair values, and is a market-based measurement, not an entity-specific measurement. When considering the assumptions that market participants would use in pricing the asset or liability, ASC Topic 820 establishes a fair value hierarchy that distinguishes between market participant assumptions based on market data obtained from sources independent of the reporting entity (observable inputs that are classified within Levels 1 and 2 of the hierarchy) and the reporting entity’s own assumptions about market participant assumptions (unobservable inputs classified within Level 3 of the hierarchy). The fair value hierarchy prioritizes inputs used to measure fair value into three broad levels.
In instances where the determination of the fair value measurement is based on inputs from different levels of the fair value hierarchy, the level in the fair value hierarchy within which the entire fair value measurement falls is based on the lowest level input that is significant to the fair value measurement in its entirety. Our assessment of the significance of a particular input to the fair value measurement in its entirety requires judgment and considers factors specific to the asset or liability.
Income Taxes – Deferred tax assets and liabilities are recognized for the future tax consequences attributable to differences between the financial statement carrying amounts of existing assets and liabilities and their respective tax bases. Deferred tax assets and liabilities are measured using enacted tax rates expected to apply to taxable income in the years in which those temporary differences are expected to be recovered or settled. The effect on deferred tax assets and liabilities of a change in tax rates is recognized in income in the period that includes the enactment date. The Company maintains a valuation allowance for a deferred tax asset when it is deemed to be more likely than not that some or all of the deferred tax asset will not be realized.
Our estimate of the potential outcome of any uncertain tax issues is subject to management’s assessment of relevant risks, facts, and circumstances existing at that time. We use a more likely than not threshold for financial statement recognition and measurement of tax position taken or expected to be taken in a tax return. To the extent that our assessment of such tax position changes, the change in estimate is recorded in the period in which the determination is made. We report tax-related interest and penalties as a component of income tax expense.
Subsequent Events – The Company has evaluated subsequent events through March 9, 2021, the date that the Consolidated Financial Statements were approved by management.
Recently Adopted Accounting Pronouncements
Effective January 1, 2020, we adopted Financial Accounting Standard Board (“FASB”) Accounting Standards Update (“ASU”) 2016-13, Measurement of Credit Losses on Financial Instruments, which changed the way entities recognize impairment of most financial assets. Short-term and long-term financial assets, as defined by the standard, are impacted by immediate recognition of estimated credit losses in the financial statements, reflecting the net amount expected to be collected. The adoption of this standard did not have a material impact on our Consolidated Financial Statements.
Recent Accounting Pronouncements Not Yet Adopted
In December 2019, the FASB issued ASU No. 2019-12, Income Taxes (Topic 740): Simplifying the Accounting for Income Taxes (ASU 2019-12), which simplifies the accounting for income taxes. This guidance will be effective for us in the first quarter of 2021 on a prospective basis, and early adoption is permitted. The Company does not expect that the adoption of this guidance will have a material impact on our Consolidated Financial Statements.
In March 2020, the FASB issued ASU No. 2020–04, Reference Rate Reform (Topic 848): Facilitation of the Effects of Reference Rate Reform on Financial Reporting (ASU 2020-04), which provides guidance to alleviate the burden in accounting for reference rate reform by allowing certain expedients and exceptions in applying generally accepted accounting principles to contracts, hedging relationships, and other transactions impacted by reference rate reform. The provisions of ASU 2020-04 apply only to those transactions that reference LIBOR or another reference rate expected to be discontinued due to reference rate reform. This guidance is effective from March 12, 2020 through December 31, 2022 and adoption is optional. We are currently evaluating the impact of ASU 2020-04 on our Consolidated Financial Statements.
NOTE 3 - CONCENTRATIONS OF REVENUES AND CREDIT RISK
We sell our products and services to companies in the chemical, plastics, and petroleum industries. We perform periodic credit evaluations of our customers and generally do not require collateral from our customers. For the years ended December 31, 2020, 2019, and 2018, one customer accounted for 15.4%, 15.0%, and 13.5%, respectively, of consolidated revenue. The associated accounts receivable balances for this customer, ExxonMobil and their affiliates, were approximately $4.1 million and $4.9 million at December 31, 2020 and 2019, respectively.
We market our products in many foreign jurisdictions. For the years ended December 31, 2020, 2019, and 2018, revenue in foreign jurisdictions accounted for approximately 24.0%, 21.9%, and 25.5% of consolidated revenue, respectively.
SHR utilizes one major supplier to purchase all our feedstock supply. The feedstock is a commodity product commonly available from other suppliers if needed. At December 31, 2020, and 2019, we owed the supplier approximately $9.2 million and $12.4 million, respectively, for feedstock purchases.
We hold our cash with various financial institutions that are insured by the Federal Deposit Insurance Corporation up to $250,000. At times during the year, cash balances may exceed this limit. We have not experienced any losses in such accounts and do not believe we are exposed to any significant risk of loss related to cash.
NOTE 4 – TRADE RECEIVABLES
| | | | | | | | | | | |
Trade receivables, net, at December 31, consisted of the following: | | | |
| 2020 | | 2019 |
| (thousands of dollars) |
Trade receivables | $ | 25,601 | | | $ | 26,749 | |
Less allowance for doubtful accounts | (300) | | | (429) | |
Trade receivables, net | $ | 25,301 | | | $ | 26,320 | |
Accounts receivable serves as collateral for our amended and restated loan agreement with a domestic bank (see Note 13).
NOTE 5 – INVENTORIES
| | | | | | | | | | | |
Inventories include the following at December 31: | | | |
| 2020 | | 2019 |
| (thousands of dollars) |
Raw material | $ | 2,580 | | | $ | 2,100 | |
Work in process | 138 | | | 142 | |
Finished products | 10,227 | | | 11,382 | |
Total inventory | $ | 12,945 | | | $ | 13,624 | |
Inventory serves as collateral for our amended and restated loan agreement with a domestic bank (see Note 13).
Inventory included products in transit valued at approximately $3.6 million and $2.9 million at December 31, 2020 and 2019, respectively.
NOTE 6 - INVESTMENT IN AMAK AND DISCONTINUED OPERATIONS
On September 28, 2020, the Company completed the final closing of the previously disclosed sale of its ownership interest in AMAK (the “Share Sale”) to AMAK and certain existing shareholders of AMAK and their assignees (collectively, the “Purchasers”). The Share Sale was completed in multiple closings pursuant to a Share Sale and Purchase Agreement, dated September 22, 2019 (which we refer to herein as the “Purchase Agreement”), among the Company, AMAK, and other Purchasers and resulted in aggregate gross proceeds to the Company of Saudi Riyals (“SAR”) 265 million (approximately $70 million) (before taxes and expenses). As of December 31, 2019, the Company had a non-controlling equity interest of 33.3% in AMAK of approximately $32.9 million.
As a condition to the effectiveness of the Purchase Agreement, the Purchasers advanced 5% of the purchase price (or approximately $3.5 million) in the form of a non-refundable deposit. Pursuant to the Purchase Agreement, (i) with respect to any Purchaser that completed the purchase of all or a portion of the ordinary shares allotted to it under the Purchase Agreement on or before March 31, 2020, the non-refundable deposit paid by such Purchaser (or a portion of such deposit for a partial closing) was credited toward the purchase price of the ordinary shares being purchased and (ii) with respect to any Purchasers that complete the purchase of all or a portion of their allotted ordinary shares after March 31, 2020 but on or
before September 28, 2020, an amount equal to 50% of the non-refundable deposit paid by such Purchasers was forfeited to the Company as liquidated damages and such amount was not applied to the purchase price paid by the applicable Purchaser.
On March 26, 2020, the Company and one Purchaser completed the first closing of the Share Sale (the “First Closing”). In connection with the First Closing, the Company sold 4,000,000 ordinary shares for aggregate gross proceeds (before taxes and transaction expenses) of SAR 40 million (or approximately $10.7 million) (inclusive of the full amount of the Purchaser’s non-refundable deposit previously paid of $0.5 million). The Company recorded a foreign tax payable of approximately $0.3 million related to the First Closing.
During the third quarter of 2020, the Company completed additional closings of the Share Sale with respect to its remaining ownership interest in AMAK. In connection with these closings, the Company sold a total of 22,467,422 ordinary shares for aggregate gross proceeds (before taxes and transaction expenses) of SAR 224 million (or approximately $59.9 million) (inclusive of $1.5 million which constituted 50% of the non-refundable deposits previously paid by certain Purchasers). As none of the third quarter 2020 closings were completed prior to March 31, 2020, the remaining portion of the initial deposits (approximately $1.5 million) were forfeited to the Company as liquidated damages and were not applied to the purchase price. These amounts are included in income from discontinued operations, net of tax. The Company recorded a foreign tax payable of approximately $1.1 million related to the third quarter 2020 closings.
In connection with the completion of the Share Sale, the Company and AMAK entered into an agreement whereby AMAK agreed to withhold approximately $2.1 million of the purchase price to pay the Company’s estimated tax obligations in Saudi Arabia. The Company is in the process of finalizing and filing the necessary tax returns in the Kingdom of Saudi Arabia. Upon payment, the Company will have a foreign tax credit which can be used to offset U.S. taxes. As of December 31, 2020, approximately $0.2 million of foreign taxes have been paid. The remaining funds withheld by AMAK are included in prepaid expenses and other assets on the Company’s consolidated balance sheets as of December 31, 2020. Subsequent to December 31, 2020, the Company instructed AMAK to pay approximately $1.1 million of the accrued foreign tax payable from the amount held by AMAK to cover the Company’s tax obligations in Saudi Arabia.
As previously disclosed, and as a result of the Company’s investment in AMAK, the Company was required to execute a limited guarantee on October 24, 2010 (the “Guarantee”) of up to 41% of a loan (the “Loan”) by the Saudi Industrial Development Fund (“SIDF”) to AMAK to fund the construction of the AMAK facilities and to provide working capital needs. The provision of personal or corporate guarantees, as applicable, by each shareholder of AMAK was a condition to SIDF providing the Loan. Pursuant to the Purchase Agreement, the Purchasers (other than AMAK) agreed, upon the completion of the Share Sale, to assume the Company’s obligation under the Guarantee (proportionately based upon such Purchaser’s percentage acquisition of ordinary shares in the Share Sale). While a formal written release of the Company from the Guarantee was not obtained from SIDF prior to closing, the Company believes that the Purchasers’ assumption of the Company’s obligation under the Guarantee effectively eliminates the Company’s liability arising under the Guarantee.
Included in discontinued operations are the following: | | | | | | | | | | | | | | | | | | | | |
| | Years Ended December 31, |
| | 2020 | | 2019 | | 2018 |
| | (thousands of dollars) |
Saudi administration and transaction expenses | | $ | (2,452) | | | $ | (187) | | | $ | 136 | |
Equity in earnings (losses) of AMAK | | 702 | | | (986) | | | (901) | |
Gain (loss) on sale of equity interest | | 34,926 | | | (1,473) | | | — | |
Income (loss) from discontinued operations before taxes | | 33,176 | | | (2,646) | | | (765) | |
Tax (expense) benefit | | (6,967) | | | 556 | | | 161 | |
Income (loss) from discontinued operations, net of tax | | $ | 26,209 | | | $ | (2,090) | | | $ | (604) | |
AMAK’s financial statements were prepared in the functional currency of AMAK which is the SAR. In June 1986 the SAR was officially pegged to the U. S. Dollar at a fixed exchange rate of 1 USD to 3.75 SAR.
The summarized results of operations and financial position for AMAK are as follows: | | | | | | | | | | | | | | | | | | | | |
Results of Operations | | Nine Months Ended September 30, | | Year Ended December 31, |
| | 2020 | | 2019 | | 2018 |
| | (thousands of dollars) |
Sales | | $ | 62,633 | | | $ | 78,350 | | | $ | 70,234 | |
Cost of sales | | (55,728) | | | (69,620) | | | (68,084) | |
Gross profit | | 6,905 | | | 8,730 | | | 2,150 | |
Selling, general, and administrative | | (4,985) | | | (13,047) | | | (7,860) | |
Operating income (loss) | | 1,920 | | | (4,317) | | | (5,710) | |
Other (expense) income | | (346) | | | 558 | | | 86 | |
Finance and interest expense | | (1,211) | | | (1,450) | | | (1,592) | |
Income (loss) before Zakat and income taxes | | 363 | | | (5,209) | | | (7,216) | |
Zakat and income tax (expense) benefit | | (490) | | | (1,801) | | | 487 | |
Net loss | | $ | (127) | | | $ | (7,010) | | | $ | (6,729) | |
| | | | | | | | | | | | | | |
Financial Position | | September 30, | | December 31, |
| | 2020 | | 2019 |
| | (thousands of dollars) |
Current assets | | $ | 29,799 | | | $ | 45,354 | |
Noncurrent assets | | 209,814 | | | 196,564 | |
Total assets | | $ | 239,613 | | | $ | 241,918 | |
| | | | |
Current liabilities | | $ | 40,919 | | | $ | 27,645 | |
Long term liabilities | | 79,122 | | | 79,348 | |
Stockholders' equity | | 119,572 | | | 134,925 | |
| | $ | 239,613 | | | $ | 241,918 | |
The equity in the earnings (losses) of AMAK included in income (loss) from discontinued operations, net of tax, on the consolidated statements of operations for the years ended December 31, 2020, 2019, and 2018, is comprised of the following: | | | | | | | | | | | | | | | | | | | | |
| | Nine Months Ended September 30, | | Year Ended December 31, |
| | 2020 | | 2019 | | 2018 |
| | (thousands of dollars) |
AMAK Net Loss | | (127) | | | (7,010) | | | (6,729) | |
| | | | | | |
| | | | | | |
Company’s share of loss reported by AMAK | | (308) | | * | (1,996) | | | (2,248) | |
Amortization of difference between Company’s investment in AMAK and Company’s share of net assets of AMAK | | 1,010 | | | 1,010 | | | 1,347 | |
Equity in earnings (losses) of AMAK | | 702 | | | (986) | | | (901) | |
* Percentage of Ownership varies during the period. | | |
NOTE 7 – PREPAID EXPENSES AND OTHER ASSETS
| | | | | | | | | | | |
Prepaid expenses and other assets at December 31 are summarized as follows: | | | |
| 2020 | | 2019 |
| (thousands of dollars) |
Prepaid license | $ | 403 | | | $ | 1,209 | |
Prepaid insurance | 4,241 | | | — | |
Spare parts | 2,376 | | | 1,857 | |
Insurance receivable | — | | | 1,148 | |
Cash held by AMAK (see Note 6) | 1,877 | | | — | |
Other prepaid expenses and assets | 301 | | | 733 | |
Total | $ | 9,198 | | | $ | 4,947 | |
NOTE 8 – PLANT, PIPELINE AND EQUIPMENT
| | | | | | | | | | | |
Plant, pipeline and equipment include the following at December 31: | | | |
| 2020 | | 2019 |
| (thousands of dollars) |
Platinum catalyst | $ | 1,580 | | | $ | 1,580 | |
Catalyst | 4,325 | | | 4,095 | |
Land | 5,428 | | | 5,428 | |
Plant, pipeline and equipment | 270,149 | | | 258,651 | |
Construction in progress | 6,422 | | | 5,052 | |
Total plant, pipeline and equipment | 287,904 | | | 274,806 | |
Less accumulated depreciation | (100,800) | | | (85,887) | |
Net plant, pipeline and equipment | $ | 187,104 | | | $ | 188,919 | |
Plant, pipeline and equipment serve as collateral for our amended and restated loan agreement with a domestic bank (see Note 13).
Interest capitalized for construction for 2020, 2019 and 2018 was approximately nil, nil and $0.7 million, respectively.
Labor capitalized for construction for 2020, 2019 and 2018 was approximately $0.6 million, $0.0 million and $2.3 million, respectively.
Catalyst amortization relating to the platinum catalyst which is included in cost of sales was approximately $1.2 million, $1.3 million and $0.1 million for 2020, 2019 and 2018, respectively.
NOTE 9 – LEASES
The components of lease expense were as follows:
| | | | | | | | | | | | | | |
| | December 31, |
($ in thousands) | Classification in the Consolidated Statements of Operations | 2020 | 2019 | 2018 |
Operating lease cost (a) | Cost of sales, exclusive of depreciation and amortization | $ | 4,088 | | $ | 4,361 | | $ | — | |
Operating lease cost (a) | Selling, general and administrative | 137 | | 137 | | — | |
Total operating lease cost | | $ | 4,225 | | $ | 4,498 | | $ | — | |
| | | | |
Finance lease cost: | | | | |
Amortization of right-of-use assets | Depreciation | — | | — | | — | |
Interest on lease liabilities | Interest Expense | — | | — | | — | |
Total finance lease cost | | $ | — | | $ | — | | $ | — | |
| | | | |
Total lease cost | | $ | 4,225 | | $ | 4,498 | | $ | — | |
| | | | |
(a) Short-term lease costs were approximately $0.5 million, $0.1 million and nil as of December 31, 2020, 2019 and 2018, respectively. |
The Company had no variable lease expense during the period. | | | | | | | | | | | | | | |
| | December 31, |
($ in thousands) | Classification on the Consolidated Balance Sheets | 2020 | | 2019 |
Assets: | | | | |
Operating | Operating lease assets | $ | 10,528 | | | $ | 13,512 | |
Finance | Property, plant, and equipment | — | | | — | |
Total leased assets | | $ | 10,528 | | | $ | 13,512 | |
| | | | |
Liabilities: | | | | |
Current | | | | |
Operating | Current portion of operating lease liabilities | $ | 3,195 | | | $ | 3,174 | |
Finance | Short-term debt and current portion of long-term debt | — | | | — | |
Noncurrent | | | | |
Operating | Operating lease liabilities | 7,333 | | | 10,338 | |
Finance | Long-term debt | — | | | — | |
Total lease liabilities | | $ | 10,528 | | | $ | 13,512 | |
| | | | | | | | | | | | | | | | | |
| December 31, |
($ in thousands) | 2020 | | 2019 | | 2018 |
Cash paid for amounts included in the measurement of lease liabilities: | | | | | |
Operating cash flows used for operating leases | $ | 3,713 | | | $ | 4,389 | | | $ | — | |
Operating cash flows used for finance leases | — | | | — | | | — | |
Financing cash flows used for finance leases | — | | | — | | | — | |
Right-of-use assets obtained in exchange for lease obligations: | | | | | |
Operating leases | $ | 206 | | | $ | 81 | | | $ | — | |
Finance leases | — | | | — | | | — | |
| | | | | | | | |
| December 31, |
| 2020 | 2019 |
Weighted-average remaining lease term (in years): | | |
Operating leases | 3.7 | 4.5 |
Finance leases | 0.0 | 0.0 |
Weighted-average discount rate: | | |
Operating leases | 4.5 | % | 4.5 | % |
Finance leases | — | % | — | % |
Nearly all of the Company’s lease contracts do not provide a readily determinable implicit rate. For these contracts, the Company’s estimated incremental borrowing rate is based on information available at the inception of the lease.
As of December 31, 2020, maturities of lease liabilities were as follows: | | | | | | | | |
($ in thousands) | Operating Leases | Finance Leases |
2020 | $ | 3,590 | | $ | — | |
2021 | 3,268 | | — | |
2022 | 2,376 | | — | |
2023 | 1,062 | | — | |
2024 | 991 | | — | |
Thereafter | 117 | | — | |
Total lease payments | $ | 11,404 | | $ | — | |
Less: Interest | 876 | | — | |
Total lease obligations | $ | 10,528 | | $ | — | |
NOTE 10 – GOODWILL AND INTANGIBLE ASSETS, NET
Goodwill
We evaluated our goodwill for impairment during the fourth quarter of 2019 in connection with our annual review. As part of our review, we assessed 2019 operating performance and its impact on the operating cash flows of our Specialty Waxes reporting unit. We concluded based on this analysis that the estimates of fair value of our Specialty Waxes reporting unit was lower than its book value, including goodwill. As a result, we recorded a non-cash impairment charge of $24.2 million in 2019, representing all of the the goodwill previously allocated to this reporting unit.
Intangible Assets
The following table summarizes the gross carrying amounts and accumulated amortization of intangible assets by major class (in thousands):
| | | | | | | | | | | | | | | | | |
| December 31, 2020 |
Intangible assets subject to amortization (Definite-lived) | Gross | | Accumulated Amortization | | Net |
Customer relationships | $ | 16,852 | | | $ | (7,022) | | | $ | 9,830 | |
Non-compete agreements | 94 | | | (94) | | | — | |
Licenses and permits | 1,471 | | | (707) | | | 764 | |
Developed technology | 6,131 | | | (3,832) | | | 2,299 | |
| | | | | |
| | | | | |
| | | | | |
| | | | | |
Total | $ | 24,548 | | | $ | (11,655) | | | $ | 12,893 | |
| | | | | | | | | | | | | | | | | |
| December 31, 2019 |
Intangible assets subject to amortization (Definite-lived) | Gross | | Accumulated Amortization | | Net |
Customer relationships | $ | 16,852 | | | $ | (5,898) | | | $ | 10,954 | |
Non-compete agreements | 94 | | | (94) | | | — | |
Licenses and permits | 1,471 | | | (601) | | | 870 | |
Developed technology | 6,131 | | | (3,219) | | | 2,912 | |
| | | | | |
| | | | | |
| | | | | |
| | | | | |
Total | $ | 24,548 | | | $ | (9,812) | | | $ | 14,736 | |
Amortization expense for intangible assets included in cost of sales for the years ended December 31, 2020, 2019, and 2018, was approximately $1.8 million, $1.9 million, and $1.9 million respectively.
Based on identified intangible assets that are subject to amortization as of December 31, 2020, we expect future amortization expenses for each period to be as follows (in thousands):
| | | | | | | | | | | | | | | | | | | | | | | | | | | | | | | | | | | | | | | | | |
| Total | | 2021 | | 2022 | | 2023 | | 2024 | | 2025 | | Thereafter |
Customer relationships | $ | 9,830 | | | $ | 1,123 | | | $ | 1,123 | | | $ | 1,123 | | | $ | 1,123 | | | $ | 1,123 | | | $ | 4,215 | |
Licenses and permits | 764 | | | 101 | | | 86 | | | 86 | | | 86 | | | 86 | | | 319 | |
Developed technology | 2,299 | | | 613 | | | 613 | | | 613 | | | 460 | | | — | | | — | |
Total future amortization expense | $ | 12,893 | | | $ | 1,837 | | | $ | 1,822 | | | $ | 1,822 | | | $ | 1,669 | | | $ | 1,209 | | | $ | 4,534 | |
NOTE 11 - MINERAL PROPERTIES IN THE UNITED STATES
The principal assets of PEVM are an undivided interest in 48 patented and 5 unpatented mining claims totaling approximately 1,500 acres in southeast Nevada. The properties held by PEVM have not been commercially operated for approximately 35 years. In November 2019, PEVM entered into a sales contract which, upon completion of due diligence, may lead to liquidation of substantially all of its remaining assets. Upon closing of the sale, PEVM will be dissolved. Any proceeds from the sale will be used to repay outstanding indebtedness of PEVM owed to the Company. In accordance with the sales contract, in September 2020, approximately $0.2 million of the deposit became non-refundable. The closing of the sale and receipt of remaining proceeds is expected to be completed in late 2021. The sale of PEVM is not anticipated to have a material impact on the Company's Consolidated Financial Statements.
NOTE 12 – ACCRUED LIABILITIES
| | | | | | | | | | | |
Accrued liabilities at December 31 are summarized as follows: | | | |
| 2020 | | 2019 |
| (thousands of dollars) |
Accrued state taxes | $ | 125 | | | $ | — | |
Accrued payroll | 2,282 | | | 1,250 | |
Accrued royalties | 260 | | 273 |
Accrued officer compensation | 1,053 | | | 1,687 | |
Accrued professional expenses | 559 | | | 1,000 | |
Accrued foreign taxes | 1,054 | | | — | |
Other liabilities | 1,524 | | | 1,532 | |
Total | $ | 6,857 | | | $ | 5,742 | |
NOTE 13 - LONG-TERM DEBT AND LONG-TERM OBLIGATIONS
Senior Secured Credit Facilities
As of December 31, 2020, the Company had (i) no outstanding borrowings under the senior secured revolving credit facility (the “Revolving Facility”) and (ii) approximately $46.6 million in borrowings outstanding under the senior secured term loan facility (the “Term Loan Facility” and, together with the Revolving Facility, the “Credit Facilities”), in each case, provided by the amended and restated credit agreement, dated as of October 1, 2014 (as amended, the “ARC Agreement”), entered into by TOCCO, SHR, GSPL and TC (SHR, GSPL and TC collectively the “Guarantors”). As of December 31, 2020, the Company had approximately $52.4 million of availability under our Revolving Facility (which has aggregate commitments of $75.0 million under the ARC Agreement). TOCCO’s ability to make additional borrowings under the Revolving Facility at December 31, 2020 was limited by, and in the future may be limited by, the Company’s obligation to maintain compliance with the covenants contained in the ARC Agreement (including maintenance of a maximum Consolidated Leverage Ratio and minimum Consolidated Fixed Charge Coverage Ratio (each as defined in the ARC Agreement)).
The maturity date for the ARC Agreement is July 31, 2023. Subject to the lenders acceptance of any increased commitment and other conditions, TOCCO has the option, at any time, to request an increase to the commitment under the Revolving Facility and/or the Term Loan Facility by an additional amount of up to $50.0 million in the aggregate.
Borrowings under each of the Credit Facilities bear interest on the outstanding principal amount at a rate equal to LIBOR plus an applicable margin of 1.25% to 2.50% or, at our option, the Base Rate plus an applicable margin of 0.25% to 1.50%, in each case, with the applicable margin being determined based on the Consolidated Leverage Ratio of TOCCO. A commitment fee between 0.20% and 0.375% is also payable quarterly on the unused portion of the Revolving Facility. As of December 31, 2020, the year to date effective interest rate for the Credit Facilities was 2.63%. Borrowings under the Term Loan Facility are subject to quarterly amortization payments based on a commercial style amortization method over a twenty year period; provided, that the final principal installment will be paid on the maturity date and will be in an amount equal to the outstanding borrowings under the Term Loan Facility on such date.
On May 8, 2020, TOCCO and the Guarantors entered into a Seventh Amendment to the ARC Agreement. Pursuant to the Seventh Amendment, certain amendments were made to the terms of the ARC Agreement, including, among other things, to (a) permit the incurrence of additional indebtedness in the form of loans (the “PPP Loans”) under the United States Small Business Administration Paycheck Protection Program (the “PPP”) and (b) exclude the PPP Loans from the calculation of the Consolidated Leverage Ratio until such time that any portion of the PPP Loans are not forgiven in accordance with the Coronavirus Aid, Relief, and Economic Security Act (the “CARES Act”).
As of the end of each fiscal quarter, TOCCO must maintain a maximum Consolidated Leverage Ratio of 3.50 to 1.00 (subject to temporary increase following certain acquisitions). TOCCO’s Consolidated Leverage Ratio was 1.65 and 2.20 as of December 31, 2020 and December 31, 2019, respectively. Additionally, TOCCO must maintain a minimum Consolidated Fixed Charge Coverage Ratio as of the end of any fiscal quarter of 1.15 to 1.00. TOCCO’s Consolidated Fixed Charge Coverage Ratio was 1.80 and 2.56 as of December 31, 2020 and December 31, 2019, respectively. As noted above, the Consolidated Leverage Ratio specifically excludes the PPP Loans until such time that any portion of the PPP Loans are not forgiven in accordance with the CARES Act. The Company used a portion of the approximately $60 million in net proceeds from the Share Sale, discussed in Note 6, to prepay outstanding borrowings of $30 million under the Term Loan Facility of the Company’s ARC Agreement in September 2020.
The ARC Agreement contains a number of customary affirmative and negative covenants and the Company was in compliance with those covenants as of December 31, 2020.
Debt Issuance Costs
Debt issuance costs of approximately $0.9 million were incurred in connection with the fourth amendment to the ARC Agreement and the remaining debt issuance costs of $0.3 million from the previous agreements were expensed and are shown as a loss on the extinguishment of debt on the consolidated statements of operations for the year ended December 31, 2018. Unamortized debt issuance costs of approximately $0.5 million and $0.6 million for the years ended December 31, 2020 and December 31, 2019, have been netted against outstanding loan balances.
| | | | | | | | | | | |
Long-term debt and long-term obligations at December 31 are summarized as follows: | | | |
| 2020 | | 2019 |
| (thousands of dollars) |
Revolving facility | $ | — | | | $ | 3,000 | |
Term loan facility | 46,563 | | | 80,938 | |
| | | |
Loan fees | (468) | | | (649) | |
| | | |
Total long-term debt | 46,095 | | | 83,289 | |
| | | |
Less current portion including loan fees | 4,194 | | | 4,194 | |
| | | |
Total long-term debt, less current portion including loan fees | $ | 41,901 | | | $ | 79,095 | |
PPP Loans
On May 6, 2020, SHR and TC (collectively, the “Borrowers”) received loan proceeds from the PPP Loans in an aggregate principal amount of approximately $6.1 million under the PPP. The PPP Loans are evidenced by unsecured promissory notes each payable to Bank of America, N.A. The Borrowers fully utilized the PPP Loans to cover payroll and benefits costs in accordance with the relevant terms and conditions of the CARES Act. The PPP Loans mature on May 6, 2022, and bear interest at a stated rate of 1.0% per annum. The Company is pursuing and expects to receive full forgiveness of the PPP Loans in accordance with the provisions of the CARES Act.
NOTE 14 - COMMITMENTS AND CONTINGENCIES
Litigation
The Company is periodically named in legal actions arising from normal business activities. We evaluate the merits of these actions and, if we determine that an unfavorable outcome is probable and can be reasonably estimated, we will establish the necessary reserves. We are not currently involved in legal proceedings that could reasonably be expected to have a material adverse effect on our business, prospects, financial condition or results of operations. We may become involved in material legal proceedings in the future.
Supplier Agreements
In accordance with our supplier agreements, on a recurring monthly basis, the Company commits to purchasing a determined volume of feedstock in anticipation of upcoming requirements. Feedstock purchases are invoiced and recorded when they are delivered. As of December 31, 2020 and 2019, the value of the remaining undelivered feedstock approximated $9.2 million and $12.4 million, respectively.
From time to time, we may incur shortfall fees due to feedstock purchases being below the minimum amounts as prescribed by our agreements with our suppliers. The shortfall fee expenses were $1.1 million, $0.6 million and $0.5 million for the years ended December 31, 2020, 2019, and 2018.
Environmental Remediation
Amounts charged to expense for various activities related to environmental monitoring, compliance, and improvements were approximately $0.9 million in 2020, $0.9 million in 2019 and $0.7 million in 2018.
NOTE 15 - SHARE-BASED COMPENSATION
The Stock Option Plan for Key Employees, as well as, the Non-Employee Director Stock Option Plan (hereinafter collectively referred to as the “Stock Option Plans”), were approved by the Company’s shareholders in July 2008. The Stock Option Plans allot for the issuance of up to 1,000,000 shares.
The Trecora Resources Stock and Incentive Plan (the “Plan”) was approved by the Company’s shareholders in June 2012. The Plan allows for the issuance of up to 2,500,000 shares in the form of stock options or restricted stock unit awards.
Share-based compensation of approximately $1.9 million, $1.3 million, and $1.8 million was recognized in 2020, 2019, and 2018, respectively. The Company reclassified approximately $0.3 million and $0.3 million for 2019 and 2018, respectively, from share-based compensation expense in connection with the restructuring described in Note 21.
Stock Options and Warrant Awards
Stock options and warrants granted under the provisions of the Stock Option Plans permit the purchase of our common stock at exercise prices equal to the closing price of Company common stock on the date the options were granted. The options have terms of 10 years and generally vest ratably over terms of 4 to 5 years. There were no stock options or warrant awards issued during 2020, 2019, or 2018. | | | | | | | | | | | | | | | | | | | | | | | |
A summary of the status of the Company’s stock option and warrant awards is as follows: |
| Stock Options and Warrants | | Weighted Average Exercise Price Per Share | | Weighted Average Remaining Contractual Life | | Intrinsic Value (in thousands) |
Outstanding at January 1, 2020 | 487,000 | | | $ | 10.87 | | | | | |
Granted | — | | | — | | | | | |
Expired | — | | | — | | | | | |
Exercised | — | | | — | | | | | |
Forfeited | — | | | — | | | | | |
Outstanding at December 31, 2020 | 487,000 | | | $ | 10.87 | | | 2.8 | | $ | — | |
Expected to vest | — | | | $ | — | | | 0.0 | | $ | — | |
Exercisable at December 31, 2020 | 487,000 | | | $ | 10.87 | | | 2.8 | | $ | — | |
The aggregate intrinsic value of options was calculated as the difference between the exercise price of the underlying awards and the quoted price of our common stock. At December 31, 2020, options to purchase approximately 0.1 million shares of common stock were in-the-money.
Since no options were granted, the weighted average grant-date fair value per share of options granted during the years 2020, 2019, and 2018 was nil. During 2020, 2019, and 2018 the aggregate intrinsic value of options and warrants exercised was approximately nil, $0.1 million and $2.6 million respectively, determined as of the date of option exercise.
The Company received approximately nil, nil and $0.9 million in cash from the exercise of options during 2020, 2019 and 2018, respectively. Of the 85,000 stock options and warrants exercised in 2019, the Company only issued approximately 11,000 shares due to cashless transactions. The tax benefit realized from the exercise in 2019 was insignificant.
As of December 31, 2020, there was no unrecognized compensation costs related to non-vested share-based compensation.
Post-retirement compensation of approximately $0.7 million during the year ended December 31, 2018 was reversed related to options awarded to a former CEO and board member in July 2009. On May 9, 2010, the Board of Directors determined that he had forfeited these options and other retirement benefits when he made various demands against the Company and other AMAK shareholders which would benefit him personally and were not in the best interests of the Company and its shareholders. The Company was successful in litigating its right to withdraw the options and benefits and as such, these options and benefits were reversed during the second quarter of 2018.
Restricted Stock and Restricted Stock Unit Awards
Generally, restricted stock and restricted stock unit awards are granted annually to officers and directors of the Company under the provisions of the Plan. Restricted stock units are also granted ad hoc to attract or retain key personnel, and the terms and conditions under which these restricted stock units vest vary by award. The fair market value of restricted stock units granted is equal to the Company’s closing stock price on the date of grant. Restricted stock units granted generally vest ratably over periods ranging from 1 to 3 years. Certain awards also include vesting provisions based on performance metrics.
Upon vesting, the restricted stock units are settled by issuing one share of Company common stock per unit. | | | | | | | | | | | |
A summary of the status of the Company’s restricted stock units activity is as follows: | | | |
| Shares of Restricted Stock Units | | Weighted Average Grant Date Price per Share |
Outstanding at January 1, 2020 | 298,864 | | | $ | 9.78 | |
Granted | 364,637 | | | 6.32 | |
Forfeited | (15,571) | | | 11.40 | |
Vested | (71,409) | | | 8.40 | |
Outstanding at December 31, 2020 | 576,521 | | | $ | 7.51 | |
Expected to vest | 576,521 | | | |
As of December 31, 2020, there was approximately $1.3 million of unrecognized compensation costs related to non-vested restricted share-based compensation that is expected to be recognized over a weighted average period of 1.1 years.
NOTE 16 – INCOME TAXES
On March 27, 2020, the CARES Act was enacted into law. The CARES Act allows for the deferral of income and social security tax payments, a five–year carryback for net operating losses (“NOLs”), changes to interest expense and business loss limitation rules, certain new tax credits, and certain new loans and grants to businesses. In connection with the CARES Act, we recognized $16.5 million in NOL carryback claims, of which approximately, $14.1 million was received during the fourth quarter of 2020. In connection with this claim, we received interest income of approximately $0.5 million which is included in miscellaneous income (expense). Our final refund claim for approximately $2.4 million is still outstanding and is included in taxes receivable on the consolidated balance sheet.
| | | | | | | | | | | | | | | | | |
The provision (benefit) for income taxes from continuing operations consisted of the following: |
| Year ended December 31, |
| 2020 | | 2019 | | 2018 |
| (thousands of dollars) |
Current federal benefit | $ | (19,190) | | | $ | — | | | $ | (74) | |
Current state expense | 86 | | | 91 | | | 31 | |
| | | | | |
Deferred federal expense (benefit) | 15,140 | | | (3,564) | | | (813) | |
Deferred state expense (benefit) | 1 | | | (93) | | | 210 | |
| | | | | |
Income tax expense (benefit) | $ | (3,963) | | | $ | (3,566) | | | $ | (646) | |
The difference between the year ended effective tax rate in income tax expense (benefit) and the Federal statutory rate of 21% is as follows:
| | | | | | | | | | | | | | | | | |
| 2020 | | 2019 | | 2018 |
| (thousands of dollars) |
Income taxes at U.S. statutory rate | $ | 211 | | | $ | (3,455) | | | $ | (661) | |
State taxes, net of federal benefit | 71 | | | 256 | | | 234 | |
Net operating loss carryback | (4,655) | | | — | | | — | |
Research and development credits | (518) | | | (203) | | | (263) | |
Permanent and other items | 928 | | | (164) | | | 44 | |
| | | | | |
Total tax expense (benefit) | $ | (3,963) | | | $ | (3,566) | | | $ | (646) | |
The significant difference in rate is primarily due to the ability of the Company under the CARES Act to carryback 2018 and 2019 NOLs to a year with a 35% income tax rate. Other permanent differences include the research and development credit, compensation limits, and stock-based compensation.
Tax effects of temporary differences that give rise to significant portions of federal and state deferred tax assets and deferred tax liabilities were as follows:
| | | | | | | | | | | |
| December 31, |
| 2020 | | 2019 |
| (thousands of dollars) |
Deferred tax liabilities: | | | |
Plant, pipeline and equipment | $ | (31,119) | | | $ | (29,227) | |
| | | |
Other assets | (31) | | | (32) | |
Operating lease asset | (2,211) | | | (2,838) | |
Total deferred tax liabilities | $ | (33,361) | | | $ | (32,097) | |
| | | |
Deferred tax assets: | | | |
Net operating loss carryforward | — | | | 11,685 | |
Intangible assets | 3,396 | | | 3,699 | |
Operating lease liability | 2,211 | | | 2,838 | |
Stock-based compensation | 956 | | | 1,093 | |
Investment in AMAK | — | | | 589 | |
Accounts receivable | 65 | | | 240 | |
Mineral interests | 226 | | | 226 | |
Interest expense carryforward | — | | | 211 | |
General business credit | — | | | 140 | |
Inventory | 146 | | | 111 | |
Post-retirement benefits | 70 | | | 71 | |
Charitable contributions | — | | | 45 | |
Gross deferred tax assets | 7,070 | | | 20,948 | |
Valuation allowance | (226) | | | (226) | |
Total net deferred tax assets | $ | 6,844 | | | $ | 20,722 | |
Net deferred tax liabilities | $ | (26,517) | | | $ | (11,375) | |
We provided a valuation allowance in 2020 and 2019 against certain deferred tax assets because of uncertainties regarding their realization. In connection with the sale of AMAK, the Company recorded foreign tax expense, recognized as a foreign tax credit, of approximately $1.3 million (See Note 6) during the year ended December 31, 2020.
We file an income tax return in the U.S. federal jurisdiction and a margin tax return in Texas. We received notification from the Internal Revenue Service (“IRS”) in February 2020 on the selection of our December 31, 2017 tax return for audit. All audit requests are complete and the Company is expecting to receive confirmation of the audit closing without change. In prior years, we received notification that Texas selected our R&D credit calculations for 2014 and 2015 for audit. The state of Texas had suspended their examination while they comprehensively reviewed their audit procedures for consistency. During the fourth quarter of 2019, we received notice that Texas had completed their review of their procedures and initiated additional requests for information. The Company has timely responded to all requested information. We do not expect any changes related to the Federal or Texas audits. Our federal and Texas tax returns remain open for examination for the years 2016 through 2020.
We recognized no adjustment for uncertain tax positions. As of December 31, 2020, and 2019, no interest or penalties related to uncertain tax positions had been accrued.
NOTE 17 – SEGMENT INFORMATION
We operate in two business segments: Specialty Petrochemicals and Specialty Waxes. We operate through business segments according to the nature and economic characteristics of our products as well as the manner in which the information is used internally by our key decision maker, who is our Chief Executive Officer. The accounting policies of the reporting segments are the same as those described in Note 2.
Our Specialty Petrochemicals segment includes SHR and GSPL. Our Specialty Waxes segment includes TC. We also separately identify our corporate overhead which includes financing and administrative activities such as legal, accounting, consulting, investor relations, officer and director compensation, corporate insurance, and other administrative costs.
| | | | | | | | | | | | | | | | | | | | | | | |
| Year Ended December 31, 2020 |
| Specialty Petrochemicals | | Specialty Waxes | | Corporate | | Consolidated |
| (in thousands) |
Net revenues | $ | 172,350 | | | $ | 36,276 | | | $ | — | | | $ | 208,626 | |
Operating income (loss) before depreciation and amortization | 26,438 | | | 1,762 | | | (9,114) | | | 19,086 | |
Operating income (loss) | 15,827 | | | (3,760) | | | (9,129) | | | 2,938 | |
Income (loss) from continuing operations before taxes | 13,294 | | | (3,606) | | | (8,685) | | | 1,003 | |
Depreciation and amortization | 10,611 | | | 5,522 | | | 16 | | | 16,149 | |
Capital expenditures | 11,334 | | | 2,017 | | | — | | | 13,351 | |
| | | | | | | | | | | | | | | | | | | | | | | | | | | | | |
| Year Ended December 31, 2020 |
| Specialty Petrochemicals | | Specialty Waxes | | Corporate | | Eliminations | | Consolidated |
| | | (in thousands) |
Intangible assets, net | $ | — | | | $ | 12,893 | | | $ | — | | | $ | — | | | $ | 12,893 | |
Total assets | 298,198 | | | 83,108 | | | 127,260 | | | (191,733) | | | 316,833 | |
| | | | | | | | | | | | | | | | | | | | | | | |
| Year Ended December 31, 2019 |
| Specialty Petrochemicals | | Specialty Waxes | | Corporate | | Consolidated |
| (in thousands) |
Net revenues | $ | 224,311 | | | $ | 34,648 | | | $ | — | | | $ | 258,959 | |
Operating income (loss) before depreciation and amortization | 38,860 | | | (24,333) | | | (9,190) | | | 5,337 | |
Operating income (loss) | 28,304 | | | (29,925) | | | (9,242) | | | (10,863) | |
Income (loss) from continuing operations before taxes | 23,993 | | | (31,164) | | | (9,279) | | | (16,450) | |
Depreciation and amortization | 10,556 | | | 5,593 | | | 52 | | | 16,201 | |
Capital expenditures | 6,955 | | | 3,124 | | | — | | | 10,079 | |
| | | | | | | | | | | | | | | | | | | | | | | | | | | | | |
| Year Ended December 31, 2019 |
| Specialty Petrochemicals | | Specialty Waxes | | Corporate | | Eliminations | | Consolidated |
| | | (in thousands) |
Intangible assets, net | $ | — | | | $ | 14,736 | | | $ | — | | | $ | — | | | $ | 14,736 | |
Total assets | 289,546 | | | 88,245 | | | 90,203 | | | (166,175) | | | 301,819 | |
NOTE 18 - NET INCOME (LOSS) PER COMMON SHARE
| | | | | | | | | | | | | | | | | |
| Year ended December 31, |
| 2020 | | 2019 | | 2018 |
| (thousands of dollars, except per share amounts) |
Net Income per Common Share - Continuing Operations | | | | | |
Net income (loss) from continuing operations | $ | 4,966 | | | $ | (12,884) | | | $ | (1,728) | |
| | | | | |
Basic income (loss) from continuing operations per common share: | | | | | |
Weighted average shares outstanding | 24,802 | | | 24,698 | | | 24,438 | |
Per share amount (dollars) | $ | 0.20 | | | $ | (0.52) | | | $ | (0.07) | |
| | | | | |
Diluted income (loss) from continuing operations per common share: | | | | | |
Weighted average shares outstanding | 25,356 | | | 24,698 | | | 24,438 | |
Per share amount (dollars) | $ | 0.20 | | | $ | (0.52) | | | $ | (0.07) | |
| | | | | |
Weighted average shares-denominator basic computation | 24,802 | | | 24,698 | | | 24,438 | |
Unvested restricted stock unit grant | 554 | | | — | | | — | |
| | | | | |
Weighted average shares, as adjusted denominator diluted computation | 25,356 | | | 24,698 | | | 24,438 | |
| | | | | |
Net Income per Common Share - Discontinued Operations | | | | | |
Net income (loss) from discontinued operations | $ | 26,209 | | | $ | (2,090) | | | $ | (604) | |
| | | | | |
Basic income (loss) from discontinued operations per common share: | | | | | |
Weighted average shares outstanding | 24,802 | | | 24,698 | | | 24,438 | |
Per share amount (dollars) | $ | 1.06 | | | $ | (0.08) | | | $ | (0.02) | |
| | | | | |
Diluted income (loss) from discontinued operations per common share: | | | | | |
Weighted average shares outstanding | 25,356 | | | 24,698 | | | 24,438 | |
Per share amount (dollars) | $ | 1.03 | | | $ | (0.08) | | | $ | (0.02) | |
| | | | | |
Weighted average shares-denominator basic computation | 24,802 | | | 24,698 | | | 24,438 | |
Unvested restricted stock unit grant | 554 | | | — | | | — | |
| | | | | |
Weighted average shares, as adjusted denominator diluted computation | 25,356 | | | 24,698 | | | 24,438 | |
| | | | | |
Net Income per Common Share | | | | | |
Net income (loss) | $ | 31,175 | | | $ | (14,974) | | | $ | (2,332) | |
| | | | | |
Basic income (loss) per common share: | | | | | |
Weighted average shares outstanding | 24,802 | | | 24,698 | | | 24,438 | |
Per share amount (dollars) | $ | 1.26 | | | $ | (0.61) | | | $ | (0.10) | |
| | | | | |
Diluted income (loss) per common share: | | | | | |
Weighted average shares outstanding | 25,356 | | | 24,698 | | | 24,438 | |
Per share amount (dollars) | $ | 1.23 | | | $ | (0.61) | | | $ | (0.10) | |
| | | | | |
Weighted average shares-denominator basic computation | 24,802 | | | 24,698 | | | 24,438 | |
Unvested restricted stock unit grant | 554 | | | — | | | — | |
Effect of dilutive stock options | — | | | — | | | — | |
Weighted average shares, as adjusted denominator diluted computation | 25,356 | | | 24,698 | | | 24,438 | |
At December 31, 2020, 2019, and 2018, 0.5 million, 0.5 million and 0.7 million potential common stock shares, respectively, were issuable upon the exercise of options and warrants. At December 31, 2020, the Company had 0.5 million stock options that were not included in the computation of diluted earnings per share because such options would be anti-dilutive.
NOTE 19 - QUARTERLY RESULTS OF OPERATIONS (UNAUDITED)
The quarterly results of operations shown below are derived from unaudited financial statements for the eight quarters ended December 31, 2020 (in thousands, except per share data, rounding may apply):
| | | | | | | | | | | | | | | | | | | | | | | | | | | | | |
| Year Ended December 31, 2020 |
| First Quarter | | Second Quarter | | Third Quarter | | Fourth Quarter | | Total |
| | | | | | | | | |
Revenues | $ | 62,067 | | | $ | 40,674 | | | $ | 47,747 | | | $ | 58,138 | | | $ | 208,626 | |
Gross profit | 8,078 | | | 6,167 | | | 8,457 | | | 5,976 | | | 28,678 | |
| | | | | | | | | |
Net income (loss) from continuing operations | $ | 5,863 | | | $ | (1,859) | | | $ | 1,108 | | | $ | (146) | | | $ | 4,966 | |
Net income (loss) from discontinued operations, net of tax | 4,857 | | | (2) | | | 21,324 | | | 30 | | | 26,209 | |
Net income (loss) | 10,720 | | | (1,861) | | | 22,432 | | | (116) | | | 31,175 | |
| | | | | | | | | |
Basic EPS (1) from continuing operations | $ | 0.24 | | | $ | (0.07) | | | $ | 0.04 | | | $ | (0.01) | | | $ | 0.20 | |
Basic EPS (1) from discontinued operations | 0.20 | | | — | | | 0.86 | | | — | | | 1.06 | |
Basic EPS (1) | 0.44 | | | (0.07) | | | 0.90 | | | (0.01) | | | 1.26 | |
| | | | | | | | | |
Diluted EPS (1) from continuing operations | $ | 0.23 | | | $ | (0.07) | | | $ | 0.04 | | | $ | (0.01) | | | $ | 0.20 | |
Diluted EPS (1) from discontinued operations | 0.19 | | | — | | | 0.84 | | | — | | | 1.03 | |
Diluted EPS (1) | 0.42 | | | (0.07) | | | 0.88 | | | (0.01) | | | 1.23 | |
| | | | | | | | | | | | | | | | | | | | | | | | | | | | | |
| Year Ended December 31, 2019 |
| First Quarter | | Second Quarter | | Third Quarter | | Fourth Quarter | | Total |
| | | | | | | | | |
Revenues | $ | 65,155 | | | $ | 69,371 | | | $ | 62,715 | | | $ | 61,718 | | | $ | 258,959 | |
Gross profit | 10,073 | | | 10,565 | | | 9,567 | | | 8,310 | | | 38,515 | |
| | | | | | | | | |
Net income (loss) from continuing operations | $ | 1,797 | | | $ | 2,476 | | | $ | 1,583 | | | $ | (18,740) | | | $ | (12,884) | |
Net income (loss) from discontinued operations, net of tax | (46) | | | (72) | | | (1,002) | | | (970) | | | (2,090) | |
Net income (loss) | 1,751 | | | 2,404 | | | 581 | | | (19,710) | | | (14,974) | |
| | | | | | | | | |
Basic EPS (1) from continuing operations | $ | 0.07 | | | $ | 0.10 | | | $ | 0.06 | | | $ | (0.76) | | | $ | (0.52) | |
Basic EPS (1) from discontinued operations | — | | | — | | | (0.04) | | | (0.04) | | | (0.08) | |
Basic EPS (1) | 0.07 | | | 0.10 | | | 0.02 | | | (0.80) | | | (0.61) | |
| | | | | | | | | |
Diluted EPS (1) from continuing operations | $ | 0.07 | | | $ | 0.10 | | | $ | 0.06 | | | $ | (0.76) | | | $ | (0.52) | |
Diluted EPS (1) from discontinued operations | — | | | — | | | (0.04) | | | (0.04) | | | (0.08) | |
Diluted EPS (1) | 0.07 | | | 0.10 | | | 0.02 | | | (0.80) | | | (0.61) | |
(1)Basic and diluted earnings per share are computed independently for each of the quarters presented based on the weighted average number of common shares outstanding during that period. Therefore, the sum of quarterly basic and diluted per share information may not equal annual basic and diluted earnings per share.
NOTE 20 – RELATED PARTY TRANSACTIONS
In November 2020, Company Director Adam C. Peakes joined Merichem Company as Executive Vice President and Chief Financial Officer. The Company incurred expenses of less than $0.1 million during each of the years ended December 31, 2020, 2019, and 2018, respectively, for Merichem Company. At December 31, 2020 and 2019, we had outstanding liabilities payable to Merichem Company of less than $0.1 million and nil, respectively.
Consulting fees of approximately nil , $0.1 million and $0.1 million were incurred during 2020, 2019, and 2018, respectively, from Nicholas Carter, Director and former CEO. Due to his history and experience with the Company and to provide continuity after his retirement, a consulting agreement was entered into with Mr. Carter in July 2015, which terminated effective December 31, 2019.
NOTE 21 – RESTRUCTURING AND SEVERANCE EXPENSES
During 2018, the Company incurred restructuring and severance expenses of approximately $2.3 million related to changes in executive management and the completion of significant capital projects in our specialty petrochemicals segment. These expenses related to severance, stock compensation for continued vesting of time-vested shares issued under the Company’s long-term incentive plans, and certain employee benefits including medical insurance and vacation. As of December 31, 2020, there was no remaining unpaid or accrued restructuring or severance expenses. As of December 31, 2019, approximately $0.02 million remained unpaid and was included in accrued liabilities.
NOTE 22 – POST-RETIREMENT OBLIGATIONS
In July 2015 and June 2018, we entered into retirement agreements with our former CEO, Nicholas Carter, and our former VP of Accounting & Compliance, Connie Cook. Mr. Carter’s agreement provides continued welfare benefits for him and his wife for life at the same cost sharing basis as regular employees. Ms. Cook’s agreement provides continued welfare benefits for her and her husband until eligible for Medicare. Approximately $0.3 million and $0.3 million was outstanding at December 31, 2020, and 2019, respectively, and included in post-retirement benefits. For the period ended December 31, 2020, and 2019, approximately $0.01 million and $0.02 million, respectively, had been paid.
TRECORA RESOURCES AND SUBSIDIARIES
VALUATION AND QUALIFYING ACCOUNTS
Three years ended December 31, 2020
| | | | | | | | | | | | | | | | | | | | | | | | | | |
Description | | Beginning balance | | Charged (credited) to earnings | | Deductions | | Ending balance |
ALLOWANCE FOR DEFERRED TAX ASSET | | | | | | | | |
| | | | | | | | |
December 31, 2018 | | 225,622 | | | — | | | — | | | 225,622 | |
December 31, 2019 | | 225,622 | | | — | | | — | | | 225,622 | |
December 31, 2020 | | 225,622 | | | — | | | — | | | 225,622 | |
| | | | | | | | | | | | | | | | | | | | | | | | | | |
Description | | Beginning balance | | Charged to earnings | | Deductions | | Ending balance |
ALLOWANCE FOR DOUBTFUL ACCOUNTS | | | | | | | | |
| | | | | | | | |
December 31, 2018 | | 300,000 | | | 152,000 | | | — | | | 452,000 | |
December 31, 2019 | | 452,000 | | | (23,000) | | | — | | | 429,000 | |
December 31, 2020 | | 429,000 | | | — | | | (129,000) | | | 300,000 | |
AL MASANE AL KOBRA MINING COMPANY
Financial Statements
with
Report of Independent Registered Public Accounting Firm
For the nine months ended September 30, 2020
and years ended
December 31, 2019 and 2018
AL MASANE AL KOBRA MINING COMPANY
Table of Contents
______________________________________________________________________________________________________
REPORT OF INDEPENDENT REGISTERED PUBLIC ACCOUNTING FIRM
To the Board of Directors and
Shareholders of Al Masane Al Kobra Mining Company
Najran, Kingdom of Saudi Arabia
Opinion on the Financial Statements
We have audited the accompanying balance sheets of Al Masane Al Kobra Mining Company (the “Company”) as of September 30, 2020 and December 31, 2019, and the related statements of operations, changes in shareholders’ equity, and cash flows for the nine months ended September 30, 2020 and each of the years ended December 31, 2019 and 2018, and the related notes (collectively referred to as the “Financial Statements”). In our opinion, the Financial Statements present fairly, in all material respects, the financial position of the Company as of September 30, 2020 and December 31, 2019, and the results of its operations and its cash flows for the nine months ended September 30, 2020 and each of the years ended December 31, 2019 and 2018, in conformity with accounting principles generally accepted in the United States of America.
Basis for Opinion
These Financial Statements are the responsibility of the Company’s management. Our responsibility is to express an opinion on the Company’s Financial Statements based on our audits. We are a public accounting firm registered with the Public Company Accounting Oversight Board (United States) (“PCAOB”) and are required to be independent with respect to the Company in accordance with the U.S. federal securities laws and the applicable rules and regulations of the Securities and Exchange Commission and the PCAOB.
We conducted our audits in accordance with the standards of the PCAOB. Those standards require that we plan and perform the audit to obtain reasonable assurance about whether the Financial Statements are free of material misstatement, whether due to error or fraud. The Company is not required to have, nor were we engaged to perform, an audit of its internal control over financial reporting. As part of our audits, we are required to obtain an understanding of internal control over financial reporting, but not for the purpose of expressing an opinion on the effectiveness of the Company’s internal control over financial reporting. Accordingly, we express no such opinion.
Our audits included performing procedures to assess the risks of material misstatement of the Financial Statements, whether due to error or fraud, and performing procedures that respond to those risks. Such procedures included examining, on a test basis, evidence regarding the amounts and disclosures in the Financial Statements. Our audits also included evaluating the accounting principles used and significant estimates made by management, as well as evaluating the overall presentation of the Financial Statements. We believe that our audits provide a reasonable basis for our opinion.
/s/ Mamdouh Al Majed & Faisal Al-Enzi
Certified Public Accountants
We have served as the Company’s auditor since 2013.
Riyadh, Kingdom of Saudi Arabia
March 4, 2021
AL MASANE AL KOBRA MINING COMPANY
Balance Sheets
| | | | | | | | | | | |
| September 30, | | December 31, |
| 2020 | | 2019 |
| (Expressed in Saudi Riyals) |
ASSETS | | | |
Current assets: | | | |
Cash and cash equivalents | 29,452,821 | | | 52,244,794 | |
Restricted cash (Note 1) | 7,935,905 | | | — | |
Accounts receivable, net | 8,688,925 | | | 29,643,472 | |
Inventories | 45,017,824 | | | 35,277,340 | |
Advances to shareholders (Note 1) | — | | | 2,859,341 | |
Advances to contractors and other | 20,650,315 | | | 50,053,018 | |
| | | |
Total current assets | 111,745,790 | | | 170,077,965 | |
| | | |
Non-current assets: | | | |
Property and equipment, net | 683,014,705 | | | 610,634,432 | |
Development costs, net | 98,939,725 | | | 121,267,664 | |
Deferred mine closure costs | 4,849,249 | | | 5,211,505 | |
| | | |
Total non-current assets | 786,803,679 | | | 737,113,601 | |
| | | |
| 898,549,469 | | | 907,191,566 | |
| | | |
LIABILITIES AND SHAREHOLDERS' EQUITY | | | |
Current liabilities: | | | |
Accounts payable and accrued liabilities | 38,499,280 | | | 40,418,619 | |
Zakat and income tax liability | 14,966,681 | | | 10,932,026 | |
| | | |
Capital lease obligation, current portion | 2,479,480 | | | 2,318,301 | |
Long-term debt, current portion | 97,500,000 | | | 50,000,000 | |
| | | |
Total current liabilities | 153,445,441 | | | 103,668,946 | |
| | | |
Non-current liabilities | | | |
Provision for mine closure costs | 17,030,905 | | | 16,625,347 | |
Capital lease obligation, net of current portion | 2,022,518 | | | 3,898,002 | |
Long-term debt, net of current portion and | | | |
deferred finance costs | 271,626,947 | | | 267,933,847 | |
End-of-service indemnities | 6,029,921 | | | 4,880,892 | |
Deferred income taxes | — | | | 4,217,658 | |
| | | |
Total non-current liabilities | 296,710,291 | | | 297,555,746 | |
See accompanying notes to financial statements.
AL MASANE AL KOBRA MINING COMPANY
Balance Sheets - (Continued)
| | | | | | | | | | | |
| September 30, | | December 31, |
| 2020 | | 2019 |
| (Expressed in Saudi Riyals) |
Commitments and contingencies (Note 14) | | | |
| | | |
Shareholders' equity | | | |
Share capital | 820,000,000 | | | 820,000,000 | |
Share premium | (131,808,900) | | | (74,713,350) | |
Accumulated deficit | (239,797,363) | | | (239,319,776) | |
| | | |
Total shareholders' equity | 448,393,737 | | | 505,966,874 | |
| | | |
| 898,549,469 | | | 907,191,566 | |
See accompanying notes to financial statements.
AL MASANE AL KOBRA MINING COMPANY
Statements of Operations
For the nine months ended September 30, 2020 and
years ended December 31, 2019 and 2018
| | | | | | | | | | | | | | | | | |
| 2020 | | 2019 | | 2018 |
| (Expressed in Saudi Riyals) |
Revenues | 234,872,562 | | | 293,811,329 | | | 263,377,273 | |
| | | | | |
Costs of revenues | 208,980,004 | | | 279,645,705 | | | 255,313,296 | |
| | | | | |
Operating income | 25,892,558 | | | 14,165,624 | | | 8,063,977 | |
| | | | | |
General and administrative expenses | 18,693,047 | | | 30,355,423 | | | 29,475,998 | |
| | | | | |
Income (loss) from operations | 7,199,511 | | | (16,189,799) | | | (21,412,021) | |
| | | | | |
Other income (expense) | | | | | |
| | | | | |
| | | | | |
Finance charges | (4,539,975) | | | (5,436,532) | | | (5,969,821) | |
Other income (expense) (Note 1) | (1,300,258) | | | 2,091,152 | | | 323,575 | |
| | | | | |
| (5,840,233) | | | (3,345,380) | | | (5,646,246) | |
| | | | | |
Income (loss )before Zakat and income tax | 1,359,278 | | | (19,535,179) | | | (27,058,267) | |
| | | | | |
Zakat and income tax (expense) benefit | (1,836,865) | | | (6,751,156) | | | 1,824,929 | |
| | | | | |
Net loss | (477,587) | | | (26,286,335) | | | (25,233,338) | |
See accompanying notes to financial statements.
AL MASANE AL KOBRA MINING COMPANY
Statements of Changes in Shareholders' Equity
| | | | | | | | | | | | | | | | | | | | | | | | | | | | | |
| (Expressed in Saudi Riyals) |
| | | | | | | Retained | | |
| | | | | | | Earnings | | |
| Share | | Share | | Treasury | | (Accumulated | | |
| Capital | | Premium | | Stock at cost | | Deficit) | | Total |
| | | | | | | | | |
Balance at December 31, 2017 | 780,000,000 | | | 37,546,420 | | | — | | | (187,800,103) | | | 629,746,317 | |
| | | | | | | | | |
Issuance of share premium | — | | | 2,453,580 | | | — | | | — | | | 2,453,580 | |
| | | | | | | | | |
Conversion of share premium to share capital | 40,000,000 | | | (40,000,000) | | | — | | | — | | | — | |
| | | | | | | | | |
Net loss | — | | | — | | | — | | | (25,233,338) | | | (25,233,338) | |
| | | | | | | | | |
Balance at December 31, 2018 | 820,000,000 | | | — | | | — | | | (213,033,441) | | | 606,966,559 | |
| | | | | | | | | |
Share repurchase (Note 1) | — | | | — | | | (74,713,350) | | | — | | | (74,713,350) | |
| | | | | | | | | |
Net loss | — | | | — | | | — | | | (26,286,335) | | | (26,286,335) | |
| | | | | | | | | |
Balance at December 31, 2019 | 820,000,000 | | | — | | | (74,713,350) | | | (239,319,776) | | | 505,966,874 | |
| | | | | | | | | |
Share repurchase (Note 1) | — | | | — | | | (57,095,550) | | | — | | | (57,095,550) | |
| | | | | | | | | |
Net loss | — | | | — | | | — | | | (477,587) | | | (477,587) | |
| | | | | | | | | |
Balance at September 30, 2020 | 820,000,000 | | | — | | | (131,808,900) | | | (239,797,363) | | | 448,393,737 | |
See accompanying notes to financial statements.
AL MASANE AL KOBRA MINING COMPANY
Statements of Cash Flows
For the nine months ended September 30, 2020 and
years ended December 31, 2019 and 2018
| | | | | | | | | | | | | | | | | |
| 2020 | | 2019 | | 2018 |
| (Expressed in Saudi Riyals) |
Cash flows from operating activities: | | | | | |
Net loss | (477,587) | | | (26,286,335) | | | (25,233,338) | |
Adjustments to reconcile net loss to net cash provided by (used in) operating activities: | | | | | |
Depreciation and amortization | 77,148,251 | | | 113,949,259 | | | 125,507,864 | |
Accretion of deferred mine closure costs | 405,558 | | | 562,211 | | | 543,198 | |
Amortization of deferred finance costs | 1,193,100 | | | 1,675,135 | | | 2,175,902 | |
Deferred income taxes | (4,217,658) | | | 424,873 | | | (7,224,929) | |
Forfeiture of non-refundable deposit | 1,429,670 | | | — | | | — | |
Changes in operating assets and liabilities: | | | | | |
Accounts receivable | 20,954,547 | | | (13,408,437) | | | (8,021,219) | |
Inventories | (9,740,484) | | | 10,593,780 | | | (18,644,188) | |
Advances to contractors and other | 29,402,704 | | | (30,884,252) | | | 563,016 | |
Accounts payable and accrued liabilities | (1,919,339) | | | 11,661,674 | | | 6,084,327 | |
Zakat and income tax liability | 4,034,655 | | | 5,532,026 | | | 1,883,327 | |
End-of-service indemnities | 1,149,029 | | | 1,231,003 | | | 1,131,360 | |
| | | | | |
Net cash provided by operating activities | 119,362,446 | | | 75,050,937 | | | 78,765,320 | |
| | | | | |
Cash flows from investing activities: | | | | | |
Additions to property and equipment | (126,838,330) | | | (48,246,282) | | | (28,945,309) | |
| | | | | |
Cash flows from financing activities: | | | | | |
Issuance of share capital and premium | — | | | — | | | 2,453,580 | |
Payments on capital lease obligations | (1,714,305) | | | (1,059,694) | | | (72,788) | |
Repurchase of treasury stock | (55,665,879) | | | (22,151,322) | | | — | |
Borrowings from long-term debt | 50,000,000 | | | 50,000,000 | | | — | |
Payments on long-term debt | — | | | (30,000,000) | | | — | |
Net advances to shareholders | — | | | (2,859,341) | | | (53,015,844) | |
| | | | | |
Net cash used in financing activities | (7,380,184) | | | (6,070,357) | | | (50,635,052) | |
| | | | | |
Increase (decrease) in cash and cash equivalents and restricted cash | (14,856,068) | | | 20,734,298 | | | (815,041) | |
| | | | | |
Cash, cash equivalents and restricted cash, beginning of period | 52,244,794 | | | 31,510,496 | | | 32,325,537 | |
| | | | | |
Cash, cash equivalents and restricted cash, end of period | 37,388,726 | | | 52,244,794 | | | 31,510,496 | |
| | | | | |
Supplemental cash flow information | | | | | |
| | | | | |
Cash paid for interest | 3,346,875 | | | 4,428,545 | | | 3,927,778 | |
| | | | | |
Cash paid for Zakat and income tax | 2,019,868 | | | 6,086,073 | | | 3,212,813 | |
| | | | | |
Supplemental disclosure of non-cash items | | | | | |
| | | | | |
Assets acquired through capital lease obligations | — | | | 7,933,140 | | | 625,805 | |
| | | | | |
Advances to shareholders applied to treasury stock purchase | 1,429,671 | | | 52,562,028 | | | — | |
See accopmanying notes to financial statements.
Note 1 – Organization and Business
Organization
Al Masane Al Kobra Mining Company (us, we, our, AMAK or the Company) is a Saudi Arabian closed joint stock company approved by the Minister of Commerce and Industry Decree Number 247/Q dated 9/10/1428 (October 21, 2007) and registered in Jeddah under Commercial Registration No. 4030175345 on 7/1/1429 (January 16, 2008). During 2015, the head office was moved from Jeddah to Najran. Accordingly, Najran Commercial Registration No. 5950017523 dated 03/11/1431H (October 11, 2010) was modified to be the main Commercial Registration. All amounts are expressed in Saudi Riyals (SR) unless otherwise noted.
During 2009, the authorized capital of the Company was 450,000,000 consisting of 45 million shares of SR10 each of which 50% were issued for cash. The remaining 50% were issued for the contribution of mining rights and assets from Trecora Resources (Trecora) subject to Trecora’s liability for a loan in the amount of 41,250,000 due to the Ministry of Finance and National Economy. The mining rights in Al Masane mine were originally granted by Royal Decree Number M/17 effective 1/12/1413 (May 22, 1993) for a period of thirty years, with a right of renewal for a further period of twenty years to Trecora. The mining rights granted Trecora the right of exploitation in Al Masane mine located in Najran, Saudi Arabia, with an area of 44 square kilometers for a surface rental of 10,000 per square kilometer per year, i.e. 440,000 per year. As per the Ministry of Petroleum and Mineral Resources resolution dated 13/9/1429 (13/9/2008) and the ministry subsequent letter dated 2/1/1430 (30/12/2008), the aforementioned rights were transferred to us.
During 2011, the Company increased its authorized share capital by SR50,000,000 to SR500,000,000 and issued 5,000,000 shares of 10 each at a price of SR28 each resulting in a share premium of SR90,000,000. The entire 5,000,000 shares were issued for cash to Arab Mining Company (ARMICO) headquartered in Amman, Jordan.
During 2013, the Company increased its authorized share capital by SR50,000,000 to SR550,000,000 and issued 5,000,000 shares of 10 each at a price of SR30 each resulting in a share premium of SR100,000,000. The shares were issued for cash to existing shareholders.
During 2015, the Company increased its authorized share capital by SR190,000,000 to SR 740,000,000 and issued 19,000,000 shares of 10 each by transferring from share premium accounts.
During 2016, the Company increased its authorized share capital by SR40,000,000 to SR780,000,000 and issued 4,000,000 shares of 10 each at a price of SR20 each resulting in a share premium of SR35,092,840.
During 2018, the Company increased share premium by SR2,453,580 for shares that were previously issued. In addition, the Company increased its authorized share capital by SR40,000,000 to SR820,000,000 and issued 4,000,000 shares of 10 each by transferring from share premium accounts.
During the Company’s Extraordinary General Assembly Meeting in October of 2018, the shareholders approved to repurchase up to 2,500,000 shares from the shareholders at a price of SR30 each and to register these shares as treasury shares. In December 2018, the Board unanimously approved this proposal and authorized the CEO to proceed with the repurchase. The Company advanced certain shareholders their portion of these proceeds in 2018. During the first quarter of 2019, the Company finalized the transaction and repurchased 2,490,445 shares for approximately SR74,713,000.
On October 2, 2019, the Company and certain shareholders of the Company (collectively, the “Purchasers”) entered into a Share Sale and Purchase Agreement (“Purchase Agreement”) with Trecora to purchase their entire equity interest in the Company for an aggregate gross purchase price of approximately SR264,700,000. The Purchase Agreement contains various representations, warranties and indemnity obligations of the Purchasers and Trecora. As required by the Purchase Agreement, the Purchasers advanced 5% of the purchase price to Trecora as a non-refundable deposit tha twould be applied to the purchase price. The Company’s share of the advance was approximately, SR2,855,000 and was included in advances to shareholders in the accompanying balance sheets as of December 31, 2019.
On January 16, 2020, the Purchasers and Trecora entered into an amendment to extend the close date to March 31, 2020 to allow additional time for the parties to obtain certain required governmental approvals. On March 26, 2020, the Company entered into a second amendment that the Purchasers would complete the purchase of their portion of the shares in multiple closings. Purchasers that completed their portion of the sale after March 31, 2020 but on or before September 28, 2020, would forfeit an amount equal to 50% of their non-refundable deposit as liquidated damages and would not be applied to the purchase price at closing. On April 1, 2020, the Company forfeited SR1,429,726 of their non-refundable deposit and is included in other income (expense) on the accompanying statement of operations.
On August 10, 2020, the Company closed their portion of the Purchase Agreement and purchased 5,709,555 shares from Trecora for SR57,095,550. The Company has recorded these shares as treasury stock. On September 24, 2020, the remaining
Purchasers purchased Trecora’s remaining outstanding shares. In connection with the completion of the Purchase Agreement, the Company entered into an agreement with Trecora whereby the Company agreed to withhold approximately SR7,878,000 of the purchase price to pay Trecora’s capital gain tax obligations. These amounts have been shown as restricted cash and the liability is included in Zakat and income tax liabilities on the accompanying balance sheet as of September 30, 2020.
| | | | | | | | | | | |
As of September 30, 2020, our ownership is as follows: |
| Shares | | Ownership Percentage |
Saudi shareholders | 53,936,081 | | | 73.1 | |
| | | |
ARMICO (Pan Arab Organization) | 19,502,500 | | | 26.4 | |
| | | |
Other | 361,419 | | | 0.5 | |
| | | |
| 73,800,000 | | | 100.0 | |
Business and operations
Our principal activity is to produce zinc and copper concentrates and silver and gold doré as per the license Number 993/2 dated 16/7/1428 (July 31, 2007) issued by Saudi Arabian General Investment Authority (SAGIA). We commenced our commercial production on July 1, 2012. During 2015, we received a new mining lease for an area near our current mining area for the Guyan ancient mine. Over the years, we have performed renovations and maintenance to improve recoveries overall and upgrade the precious metals circuit through the installation of SART (sulfidization, acidification, recycling, and thickening) modifications which are expected to lower chemical use, thereby reducing operating costs. During 2020 we completed an analysis of our mineral reserve estimates and extended the life of the mine and have made capital investments in the Guyan mining area.
Note 2 - Summary of Significant Accounting Policies
The accompanying financial statements have been prepared using U.S. generally accepted accounting principles. The following is a summary of our significant accounting policies:
Cash and cash equivalents
We consider all highly-liquid investments purchased with an original maturity of three months or less to be cash equivalents.
Restricted cash
Restricted cash consists of amounts withheld from non-Saudi shareholders related to the Purchase Agreement for amount sdue to the General Authority of Zakat and Tax (GAZT) in the Kindom of Saudi Arabia for capital gains and income taxes.
Accounts receivable
We evaluate the collectability of our accounts receivable and the adequacy of the allowance for doubtful accounts based upon historical experience and any specific customer financial difficulties of which the Company becomes aware. During the nine months ended September 30, 2020 and years ended December 31, 2019 and 2018, we sold our concentrates and doré pursuant to sales contracts with primarily one customer. No amounts have been written off for the nine months ended September 30, 2020 and the years ended December 31, 2019 and 2018. In addition, we determined that an allowance for doubtful accounts was not necessary at September 30, 2020 and December 31, 2019.
Inventories
The components of inventories include mill stockpiles, precious metal doré, chemicals, and mining supplies. Inventories are stated at the lower of weighted-average cost or market. Costs of mill stockpiles inventory include labor and benefits, supplies, energy, depreciation, depletion, amortization, and other necessary costs incurred with the extraction and processing of ore. Corporate general and administrative costs are not included in inventory costs.
Because it is generally impracticable to determine the minerals contained in mill stockpiles by physical count, reasonable estimation methods are employed. The quantity of material delivered to the mill stockpiles is based on surveyed volumes of mined material and daily production records. Expected mineral recovery rates from the mill stockpiles are determined by various metallurgical testing methods.
Property and equipment
Property and equipment is carried at cost less accumulated depreciation. Expenditures for replacements and improvements are capitalized. Costs related to periodic maintenance are expensed as incurred. Depletion of the mining assets is determined using the unit-of-production method based on total estimated proven and probable reserves. Depletion and amortization using the
unit-of-production method is recorded upon extraction of the ore, at which time it is allocated to inventory cost and then included as a component of cost of goods sold. Other assets are depreciated on a straight-line basis over their estimated useful lives ranging from 3 to 20 years.
Borrowing costs that are directly attributable to the acquisition, construction or production of assets are capitalized as part of the cost of those assets. Assets under construction are capitalized in the construction in progress account. Upon completion, the cost of the related asset is transferred to the appropriate category of property and equipment.
Development costs
Mineral exploration costs, as well as drilling and other costs incurred for the purpose of converting mineral resources to proven and probable reserves or identifying new mineral resources are charged to expense as incurred. Development costs are capitalized beginning after proven and probable reserves have been established. Development costs include costs incurred in mine pre-production activities undertaken to gain access to proven and probable reserves, including shafts, drifts, ramps, permanent excavations, infrastructure and removal of overburden. These costs are deferred net of the proceeds from the sale of any production during the development period and then amortized using an estimated unit-of-production method. If a mine is no longer considered economical, the accumulated costs are charged to the statement of operations in the year in which the determination is made.
Asset impairment
We review and evaluate our long-lived assets for impairment when events or changes in circumstances indicate that the carrying amounts may not be recoverable. Long-lived assets are evaluated for impairment under the two-step model. When events or circumstance suggest impairment of long-lived assets, estimated undiscounted future net cash flows are calculated using future estimated commodity prices, proven and probable reserves, and estimated net proceeds from the disposition of assets on retirement, less operating, sustaining capital, and reclamation costs. If it is determined that an impairment exists, an impairment loss is measured as the amount by which the asset carrying value exceeds its fair value. Fair value is generally determined using valuation techniques such as estimated future cash flows. Because the cash flows used to assess recoverability of our long-lived assets and measure fair value of our mining operations require us to make several estimates and assumptions that are subject to risk and uncertainty, changes in these estimates and assumptions could result in the impairment of our long-lived asset values.
Based on our evaluation, we recorded no impairment losses during the nine months ended September 30, 2020 and the years ended December 31, 2019 and 2018.
End-of-service indemnities
Employee end-of-service benefits are accrued for the benefit of employees under the terms and conditions of Saudi Labor Law and Regulations and their employment contracts. End-of-service indemnities are provided for and accrued in the financial statements based on the respective employees' salaries and length of service.
Foreign currency
Our functional currency is the Saudi Riyal (SR). In June 1986, the Saudi Riyal was officially pegged to the U.S. Dollar at a fixed exchange rate of 1 U.S. Dollar to 3.75 riyals. Foreign currency transactions are translated into Saudi Riyals at the rates of exchange prevailing at the time of the transactions. Monetary assets and liabilities denominated in foreign currencies at the balance sheet date are translated at the exchange rates prevailing at that date. Any gains and losses from settlement and translation of foreign currency transactions are included in the statement of operations. There were no material foreign-currency exchange gains or losses or translation adjustments during the nine months ended September 30, 2020 and the years ended December 31, 2019 and 2018.
Leasing arrangements
We periodically lease operating equipment, facilities, and office buildings. Rentals payable under operating leases are charged to the statements of operations on a straight-line basis over the term of the relevant lease. For any capital leases, the present value of future minimum lease payments at the inception of the lease is reflected as an asset and a liability in the balance sheet. Amounts due within one year are classified as short-term liabilities and the remaining balance as long-term liabilities. Finance charges are charged to the statement of operations.
Operating lease expense amounted to approximately SR2,531,000, SR4,015,000 and SR1,619,000 for the nine months ended September 30, 2020 and the years ended December 31, 2019 and 2018, respectively.
Environmental costs
Environmental costs are expensed or capitalized, depending upon their future economic benefits. Accruals for such expenditures are recorded when it is probable that obligations have been incurred and the costs can reasonably be estimated.
Ongoing compliance costs are expensed as incurred.
Asset retirement obligations and costs
We record the fair value of our estimated asset retirement obligations (ARO) associated with tangible long-lived assets in the period in which the obligation is incurred. ARO associated with long-lived assets are those for which there is a legal obligation to settle under various laws, statues, or regulations. These obligations, which are initially estimated based on discounted cash flow estimates, are accreted to full value over time through charges to cost of revenues. In addition, asset retirement costs (ARCs) are capitalized as part of the related asset’s carrying value and are depreciated (primarily on a unit-of-production basis) over the asset’s respective useful life.
Our ARO consist primarily of costs associated with mine reclamation and closure activities and are included in deferred mine closure costs on the accompanying balance sheets. At least annually, we review our ARO estimates for changes in the projected timing and changes in cost estimates and additional ARO incurred during the period.
Zakat and income tax
We are subject to the Regulations of GAZT in the Kingdom of Saudi Arabia. Under these regulations, Zakat is payable at 2.5% on the basis of the portion of our Zakat base attributable to our Saudi stockholders, and income tax is payable at 20% on the portion of our taxable income attributable to our non-Saudi stockholders. Zakat and income tax are provided on an accrual basis. Any difference in the estimate is recorded when the final assessment is approved, at which time the provision is cleared.
We account for deferred income taxes on non-Saudi owners utilizing an asset and liability method, whereby deferred tax assets and liabilities are recognized based on the tax effects of temporary differences between the financial statements and the income tax basis of assets and liabilities, as measured by the effective tax rate. When appropriate, we evaluate the need for a valuation allowance based on a more likely than not threshold to reduce deferred tax assets to estimated recoverable amounts.
We account for uncertain income tax positions using a threshold and measurement attribute for the financial statement recognition and measurement of a tax position taken or expected to be taken in a tax return. We report tax-related interest and penalties as a component of Zakat and income tax expense. We recognized no material adjustment for unrecognized income tax liabilities.
Revenue recognition
The Company’s revenues primary consists of sales of copper and zinc.
We sell our products pursuant to individual sales contracts entered into with a customer who acts as an intermediary and resells our products to end users. The Company considers each sales contract to be a single performance obligation, represented by the delivery of a series of distinct goods that are substantially the same, with the same pattern of transfer to the Company’s customer. The Company concluded this as, based on the nature of its contracts, the customer receives the benefit of mineral sold as it is shipped per the terms of the commercial invoice at each delivery date. In addition, the Company considers that it has a right to consideration from its customers in an amount that corresponds directly to the value transferred to those customers that being the quantity of mineral delivered at the price per unit delivered. Accordingly, the Company recognizes revenue at the amount to which it has the right to invoice (the invoice practical expedient), as it believes that this method is a faithful depiction of the transfer of goods to its customers.
Revenue is recognized when or as the performance obligations are satisfied, when the Company transfers control of the goods and title passes to the customer. Control is transferred generally upon the completion of loading the material as the point of origin. This is the point which the customer obtains legal title to the product as well as the ability to direct the use of and obtain substantially all the remaining benefits of ownership of the assets.
Sales are recorded based on a provisional sales price or a final sales price calculated in accordance with the terms specified in the relevant sales contract. Under the long-established structure of sales agreements prevalent in the industry, the copper and zinc contained in concentrate is generally “provisionally” priced at the time of shipment. The provisional price received at the time of shipment is later adjusted to a “final” price based on quoted monthly average spot prices on the London Metal Exchange (LME) for a specified future month. We record revenues at the time of shipment (when title and risk of loss pass) based on then-current LME prices, and we account for any changes between the sales price recorded at the time of shipment and subsequent changes in the LME prices through the date of final pricing as gains or losses from a derivative embedded in the sales contract (a futures contract initiated at the date of shipment and settled upon the determination of the “final price”) which is bifurcated and separately accounted for at fair value. The host contract is the sale of the metals contained in the concentrates at the then-current LME price as defined in the contract. Mark-to-market price fluctuations recorded through the settlement date are reflected in revenues for sales contracts. Our embedded derivatives at September 30, 2020 and December 31, 2019, were not significant to the financial statements.
Revenues from concentrate sales are recorded net of treatment and refining charges. These allowances are a negotiated term of
each contract. Treatment and refining charges represent payments or price adjustments to smelters and refiners and are either fixed, or in certain cases, vary with the price of metals (referred to as price participation).
Management estimates
The preparation of financial statements in conformity with accounting principles generally accepted in the United States of America requires management to make estimates and assumptions that affect the reported amounts of assets and liabilities and disclosure of contingent assets and liabilities at the date of the financial statements and the reported amounts of revenues and expenses during the reporting periods. The most significant areas requiring the use of management estimates include mineral reserve estimation; useful asset lives for depreciation and amortization; zakat and income taxes; environmental obligations; reclamation and closure costs; estimates of recoverable materials in mill stockpiles; fair value of embedded derivatives; end-of-service indemnities; and asset impairment, including estimates used to derive future cash flows associated with those assets. Actual results could differ from these estimates.
In early 2020, the World Health Organization declared the rapidly spreading coronavirus disease (COVID-19) outbreak a pandemic. This pandemic has resulted in governments worldwide enacting emergency measures to combat the spread of the virus. The Company considered the impact of COVID-19 on the assumptions and estimates used and determined that there were no material adverse impacts on the Company’s results of operations and financial position at September 30, 2020. The Company is not aware of any specific event or circumstance that would require an update to its estimates or judgments or a revision of the carrying value of its assets or liabilities as of the date of issuance of the financial statements. These estimates may change, as new events occur and additional information is obtained.
Recent accounting pronouncements
In February 2016 the FASB issued ASU No. 2016-02, Leases (Topic 842), to increase transparency and comparability among organizations by recognizing all lease transactions (with terms in excess of 12 months) on the balance sheet as a lease liability and a right-of-use asset (as defined). The ASU is effective for fiscal years beginning after December 15, 2020, including interim periods within those fiscal years, with earlier application permitted. Upon adoption, the lessee will apply the new standard retrospectively to all periods presented or retrospectively using a cumulative effect adjustment in the year of adoption. The Company has several lease agreements for which the amendments will require the Company to recognize a lease liability to make lease payments and a right-of-use asset which will represent its right to use the underlying asset for the lease term. As permitted by the amendments, the Company is anticipating electing an accounting policy to not recognize lease assets and lease liabilities for leases with a term of twelve months or less. The Company is currently reviewing the amendments to ensure it is fully compliant by the adoption date and does not expect to early adopt. In addition, the Company will change its current accounting policies to comply with the amendments with such changes as mentioned above.
Reclassifications
Certain reclassifications have been made to the prior periods to conform with the current year presentation.
Subsequent events
We have evaluated events and transactions subsequent to the date of the financial statements for matters requiring recognition or disclosure in the financial statements. The accompanying financial statements consider events through March 4, 2021, the date on which the financial statements were available to be issued.
Note 3 – Liquidity and Capital Resources
As shown in the financial statements, we have incurred three consecutive years of net losses however, the Company has operating income and generated cash provided from operations. In addition, during 2020 we have updated our mineral reserve estimates and extended the life of the mine with the expectation that the life of mine will be extended another two to three years. We believe that our continued operations, additional debt financing discussed in Note 10, and adjusted repayment terms of our outstanding debt will provide us the necessary liquidity and capital resources.
Note 4 – Inventories
| | | | | | | | | | | |
Inventories consisted of the following at:
| | | |
| September 30, | | December 31, |
| 2020 | | 2019 |
Stockpile ore | 15,623,461 | | | 18,657,218 | |
Ore concentrates | 20,557,020 | | | 6,294,948 | |
Precious metal dore | 2,235,799 | | | 4,490,589 | |
Explosives | 484,169 | | | 326,599 | |
Chemicals and other | 6,117,375 | | | 5,507,986 | |
| | | |
| 45,017,824 | | | 35,277,340 | |
Note 5 – Advances to Contractors and Other
| | | | | | | | | | | |
Advances to contractors and other consisted of the following at: | | | |
| September 30, | | December 31, |
| 2020 | | 2019 |
Advances to contractors | 13,668,562 | | | 42,672,136 | |
Prepaid expenses | 2,251,667 | | | 5,185,037 | |
Other miscellaneous advances and receivables | 4,730,086 | | | 2,195,845 | |
| | | |
| 20,650,315 | | | 50,053,018 | |
Note 6 – Property and Equipment
| | | | | | | | | | | |
Property and equipment, net consisted of the following at:
| | | |
| September 30, | | December 31, |
| 2020 | | 2019 |
Buildings | 191,974,662 | | | 191,838,962 | |
Leasehold improvements | 4,051,062 | | | 1,838,317 | |
Heavy equipment | 146,801,861 | | | 136,066,275 | |
Motor vehicles | 22,753,563 | | | 22,467,300 | |
Civil works | 16,288,221 | | | 16,288,221 | |
Tailings dam | 23,900,160 | | | 23,900,160 | |
Plant and machinery | 332,014,825 | | | 326,974,958 | |
Mining assets – rehabilitation costs | 98,894,826 | | | 98,894,826 | |
Mining assets – underground development costs | 409,899,633 | | | 299,224,519 | |
Construction in progress | 3,356,625 | | | 4,789,313 | |
| | | |
| 1,249,935,438 | | | 1,122,282,851 | |
| | | |
Less accumulated depreciation, depletion and amortization | (566,920,733) | | | (511,648,419) | |
| | | |
| 683,014,705 | | | 610,634,432 | |
During 2020 and 2019, additions to Mining Assets - underground development costs relates to capital investments in the Guyan mining area.
Property and equipment serve as collateral for the SIDF loan agreement (see Note 10).
Depreciation, depletion and amortization expense related to property and equipment was approximately, SR55,000,000, SR79,000,000 and SR88,000,000 for the nine months ended September 30, 2020 and the years ended December 31, 2019 and 2018, respectively.
Note 7 – Development Costs
| | | | | | | | | | | |
Development costs, net consisted of the following at: | | | |
| September 30, | | December 31, |
| 2020 | | 2019 |
Cost | 289,973,237 | | | 289,973,237 | |
Accumulated amortization | (191,033,512) | | | (168,705,573) | |
| | | |
| 98,939,725 | | | 121,267,664 | |
Development costs are amortized using the unit of production method upon extraction of the ore. Amortization expenses related to development costs was approximately SR22,328,000, SR34,014,000 and SR36,250,000 for the nine months ended September 30, 2020 and the years ended December 31, 2019 and 2018, respectively.
Note 8 – Accounts Payable and Accrued Liabilities
| | | | | | | | | | | |
Accounts payable and accrued liabilities consisted of the following at: | | | |
| September 30, | | December 31, |
| 2020 | | 2019 |
Accounts payable and accrued liabilities | 33,012,537 | | | 36,571,709 | |
| | | |
Accrued salaries and payroll | 5,486,743 | | | 3,846,910 | |
| | | |
| 38,499,280 | | | 40,418,619 | |
Note 9 – Zakat and Income Tax
We have submitted our Zakat and income tax return for the year ended December 31, 2019 and have obtained our 2019 Zakat certificate. The Zakat base for the Saudi shareholders was positive in 2020, 2019 and 2018 and the corresponding Zakat expense and liability has been recorded. In 2020, 2019 and 2018, there was a taxable profit attributable to our non-Saudi (foreign) shareholders and the current income tax expense and liability has also been recorded, also included in the liability is withholding on non-Saudi shareholders for capital gains taxes in connection with the share repurchase as discussed in Note 1
| | | | | | | | | | | | | | | | | |
The components of Zakat and income tax expense (benefit) for the nine months ended September 30, 2020 and years ended December 31, 2019 and 2018 are as follows: |
| | | | | |
| 2020 | | 2019 | | 2018 |
Deferred income tax expense (benefit) | (3,277,217) | | | 1,737,276 | | | (12,961,569) | |
Change in valuation allowance | (940,440) | | | (1,312,403) | | | 5,736,640 | |
Current Zakat and income tax expense | 6,054,522 | | | 6,326,283 | | | 5,400,000 | |
| | | | | |
Zakat and income tax expense (benefit) | 1,836,865 | | | 6,751,156 | | | (1,824,929) | |
The difference between the effective income tax rate and the statutory rate for non-Saudi shareholders of 20% for the nine months ended September 30, 2020 and the years ended December 31, 2019 and 2018 relates primarily to changes in the valuation allowance and adjustments to estimates in depreciation.
| | | | | | | | | | | |
Tax effects of temporary differences that give rise to significant portions of non-Saudi owners deferred tax assets and deferred tax liabilities were as follows: |
| September 30, | | December 31, |
| 2020 | | 2019 |
Deferred tax assets: | | | |
Loss carryforward | 40,645,080 | | | 41,293,547 | |
Other | 449,302 | | | 799,526 | |
| | | |
| 41,094,382 | | | 42,093,073 | |
Deferred tax liabilities: | | | |
Property and Equipment | (4,509,734) | | | (8,785,642) | |
| | | |
Net deferred tax asset | 36,584,648 | | | 33,307,431 | |
Valuation allowance | (36,584,648) | | | (37,525,089) | |
| | | |
Net deferred tax liability | — | | | (4,217,658) | |
At September 30, 2020 and December 31, 2019, we had tax loss carryforwards totaling approximately SR203,225,000 and SR206,468,000. Tax losses may be carried forward indefinitely subject to certain annual limitations for non-Saudi shareholders. We have provided a valuation allowance in 2020 and 2019 against a portion of our gross deferred tax assets because of uncertainties regarding their realization.
Note 10 - Long-term Debt
Saudi Industrial Development Fund (SIDF)
During 2010, the Company entered into a loan agreement with the SIDF for SR330,000,000 to finish the development of the mine and provide working capital. In May 2020, we amended our agreement with SIDF to adjust the repayment schedule. Payments are due semi-annually starting on May 27, 2021 of approximately SR35,000,000 with a final payment due on April 24, 2024. The loan agreement is collateralized by all the assets of Company and is guaranteed by the shareholders.
Banque Saudi Fransi (BSF)
During 2019, the Company obtained a credit facility from BSF for SR110,518,400. The facility is to be used to finance capital expenditures related to Guyan and provide bridge financing to SIDF.
The agreement bears interest at Saudi Arabian Interbank Offered Rate (SAIBOR) plus 2.5% per annum. In December 2019, the Company received proceeds of SR50,000,000 which will be repaid starting on March 31, 2021 through equal quarterly installments of approximately SR4,167,000 with the final payment due on December 31, 2023. During 2020, the Company received additional proceeds of SR50,000,000 for bridge financing to SIDF. During December 2020, the Company repaid BSF the SR50,000,000 related to the bridge financing to SIDF.
Under the terms of the agreements with SIDF and BSF, we are required to maintain certain financial covenants, among other requirements.
| | | | | | | | | | | |
Long-term debts are summarized as follows at: | | | |
| September 30, | | December 31, |
| 2020 | | 2019 |
SIDF | 275,000,000 | | | 275,000,000 | |
BSF | 100,000,000 | | | 50,000,000 | |
Deferred finance charges | (5,873,053) | | | (7,066,153) | |
Total debt | 369,126,947 | | | 317,933,847 | |
| | | |
Less current portion | 97,500,000 | | | 50,000,000 | |
| | | |
Total long-term debt, less current portion | 271,626,947 | | | 267,933,847 | |
Deferred finance costs are comprised of SIDF loan origination charges which are capitalized and amortized over the period of the related loan which approximates the interest method. Loan fees of SR5,873,056 and SR7,066,153 net of accumulated amortization are included net with long-term debt at September 30, 2020 and December 31, 2019. Amortization of loan fees
amounted to approximately SR1,835,000, SR1,639,000, and SR1,639,000 for the nine months ended September 30, 2020 and the years ended December 31, 2019 and 2018, respectively.
The repayment schedule is as follows:
| | | | | |
Years Ending December 31, | |
| |
2020 | 50,000,000 | |
2021 | 86,666,668 | |
2022 | 91,666,668 | |
2023 | 96,666,664 | |
2024 | 50,000,000 | |
| |
| |
| 375,000,000 | |
Note 11 – End-of-Service Indemnities
| | | | | | | | | | | |
The change in the end-of-service indemnities provision is as follows: | | | |
| September 30, | | December 31, |
| 2020 | | 2019 |
Balance, beginning of period | 4,880,892 | | | 3,649,889 | |
Provision | 2,198,461 | | | 2,208,156 | |
Paid | (1,049,432) | | | (977,153) | |
Balance, end of period | 6,029,921 | | | 4,880,892 | |
Note 12 – Asset Retirement Obligations
During 2012, we recorded an ARO for deferred mine closure costs of approximately SR12,843,000. These deferred mine closure costs are being amortized over the estimated life of the mine. Amortization expense was approximately SR362,000, SR541,000, and SR745,000 for the nine months ended September 30, 2020 and the years ended December 31, 2019 and 2018.
| | | | | | | | | | | |
Deferred mine closure costs consisted of the following at: | | | |
| September 30, | | December 31, |
| 2020 | | 2019 |
Cost | 12,842,625 | | | 12,842,625 | |
Accumulated amortization | (7,993,376) | | | (7,631,120) | |
| | | |
| 4,849,249 | | | 5,211,505 | |
| | | | | | | | | | | | | | | | | |
A summary of changes in our provision for mine closure costs is as follows: | | | | | |
| September 30, | | December 31, |
| 2020 | | 2019 | | 2018 |
Balance, beginning of period | 16,625,347 | | | 16,063,136 | | | 15,519,938 | |
Accretion expense | 405,558 | | | 562,211 | | | 543,198 | |
| | | | | |
Balance, end of period | 17,030,905 | | | 16,625,347 | | | 16,063,136 | |
ARO costs may increase or decrease significantly in the future as a result of changes in regulations, changes in engineering designs and technology, permit modifications or updates, changes in mine plans, inflation or other factors and as actual reclamation spending occurs.
Note 13 – General and Administrative Expenses
| | | | | | | | | | | | | | | | | |
A summary of general and administrative expenses is as follows: | | | | | |
| September 30, | | December 31, |
| 2020 | | 2019 | | 2018 |
Wages, salaries and related costs | 7,823,013 | | | 18,701,126 | | | 17,036,965 | |
Mine closure and environmental | 767,814 | | | 1,306,705 | | | 1,287,698 | |
Office expenses and other | 6,494,431 | | | 8,831,910 | | | 9,287,218 | |
Travel and accommodation | 85,721 | | | 27,182 | | | 593,046 | |
Professional fees | 3,522,068 | | | 1,488,500 | | | 1,271,071 | |
| | | | | |
| 18,693,047 | | | 30,355,423 | | | 29,475,998 | |
Note 14 - Commitments and Contingencies
Operating lease obligations
Our lease commitment for our surface mining lease was initially granted for a period of 30 years through 2024. The lease allows for renewal for an additional 20 years. We also have leases for our corporate offices and three residential villas in Najran through 2025. There is also a mining lease that covers the Guyan area for a period of 20 years through 2034.
A summary of these commitments are as follows:
| | | | | |
Years Ending December 31, | |
| |
2020 | 247,500 | |
2021 | 990,000 | |
2022 | 990,000 | |
2023 | 550,000 | |
2024 | 550,000 | |
2025 | 110,000 | |
Thereafter | 990,000 | |
| |
| 4,427,500 | |
Capital lease obligations
We lease certain equipment vehicles under capital lease obligations that are set to expire at various dates through 2022. The future minimum lease payments under the capital lease obligations as of September 30, 2020:
| | | | | |
2020 | 723,727 | |
2021 | 2,791,921 | |
2022 | 1,482,543 | |
Total minimum lease payments | 4,998,191 | |
Less deferred financial charges | (496,193) | |
Total capital lease obligations | 4,501,998 | |
Less: current portion of capital lease obligations | 2,479,480 | |
Total long term portion, net current portion | 2,022,518 | |
Note 15 - Fair Value Measurement
Fair value accounting guidance includes a hierarchy that prioritizes the inputs to valuation techniques used to measure fair value. The hierarchy gives the highest priority to unadjusted quoted prices in active markets for identical assets or liabilities (Level 1 inputs) and the lowest priority to unobservable inputs (Level 3 inputs).
| | | | | |
Level 1 | Unadjusted quoted prices in active markets that are accessible at the measurement date for identical, unrestricted assets or liabilities; |
Level 2 | Quoted prices in markets that are not active, quoted prices for similar assets or liabilities in active markets, inputs other than quoted prices that are observable for the asset or liability, or inputs that are derived principally from or corroborated by observable market data by correlation or other means; and |
Level 3 | Prices or valuation techniques that require inputs that are both significant to the fair value measurement and unobservable (supported by little or no market activity). |
We did not have any significant transfers in or out of Levels 1, 2, or 3 in 2020 or 2019. The embedded derivatives in our provisional sales contracts are considered Level 2 measurements.